- There are no more items in your cart
- Shipping Calculated at checkout
- Sub-Total (inc. VAT) £0.00
Carboline Plasite 7122 HAR is a two-component, lining-grade epoxy which has wide chemical resistance and is suitable for use as a chemically resistant coating for aggressive atmospheric exposures or as a lining for a variety of chemical exposures.
- Versatile coating with wide chemical resistance
- Excellent abrasion resistance
- Excellent resistance to fuels
- Long history of performance
- Cure for service in 7 days (at 21°C)
This product is only available as PRICE ON APPLICATION - For more information and to place an order please contact us on 0113 2455450 or email [email protected].
Carboline Plasite 7122 HAR is a two-component, lining-grade epoxy has wide chemical resistance and is suitable for use as a chemically resistant coating for aggressive atmospheric exposures or as a lining for a variety of chemical exposures. It is suitable for use in food-grade service where product purity (taste and odour) are critical. It has excellent abrasion and thermal shock resistance.
Click To Jump To Section:
- Features and Benefits
- Product Specification
- Drying Times
- Surface Preparation
- Application Methods
- Health and Safety
Features and Benefits
- Versatile coating with wide chemical resistance
- Excellent abrasion resistance
- Excellent thermal shock resistance
- Excellent resistance to fuels
- Cure for service in 7 days (at 21°C)
- Long history of performance
- Self-priming
Product Specification
Technical Data | |
---|---|
Carboline Plasite 7122 HAR | |
Volume Solids: | By Volume 56% +/- 2% |
Theoretical Coverage Rate: | 19.7 m²/l at 25 microns (802 ft²/gal at 1.0 mils) 3.3 m²/l at 150 microns (134 ft²/gal at 6.0 mils) 2.8 m²/l at 175 microns (115 ft²/gal at 7.0 mils) |
Allow for loss in mixing and application | |
Dry Film Thickness: | 152 - 178 microns (6 - 7 mils) per coat Two multi-pass spray coats will produced 12-15 mil/300-375 micron DFT - recommended for immersion service |
VOC Values: | As Supplied: 400 g/l Plasite Thinner 71: Thinned 10%: 437 g/l VOC content varies between colours. Contact Rawlins on Tech - 0113 2455450 (option 2) or [email protected] for VOC of specific colours |
Dry Temp. Resistance: | Non-Continuous: 204°C (400°F) This product is not normally recommended for high temperature service, but will tolerate short excursions to 204°C (400°F) |
Flash Point: | Part A: -4°C (24.8°F) Part B: 999°C (1830°F) Part C: 59°C (138°F) |
Shelf Life: | 24 months Material stock can be turned upside down every 3 months to aid in ease of mixing |
Storage Temperature and Humidity: | 10-24°C (50-75°F) |
Drying Times
Curing Schedule | ||||
---|---|---|---|---|
Surface Temp | Dry to Recoat | Final Cure | ||
21°C (70°F) | 10 Hours | 7 Days | ||
29°C (85°F) | 6 Hours | 5 Days |
- Within 24 hours after coating is applied a minimum substrate temperature of 21°C (70°F) is required for proper polymerization
Curing Schedule | ||||
---|---|---|---|---|
Surface Temp | Dry to Recoat | |||
54°C (130°F) | 18 Hours | |||
60°C (140°F) | 10 Hours | |||
66°C (150°F) | 6 Hours | |||
77°C (170°F) | 3.5 Hours | |||
88°C (190°F) | 2 Hours |
- The chart above outlines the cure for service (immersion) times when the Force Cure schedule below is followed
Force Cure
- NOTE: Temperatures listed for 130°F and above are for force cure
- Force curing at elevated temperature will increase resistance to certain exposures. When exposure is severe, force curing is recommended to obtain maximum resistance and service life
- Allow an air-dry time of 2-5 hours @ 21-37°C before heat curing. After air drying the substrate temperature should be raised by approximately 15°C each 30 minutes until the desired force cure temperature is reached
- Final cure may be checked by exposing coated surface to MIBK for ten minutes. If no dissolving and only minor softening of film occurs the curing can be considered complete. The film should reharden after exposure if cured
Surface Preparation
Steel
- Immersion Service or Aggressive Chemical Exposures (Spill/Fume)
- Abrasive clean to an SSPC-SP10 or NACE No. 2 (Near-White metal surface)
- Profile: 25-75 microns
- Non-Immersion (Atmospheric)
- Preferred: SSPC-SP6; Where abrasive blasting is not permitted or practical, clean per SSPC-SP3 to yield a rough (non-polished) surface
Galvanised Steel
- Contact Rawlins on Tech - 0113 2455450 (option 2) or [email protected]
Aluminium
- Surface shall be clean and grease free with a blast produced anchor pattern or “tooth” as described earlier under steel. In addition, the blasted surface shall be given a chemical treatment
- For immersion, blasting with sharp grit followed by the chemical surface treatment is required
Concrete or CMU
- Contact Rawlins on Tech - 0113 2455450 (option 2) or [email protected] for recommendations
Application Methods
Product Information | |
---|---|
Mixing: | Mix the Part A and part C separately, then add the Part C to the Part A and mix thoroughly. The B (powder) can then be mixed slowly into the liquid. The mixture should stand approximately 30 minutes to "sweat in" before use |
Thinning: | Thinning will be necessary to spray this coating Thin up to 10% for normal temperatures and add up to 20% thinner for higher temperatures if necessary Use Plasite Thinner 71 (a medium-fast thinner) for internal tank lining; and Plasite Thinner 19 (a slower thinner) for exterior (hot or windy) conditions |
