- There are no more items in your cart
- Shipping Calculated at checkout
- Sub-Total (inc. VAT) £0.00
Need Help?
Immersed Environment Primers
Shop our range of immersed environment primers and prepare metal substrates properly - steel, stainless steel, aluminium, galvanising, shop primed, thermally sprayed zinc - for compatible protective topcoats. Choose epoxy and chlorinated rubber solvent-based primers in single-pack and two-component sizes, all suited to atmospheric environments and application to underwater substrates.
Use the sidebar filter to find product attributes suited to your project, including holding primers, high solids, anti-corrosive properties, high build, and much more. Our immersed environment primers can also be filtered on their recoating times, ranging from 16 hours down to 4 hours. Click for more info.
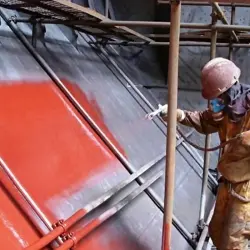
International Intergard 269
International Intergard 269 is a quick drying two component epoxy primer suitable for overcoating after prolonged periods of weathering, for use at both new construction and maintenance.As a blast holding primer suitable for use in immersed and exposed conditions and overcoatable with a wide range of high performance systems. For use at...

Jotun Penguard Primer
Jotun Penguard Primer is a two component polyamide cured high molecular weight epoxy coating designed as a primer for new construction. It can be used as a primer as a part of a complete system in atmospheric and immersed environments. Suitable for properly prepared carbon steel, stainless steel, aluminium, concrete, galvanised steel, shop...

Teamac Metaclor Underwater Primer
Matt grey modified chlorinated rubber primer. For multi-purpose use on steel, wood, and GRP. Can be applied underwater on prepared steel or as a sealer coat. Includes Zinc Phosphate for enhanced protection.

Rust-Oleum 9180 Epoxy Metal Primer
High-build two-component anti-corrosion primer available in Grey. For bare or blasted steel, galvanized substrates, and as an intermediate coat. High amount of rust inhibitors for enhanced protection. 1:1 mixing ratio. Touch dry in just 1 hour. Applied by brush, roller, or spray.
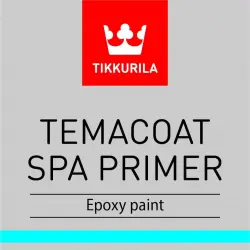
Tikkurila Temacoat SPA Primer
Tikkurila Temacoat SPA Primer, a two-component resin modified epoxy primer with anti-corrosive pigments with excellent adhesion to steel, zinc and aluminium surfaces, that can be applied in thick layers, thus enabling faster production.Has high solids content Used as a primer or an intermediate coat in paint systems exposed to abrasion...

PPG SigmaCover 295
Low-sheen red-brown epoxy primer. Good adhesion to steel and galvanized steel, industrial and marine applications. Suitable for touching up of weld seams and damages of epoxy coatings during construction. Can be overcoated with most alkyd-, chlorinated rubber-, vinyl-, epoxy- and two-component polyurethane coatings. Suitable on wet blast...

Jotun Jotacote F60 6A
A pure epoxy outfitting primer, suitable for use on a wide range of metal substrates as a primer, midcoat or finish coat in both atmospheric and immersed environments.Can be applied to carbon steel, stainless steel, galvanised steel, aluminium, GRP and thermally sprayed zinc Suitable temperature range from -196°C to +210°CPlease note:...
Need Help?
Need Help?
Immersed Environment Primers for metal surfaces provide essential protection for industries where metals are constantly exposed to water, chemicals, and other corrosive elements. These primers form the first layer of protection on metal substrates, preventing rust, corrosion, and long-term damage. For sectors such as marine, oil and gas, water treatment, and chemical processing, ensuring that metal surfaces remain intact and functional is critical. Immersed Environment Primers are formulated to offer the best possible adhesion, durability, and resistance in some of the most challenging environments.
What Are Immersed Environment Primers?
Immersed Environment Primers are specially engineered coatings designed to protect metal surfaces that are submerged in liquids or exposed to high levels of moisture and corrosive elements. Metals such as steel and iron are highly susceptible to oxidation, which causes rust and leads to structural failure. The risk of corrosion is significantly heightened when metal components are used in submerged or partially submerged conditions, such as marine environments, pipelines, water treatment facilities, or chemical plants.
