- There are no more items in your cart
- Shipping Calculated at checkout
- Sub-Total (inc. VAT) £0.00
Carboline Plasite 7159 HAR is a two-component, water-resistant epoxy coating polymerized with a polyamine type curing agent. A high-performance lining for elevated temperature and pressure immersion services in high purity water, as well as the oil/water separating processes encountered in the petroleum industry. This HAR version of Plasite 7159 is extremely abrasion resistant.
- Easy-to-apply high performance thin film lining
- Protects I high temperature demineralized water immersion - 100°C
- Recommended in high pressure three phase service up to 121°C
- Cure for service in 7 days (at 21°C)
- Resists strong oxidizer and acid immersion
- Can be air dried or force cured for prompt service
- Outstanding abrasion resistance
This product is only available as PRICE ON APPLICATION - For more information and to place an order please contact us on 0113 2455450 or email [email protected].
Carboline Plasite 7159 HAR is a two-component, water-resistant epoxy coating polymerized with a polyamine type curing agent. A high-performance lining for elevated temperature and pressure immersion services in high purity water, as well as the oil/water separating processes encountered in the petroleum industry. This HAR version of Plasite 7159 is extremely abrasion resistant.
Click To Jump To Section:
- Features and Benefits
- Product Specification
- Drying Times
- Surface Preparation
- Application Methods
- Health and Safety
Features and Benefits
- Easy-to-apply high performance thin film lining
- Protects I high temperature demineralized water immersion - 100°C
- Recommended in high pressure three phase service up to 121°C
- Cure for service in 7 days (at 21°C)
- Resists strong oxidizer and acid immersion
- Can be air dried or force cured for prompt service
- Outstanding abrasion resistance
Product Specification
Technical Data | |
---|---|
Carboline Plasite 7159 HAR | |
Volume Solids: | 68% +/- 2% |
Theoretical Coverage Rate: | 26.8 m²/l at 25 microns 5.4 m²/l at 125 microns 4.5 m²/l at 150 microns |
Allow for loss in mixing and application | |
Dry Film Thickness: | 127 - 152 microns per coat A total film thickness of 250-300 microns is required for immersion service |
VOC Values: | As Supplied: 278 g/l ± 2% Plasite Thinner 19: 332 g/l ± 2% Plasite Thinner 71: 327 g/l ± 2% VOC Content varies between colours Contact Rawlins on Tech - 0113 2455450 (option 2) or [email protected] for VOC of specific colours |
Dry Temp. Resistance: | Non-Continuous: 177°C Continuous immersion temperature and pressure limitations have been established for certain exposures Please contact Rawlins for specific recommendations |
Flash Point: | Part A: 22°C Part B: 104°C |
Shelf Life: | Part A - 24 months at 21°C Part B - 9 months at 21°C Part B material in stock should be turned upside down every three months |
Drying Times
Curing Schedule | |
---|---|
Surface Temp | Cure for Service |
10°C | 14 Days |
16°C | 10 Days |
21°C | 7 Days |
- With adequate ventilation when applying at temperatures above 21°C coating surfaces will normally be tack free in 2-4 hours
Curing Schedule | |
---|---|
Surface Temp | Cure for Most Immersion Services |
54°C | 18 Hours |
60°C | 10 Hours |
66°C | 6 Hours |
71°C | 4 Hours |
77°C | 4 Hours |
82°C | 2 Hours |
88°C | 2 Hours |
93°C | 2 Hours |
- The chart above outlines the cure for service (immersion) times when the force cure schedule below is followed
Force Cure
- Note: Temperatures listed for 54°C and above are for force cure
- Force curing at elevated temperature will increase resistance to certain exposures. When exposure is severe, force curing is recommended to obtain maximum resistance and service life
- Allow an air-dry time of 16-24 hours @ 10-21°C before heat curing. When applying at temperatures above 21°C allow 2-5 hours air-dry time
- After air-drying, the substrate temperature should be raised by approximately 17°C each 30 minutes until the desired force cure temperature is reached
- Final cure may be checked by exposing coated surface to MIBK for ten minutes. If no dissolving and only minor softening of film occurs the curing can be considered complete. The film should re-harden after exposure if cured
Surface Preparation
Preparation | |
---|---|
General: | Remove any oil or grease from surface to be coated in accordance with SSPC-SP1 |
Steel: | SSPC-SP10 Surface Profile should be dense angular 50-75 µ (2.0-3.0 mils) |
Aluminium: | Surface shall be clean and grease free with a blast produced anchor pattern or “tooth” as described earlier under steel In addition, the blasted surface shall be given a chemical treatment |
Stainless Steel: | Profile should be dense angular 50-75 µ (2.0-3.0 mils) Remove all surface contaminants that would interfere with the performance of stainless steel for the intended service such as, but not limited to, imbedded iron or chlorides |
Application Methods
Product Information | |
---|---|
Mixing: | Thoroughly mix part A and B separately, then add part B slowly to the part A and mix completely The coating should stand approximately 30 minutes after the curing agent has been thoroughly mixed in |