Pot Life: | 24 hours at 21°C and less at higher temperatures |
Spray Application (General): | Spray gun should provide an 8-12 inch-wide spray pattern with best possible atomization. Apply a “mist” bonding pass. Allow to dry approximately one minute but not long enough to allow film to completely dry Apply crisscross multi-passes, moving gun at fairly rapid rate, maintaining a wet appearing film. Observe the coating surface, and when it appears to be flowing together you will have an average 150-175 microns wet film. By allowing the solvents to flash-off for a few minutes, several faster multi-passes may be applied until you have a film thickness of approximately 150-175 microns - approximately 10-12 wet mils. Repeat above procedure for second coat-obtain a film of 250-300 microns DFT |
Conventional Spray: | Air pressure: 50 psi at the gun Pot Pressure: 10-15 psi |
Airless Spray: | Fluid Pressure: 1500-1800 psi Tip Size: 0.015-0.021 inches |
Brush: | Recommended for small areas and repairs only. Use a high-quality brush and apply a very light crisscross brush coat. Allow to dry for approximately 5 minutes. Then apply a heavy coat using a crisscross brush pattern. “Flow” the coating on rather than try to “brush out.” Allow to dry tack free. Repeat until sufficient film thickness is obtained. Normally a film thickness of 62-75 microns can be obtained per coat by this method Note: must be agitated frequently |
Health and Safety
Clean Up
- Use Carboline Thinner 71
- In case of spillage, absorb and dispose of in accordance with local applicable regulations
Safety
- Observe the precautionary notices on the container label, and read the Material Safety Data Sheet before use
- Employ normal workmanlike safety precautions
Ventilation
- When used in enclosed areas, thorough air circulation must be used during and after application until the coating is cured.
- The ventilation system should be capable of preventing the solvent vapor concentration from reaching the lower explosion limit for the solvents used
- User should test and monitor exposure levels to ensure all personnel are below guidelines
- If not sure or if not able to monitor levels, use MSHA/NIOSH approved supplied air respirator
Caution
- Fire and explosion hazards: This product contains less than 1% volatile components, however, vapours are heavier than air and can travel long distances, ignite and flash back
- Eliminate all Ignitions sources. Keep away from sparks and open flames
- All electrical equipment and installations should be made and grounded in accordance with applicable local regulations
- In areas where explosion hazards exist, workers should be required to use non-ferrous tools and wear conductive and non-sparking shoes
- Refer to the product data sheet and safety data sheets in the attachments section above for further details
Data sheet
- Manufacturer
- Carboline
- For Use On
- Steel, Galvanized Steel, Aluminium, Concrete
- Application Method
- Brush, Spray
- Sheen
- Semi-Gloss
- Colour
- Standard / Ready Mixed
- Single, Two or Three Pack
- Three-Pack
- Pack Size
- 3.79L Kit, 19.93L Kit
- Coverage
- 19.7 m²/l at 25 microns (802 ft²/gal at 1.0 mils), 3.3 m²/l at 150 microns (134 ft²/gal at 6.0 mils), 2.8 m²/l at 175 microns (115 ft²/gal at 7.0 mils)
- Recommended Thinner/Cleaner
- Carboline Thinner 71
- Solids by Volume
- 56% +/- 2%
- Heat Resistance (up-to)
- 204°C Non-Continuous
- VOC
- As Supplied: 400 g/l
- Shelf Life (from date of manufacture)
- 24 months
- Recommended Dry Film Thickness
- 152 - 178 microns (6 - 7 mils) per coat
- UN Number (Activator)
- UN3470
- UN Number (Base)
- UN1263
- Pot Life
- 24 hours at 70°F (21°C) and less at higher temperatures
- Dry to Recoat
- 21°C: 7 Days - 29°C: 5 Days
- Fully Cured
- 21°C: 5 Days - 29°C: 5 Days
- Suitable For Use On
- Aluminium
- Suitable For Use On
- Steel
- Suitable For Use On
- Galvanised Steel
- Suitable For Use On
- Concrete
- Finish
- Semi-Gloss
- Application Method
- Brush
- Application Method
- Spray
- Product Usage Type
- Tank Lining
- Product Range
- Plasite
Questions
Question about the product
Be the first to ask a question about this product!
IMPORTANT SHIPPING & DELIVERY INFORMATION
Carboline Plasite 7122 HAR is only available with the shipping and delivery timescales listed below - please do not contact our Customer Support Team with enquiries about alternative or earlier shipping and delivery times.
Saturdays and Sundays, as well as Bank Holidays, are not classed as working days.
Orders placed after the cut-off for this product will not be processed for earliest dispatch until 9am the next working day.
All delivery costs below are excluding VAT
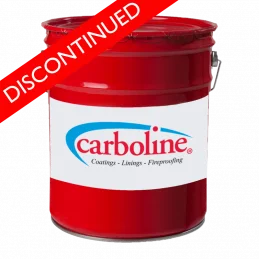
Carboline Thinner 19
We no longer stock this product; please contact our technical team on 0113 2455450 (option 2) or send a message to [email protected] where we will be happy to find an alternative product.

Surface Preparation Kits for Steel
These surface preparation kits for steel have been created to help provide customers with an easily accessible bundle of tools to aid in the preparation of steel surfaces in accordance with ISO 8501-1 (St2/3) and SSPC (SP 2/3). Please click here for important information about these kits. Kit Contents: SET 1 (Hand Tools)1 x Rust-Oleum...