These primers form a protective barrier between the metal and its environment, preventing direct contact with moisture and oxygen—both primary agents of corrosion. By adhering to the metal surface, these primers create an impermeable layer that stops corrosion at its source. Immersed Environment Primers are designed to work alongside topcoats, creating a comprehensive coating system that ensures the long-term protection of metal surfaces in even the most aggressive environments.
Modern formulations include innovations that allow these primers to withstand not only water and humidity but also the chemical elements often found in industrial and marine environments. Their complex compositions allow them to bond more effectively with the substrate, offering lasting protection where regular primers might fail.
Why Are They Essential for Metal in Immersed Conditions?
When metal is submerged or exposed to moisture for extended periods, it becomes highly susceptible to several types of corrosion. The combination of water, oxygen, and electrolytes can lead to pitting, crevice corrosion, and galvanic corrosion, all of which weaken the metal over time. Unchecked corrosion results in equipment failure, posing safety risks, operational downtimes, and substantial financial costs in repairs and replacements.
Immersed Environment Primers play a crucial role in safeguarding metal structures in such environments. These primers offer the following critical advantages:
- Corrosion Prevention: The core function of these primers is to prevent corrosion by isolating the metal surface from water, oxygen, and other corrosive agents. This ensures that the metal remains free from rust and degradation, even in environments that are consistently exposed to moisture and chemicals.
- Superior Adhesion: Immersed Environment Primers are formulated with advanced bonding agents that ensure a tight grip to metal surfaces. This strong adhesion is vital, particularly in submerged or high-moisture conditions, where weaker primers may lift or peel over time.
- Chemical Resistance: In industries such as wastewater treatment, chemical processing, and oil and gas, metal surfaces are exposed to harsh chemicals that can quickly degrade unprotected metal. Immersed Environment Primers are chemically resistant, ensuring that the substrate remains intact and shielded from corrosive chemical agents.
- Extended Service Life: These primers extend the operational life of metal components by preventing corrosion-related damage. Equipment protected by these primers can remain in service longer, reducing the need for frequent maintenance or early replacement.
- High-Temperature and Pressure Resistance: In some submerged environments, metal surfaces are exposed to significant temperature fluctuations and water pressure. Immersed Environment Primers are formulated to withstand these extremes, providing consistent protection regardless of environmental conditions.
- Environmental Protection: Modern primers are also designed with an eye towards environmental safety. They often have low VOC (Volatile Organic Compound) emissions and comply with stringent industry standards for environmental impact, offering a balance between performance and sustainability.
Where Are Immersed Environment Primers Used?
These primers are indispensable in a variety of industrial applications, particularly where metal surfaces are exposed to water, chemicals, and fluctuating environmental conditions. Some of the key sectors that rely on Immersed Environment Primers include:
Marine Industry
The marine sector is perhaps one of the most obvious industries that benefit from Immersed Environment Primers. Metal structures such as ships, boats, offshore platforms, docks, and underwater pipelines are in constant contact with seawater. The salt in seawater accelerates corrosion, especially in the case of metals like steel. Without proper protection, the structural integrity of marine vessels and platforms would quickly deteriorate. Immersed Environment Primers create a protective layer that shields metal surfaces from the aggressive corrosion caused by saltwater.
Oil and Gas Industry
Oil rigs, pipelines, and storage tanks are often exposed to both water and chemicals in the oil and gas sector. Whether these components are used offshore or in refineries, their proximity to water and aggressive chemicals poses a constant threat of corrosion. The metal infrastructure must be protected to ensure that oil and gas are transported and stored safely. Immersed Environment Primers in these settings prevent not only corrosion but also damage from hydrocarbons and other chemical agents. By protecting pipelines and storage tanks, these primers reduce the risk of leaks and failures that could have catastrophic environmental and financial consequences.
Water Treatment Facilities
Water treatment plants, both for drinking water and wastewater, involve constant exposure of metal components to water and corrosive chemicals. Whether it’s the metal surfaces in water filtration systems, storage tanks, or pipelines, these metals need strong protection against both rust and chemical degradation. Immersed Environment Primers in this industry provide critical resistance to the chemical composition of both fresh and wastewater, ensuring the longevity of the treatment infrastructure.
Chemical Processing Plants
Chemical processing involves the storage and transportation of aggressive chemical substances, many of which can rapidly corrode metal. Metal storage tanks, pipelines, and machinery within these plants face constant exposure to acids, bases, and other corrosive chemicals. Immersed Environment Primers protect the metal surfaces in these plants by forming a robust barrier that resists chemical attack and prevents corrosion. This ensures that equipment continues to function safely and efficiently for longer periods.