Thinning: | PLASITE Thinner 71 is recommended for normal application temperatures and conditions PLASITE Thinner 19 is recommended for above normal application temperatures and where tank design requires a slower evaporating thinner to help control overspray The amounts of thinner required will vary depending on air and surface temperatures and application equipment Normal application temperatures and conditions will require the addition of approximately 10% by volume with approximately 5% additional thinner added for each 3°C of increased temperature. Airless spray equipment and above normal temperatures require additional thinning It is recommended that the thinner included on each order amount to approximately 20% of the coating order |
Ratio: | 4:1 A:B |
Pot Life: | Approximately 8 to 10 hours at 21°C |
Conventional Spray: | Pressure pot equipped with dual regulators, 3/8” I.D. minimum material hose, .070” I.D. fluid tip and appropriate air cap Adjust air pressure to approximately 50 psi at the gun and provide 5-10 lbs of pot pressure. Agitate material during spray |
Airless Spray: | Note: Conventional spray is recommended for 7159 HAR because it can be abrasive to tips and equipment Pump Ratio: 30:1 (min.) GPM Output: 2.5 (min.) Material Hose: 3/8” I.D. (min.) Tip Size: .015”-.021” Output PSI: 1500-1800 Filter Size: 60 mesh |
Brush: | Recommended for small areas only. Use medium bristle brush Not recommended for tank lining applications except when striping welds Avoid excessive re-brushing for best results |
Roller: | Not recommended for tank lining applications except when striping welds Use a short-nap synthetic roller with phenolic core |
General: | Apply a “mist” bonding pass Allow to dry approximately one minute but not long enough to allow film to completely dry. Apply crisscross multi-passes, moving gun at fairly rapid rate, maintaining a wet appearing film. Fast multi-passes may be applied until you have a wet film thickness of approximately 150-200 µ (6-8 mil). Repeat this procedure for the second coat to obtain an 200-300 µ (8-12 mil) DFT Call Rawlins on Tech - 0113 2455450 (option 2) or [email protected] with any questions |
Health and Safety
Clean Up
- Use Carboline Thinner 71, Thinner 2, or Acetone
- In case of spillage, absorb and dispose of in accordance with local applicable regulations
Safety
- Observe the precautionary notices on the container label, and read the material safety data sheet before use
- Employ normal workmanlike safety precautions
Ventilation
- When used in enclosed areas, thorough air circulation must be used during and after application until the coating is cured.
- The ventilation system should be capable of preventing the solvent vapor concentration from reaching the lower explosion limit for the solvents used
- User should test and monitor exposure levels to ensure all personnel are below guidelines
- If not sure or if not able to monitor levels, use MSHA/NIOSH approved supplied air respirator
- Refer to the product data sheet and safety data sheets in the attachments section above for further details
Data sheet
- Manufacturer
- Carboline
- For Use On
- Steel, Stainless Steel, Aluminium
- Application Method
- Brush, Roller, Spray
- Colour
- Standard / Ready Mixed
- Single, Two or Three Pack
- Two-Pack
- Pack Size
- 3.79L Kit, 18.98L Kit
- Mixing Ratio
- 4:1 A:B
- Coverage
- 26.8 m²/l at 25 microns, 5.4 m²/l at 125 microns, 4.5 m²/l at 150 microns
- Recommended Thinner/Cleaner
- Carboline Thinner 71. Thinner 2
- Solids by Volume
- 68% +/- 2%
- Heat Resistance (up-to)
- Non-Continuous: 177°C
- VOC
- As Supplied: 278 g/l ± 2%
- Shelf Life (from date of manufacture)
- Part A - 24 months at 21°C, Part B - 9 months at 21°C
- UN Number (Activator)
- UN3082
- UN Number (Base)
- UN1263
- Pot Life
- Approximately 8 to 10 hours at 21°C
- Fully Cured
- 10°C: 14 Days, 16°C:10 Days, 21°C: 7 Days
- Fully Cured
- 10°C: 14 Days, 16°C:10 Days, 21°C: 7 Days
- Suitable For Use On
- Aluminium
- Suitable For Use On
- Stainless Steel
- Suitable For Use On
- Steel
- Application Method
- Roller
- Application Method
- Spray
- Application Method
- Brush
- Product Usage Type
- Tank Lining
- Product Range
- Plasite
- For Tanks or Pipes
- Tank
Questions
Question about the product
Be the first to ask a question about this product!
IMPORTANT SHIPPING & DELIVERY INFORMATION
Carboline Plasite 7159 HAR is only available with the shipping and delivery timescales listed below - please do not contact our Customer Support Team with enquiries about alternative or earlier shipping and delivery times.
Saturdays and Sundays, as well as Bank Holidays, are not classed as working days.
Orders placed after the cut-off for this product will not be processed for earliest dispatch until 9am the next working day.
All delivery costs below are excluding VAT

Carboline Thinner 2
Carboline Thinner 2 is a thinner for use in industrial coatings.
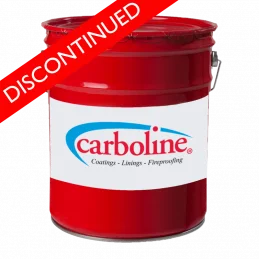
Carboline Thinner 19
We no longer stock this product; please contact our technical team on 0113 2455450 (option 2) or send a message to [email protected] where we will be happy to find an alternative product.

Surface Preparation Kits for Steel
These surface preparation kits for steel have been created to help provide customers with an easily accessible bundle of tools to aid in the preparation of steel surfaces in accordance with ISO 8501-1 (St2/3) and SSPC (SP 2/3). Please click here for important information about these kits. Kit Contents: SET 1 (Hand Tools)1 x Rust-Oleum...