Civil Engineering and Infrastructure
In the construction of bridges, dams, and other large-scale infrastructure projects, metal components are often exposed to water for long periods. For example, bridges may be subject to high humidity, rain, or even complete submersion in water, depending on their location. Immersed Environment Primers protect these metal components from rusting, which could compromise the structural integrity of the entire project. In civil engineering, the long-term durability of these primers is crucial for ensuring that infrastructure remains safe and functional over time.
Top Features to Consider When Purchasing Immersed Environment Primers
When selecting the appropriate Immersed Environment Primer for a specific application, several important features must be taken into account to ensure optimal performance and long-lasting protection. Below are the top features to consider:
- Adhesion: The primer’s ability to adhere to the metal substrate is one of the most critical features. Without proper adhesion, the primer will fail to provide the necessary protective barrier. Immersed Environment Primers are designed to offer superior adhesion to a wide range of metal substrates, including steel and aluminium. This strong bond ensures that the primer remains in place even in submerged or high-moisture environments.
- Corrosion Resistance: The core function of any Immersed Environment Primer is to prevent corrosion. The best primers not only block moisture and oxygen but also contain corrosion inhibitors that actively protect the metal surface. In industries such as marine and oil and gas, where the risk of corrosion is exceptionally high, this feature is of paramount importance.
- Chemical Resistance: In many industrial applications, metal surfaces are exposed to aggressive chemicals, which can cause rapid deterioration if not properly protected. Primers with strong chemical resistance are essential in settings like chemical processing plants, where metal surfaces may come into direct contact with acidic or caustic substances. These primers are formulated to withstand chemical exposure and prevent damage to the underlying metal.
- Durability: Immersed Environment Primers must be durable enough to withstand the harsh conditions they are designed for. This includes not only corrosion and chemical resistance but also the ability to endure fluctuating temperatures, pressure changes, and prolonged exposure to moisture. A durable primer will ensure long-lasting protection, reducing the need for frequent maintenance or reapplication.
- Compatibility with Topcoats: Immersed Environment Primers are often used in combination with topcoats to provide a multi-layered protective system. When selecting a primer, it is important to ensure that it is compatible with the topcoat that will be used. This compatibility will ensure a seamless bond between the primer and topcoat, creating an even stronger barrier against corrosion and chemical attack.
- Fast Drying Time: In industrial settings where time is of the essence, the drying time of the primer can significantly impact project timelines. Many modern Immersed Environment Primers offer fast drying times, allowing for quicker application and faster return to service. This feature is particularly beneficial in large-scale projects where downtime can be costly.
- Flexibility: Some primers are designed to be flexible, meaning they can expand and contract along with the metal substrate as temperatures fluctuate. This flexibility is particularly important in environments where the metal may be exposed to extreme temperature changes. Flexible primers are less likely to crack or peel, ensuring long-lasting protection.
- Waterproofing Properties: Many Immersed Environment Primers are designed to provide additional waterproofing benefits, preventing water from penetrating the surface of the metal. This feature is especially useful in submerged environments, where the constant presence of water could otherwise lead to corrosion and rust.
- Low VOC Emissions: For industries that prioritise environmental sustainability, low VOC (Volatile Organic Compound) emissions are an important consideration. Modern Immersed Environment Primers are often formulated with reduced VOC content to minimise their environmental impact. This feature is essential for companies that operate under strict environmental regulations or that seek to reduce their overall carbon footprint.
- Temperature and Pressure Resistance: In environments where metal components are exposed to high temperatures or pressures, such as deep-sea structures or pipelines, the primer must be capable of withstanding these conditions. Immersed Environment Primers designed for extreme environments offer enhanced resistance to both high and low temperatures as well as elevated pressures.
Common Uses of Immersed Environment Primers
Immersed Environment Primers are versatile products that provide critical protection for metal surfaces across a wide range of industries and applications. Their ability to prevent corrosion in submerged or moisture-heavy environments makes them indispensable for maintaining the structural integrity of metal components in challenging conditions. Below is an expanded, in-depth look at some of the most common uses for these primers, along with additional examples that highlight their importance in various sectors.
Marine Vessels and Offshore Structures
The marine industry is one of the largest users of Immersed Environment Primers due to the constant exposure of metal structures to saltwater, which is highly corrosive. Marine vessels, including cargo ships, fishing boats, ferries, and cruise liners, all rely on these primers to protect their hulls, propellers, and other underwater metal components from rust and corrosion. Offshore structures such as oil rigs, drilling platforms, and underwater pipelines are similarly exposed to the harsh ocean environment.
For instance, offshore oil rigs are often submerged partially or fully in seawater for decades, meaning their metal foundations and frameworks must be protected to ensure they don’t weaken over time. Immersed Environment Primers are applied to these structures to shield them from the corrosive effects of saltwater, ensuring they remain stable and operational. Additionally, marine terminals, piers, and docks, which are frequently in contact with seawater, use these primers to extend the life of metal supports and reinforcements.
In yacht and pleasure boat industries, where aesthetics and performance matter, applying Immersed Environment Primers on the metal hulls can prevent corrosion without compromising speed or functionality. Given that saltwater accelerates oxidation, the protection provided by these primers is critical for all marine environments, whether industrial or recreational.
Oil and Gas Pipelines and Storage Tanks
In the oil and gas industry, metal pipelines and storage tanks face a dual threat of internal and external corrosion. Internally, the hydrocarbons they transport can be highly corrosive, while externally, they are often exposed to water, chemicals, and extreme weather conditions. Immersed Environment Primers are applied both internally and externally on metal pipelines and storage tanks to prevent corrosion, protect structural integrity, and ensure the safe transportation and storage of oil, gas, and other chemicals.
For example, offshore oil pipelines that run underwater are exposed to saltwater, which accelerates corrosion. These pipelines, which can extend for hundreds of miles, rely on Immersed Environment Primers to ensure their longevity. Without these primers, the risk of leaks or ruptures would be significantly higher, leading to potential environmental disasters. In refineries, large metal storage tanks that store crude oil or refined products are exposed to fluctuating temperatures and moisture. Applying these specialised primers on both the inside and outside of the tanks ensures that the metal remains free of rust, extending the tank’s operational life.
In addition, pipelines used to transport water or chemicals across long distances often pass through underground environments where moisture, soil acidity, and other factors increase the risk of corrosion. Immersed Environment Primers provide a protective layer that shields these pipelines from both natural and chemical corrosion, reducing the likelihood of damage and the costly repairs that would follow.
Water and Wastewater Treatment Facilities
In water and wastewater treatment plants, the use of metal components such as pipes, tanks, and filtration systems is widespread. These metal surfaces are constantly exposed to moisture, chemicals, and varying pH levels, making them vulnerable to both rust and chemical corrosion. Immersed Environment Primers are critical for preventing corrosion in these facilities, ensuring that water is treated and transported efficiently and safely.
For example, in a wastewater treatment plant, metal pipes and tanks are used to convey and store treated and untreated water. The wastewater often contains corrosive chemicals, acids, and organic matter that can rapidly degrade unprotected metal surfaces. By applying Immersed Environment Primers, these metal surfaces are protected from both chemical and microbial corrosion, ensuring that the plant operates smoothly and that the metal components last for many years.
Similarly, drinking water treatment facilities rely on these primers to protect the metal surfaces in contact with water, such as storage tanks and distribution pipelines. Any corrosion in these systems could lead to contamination of the drinking water supply, making the protection provided by these primers critical for public health.
In addition, sewage treatment plants, where metal components are constantly submerged or exposed to aggressive chemicals and gases like hydrogen sulphide, require these primers to protect against the rapid deterioration of pipes, valves, and holding tanks.
Bridges, Tunnels, and Other Civil Engineering Projects
Civil engineering projects such as bridges, tunnels, and dams often involve the use of metal components that are exposed to high moisture levels, water, or even full submersion. These projects rely on the long-term structural integrity of the metal used in their construction, making corrosion prevention crucial. Immersed Environment Primers are applied to protect the metal surfaces in these structures from rust and degradation, helping to ensure the safety and longevity of the project.
For example, many modern bridges feature steel girders and supports that are exposed to rain, humidity, and water splashes from rivers or coastal areas. Without proper protection, these metal components would corrode, leading to structural weakness and safety hazards. By applying Immersed Environment Primers, the risk of corrosion is significantly reduced, allowing these bridges to remain strong and functional for decades. Even the submerged portions of bridge supports, which are often difficult to access, can be protected by these primers to prevent rust from weakening the structure.
In tunnel construction, particularly under-river or under-sea tunnels, metal reinforcements are often used to stabilise the tunnel walls. These metal components are in constant contact with moisture and groundwater, making them prone to corrosion. Immersed Environment Primers protect these reinforcements, ensuring that the tunnel remains structurally sound over time.
Similarly, dams and water barriers often use metal gates, sluices, and other components that come into direct contact with water. In these environments, constant exposure to water—whether fresh or saltwater—can cause metal to corrode rapidly. Immersed Environment Primers are applied to these metal surfaces to ensure that they remain corrosion-free, maintaining the safety and functionality of the dam.
Industrial and Chemical Processing Plants
In industrial and chemical processing plants, metal surfaces are exposed to a variety of aggressive chemicals, high temperatures, and moisture. These conditions can cause rapid corrosion, leading to equipment failure and production downtime. Immersed Environment Primers are used to protect metal components in these plants from both corrosion and chemical attack, ensuring that the equipment remains operational and safe.
For example, in chemical plants, metal storage tanks, pipes, and reactors are often exposed to strong acids, bases, and solvents. These chemicals can corrode unprotected metal surfaces, leading to leaks, safety hazards, and costly repairs. By applying Immersed Environment Primers, these metal surfaces are shielded from chemical attack, ensuring that they remain corrosion-free and operational for extended periods. This is particularly important in industries such as petrochemicals, where any failure in metal containment systems could result in environmental and safety disasters.
In addition to storage tanks and pipelines, processing equipment such as heat exchangers, condensers, and reactors also benefit from the protection offered by these primers. These pieces of equipment are often subjected to extreme conditions, including high pressures, temperatures, and chemical exposure. Immersed Environment Primers provide the necessary protection to ensure that these critical components function effectively without suffering from premature corrosion.
Additional Examples of Common Uses
Beyond these key industries, Immersed Environment Primers also find application in several other sectors where metal surfaces are exposed to water, chemicals, or extreme environmental conditions:
- Mining Industry: In mining operations, metal equipment such as conveyors, cranes, and loaders are often exposed to water and chemicals during the extraction and processing of minerals. Immersed Environment Primers protect this equipment from corrosion, extending its operational life and reducing maintenance costs.
- Power Generation: In hydroelectric power plants, where metal turbines, gates, and support structures are constantly submerged in water, these primers are essential for preventing corrosion and ensuring the efficiency of power generation systems.
- Agriculture: Irrigation systems and agricultural machinery that are exposed to water, fertilisers, and other chemicals rely on Immersed Environment Primers to prevent rust and extend the life of metal components.
- Food and Beverage Processing: In food and beverage plants, metal tanks, pipes, and conveyors are exposed to water and cleaning chemicals. Immersed Environment Primers protect these surfaces from corrosion, ensuring food safety and hygiene while also extending equipment life.
In each of these examples, the primary function of Immersed Environment Primers is to prevent corrosion, but the specific conditions and challenges of each industry require tailored solutions. Whether exposed to seawater, chemicals, or industrial by-products, the role of these primers is critical in preserving the integrity and safety of metal structures.
For additional assistance in selecting the right primer for your specific application, contact the technical support team to ensure product compatibility and optimal performance.
FAQs About Immersed Environment Primers
- Can Immersed Environment Primers be applied in damp conditions? Yes, many Immersed Environment Primers are formulated for application on surfaces that are slightly damp, making them ideal for use in environments where completely dry conditions are difficult to achieve. However, it is important to check the product's technical data sheet to confirm its suitability for damp application.
- What is the typical thickness of a primer coat? The recommended thickness of the primer coat depends on the specific product and application environment. Generally, Immersed Environment Primers are applied in layers ranging from 50 to 150 microns. The required thickness can vary based on the degree of protection needed.
- Is surface preparation necessary before applying these primers? Yes, proper surface preparation is essential for ensuring that the primer adheres well to the metal surface. Common preparation methods include sandblasting, grinding, or chemical cleaning to remove rust, dirt, and other contaminants.
- How long does the protection last after application? The longevity of the protection depends on the environmental conditions and the specific product used. In many cases, Immersed Environment Primers can provide protection for several years when applied and maintained correctly.
- Can these primers be used in freshwater environments as well as saltwater? Yes, Immersed Environment Primers are effective in both freshwater and saltwater environments. However, products designed for saltwater environments often contain additional corrosion inhibitors to address the higher corrosive nature of seawater.
For additional assistance in selecting the right primer for your specific application, contact the technical support team to ensure product compatibility and optimal performance.