- There are no more items in your cart
- Shipping Calculated at checkout
- Sub-Total (inc. VAT) £0.00
Need Help?
Shop Primers
Buy epoxy and alkyd shop primers at Rawlins Paints. Prepare steel, zinc and aluminium substrates properly with the correct shop primer, from renowned shop primer brands including Hempel, International, Jotun, PPG and Tikkurila. Choose attributes via the sidebar to find the right product for your project requirements, with options such as weldable coatings, for immersion, pack sizes (single or two-pack), high build products and those containing zinc phosphate.

Axalta Speedspray QDH Primer
Use Axalta Speedspray QDH Primer for in-shop spray application to steelwork. It has excellent drying and enamel hold-out, which makes it an ideal base for top coating with Hi-Dur AD100 Finish, with good adhesion and corrosion resistance.Modified-alkyd zinc phosphate primer High build Use as a primer where fast drying properties are...

International Interprime 306
International Interprime 306 is a single component, fast drying, high build alkyd primer used as a shop applied post-fabrication primer specifically designed for a blast, fabricate and prime steel production route, and where fast drying and rapid handling properties are required.

Jotun Muki EPS
A fast drying, shop primer designed for high welding and cutting speed, giving reduced weld porosity and back burning or as a temporary primer in a new construction phases or as a primer in a complete coating system.

Hempel Shopprimer E 15275
Hempel Shopprimer E 15275 is a two-component epoxy polyamide shopprimer, pigmented with zinc phosphate rust-inhibiting pigments. It is designed for automatic spray application.For professional use only Shopprimer for protection of blast cleaned steel plate and other structural steel during the storage and building period Complies with...

Hempel Shopprimer E 15280
Hempel's Shopprimer E 15280 is a two-component epoxy primer, pigmented with zinc phosphate rust-inhibiting pigments. It is designed for automatic spray application as well as manual application.For professional use only Shopprimer for protection of blast cleaned steel plate and other structural steel during the storage and building...
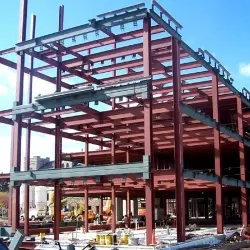
International Interplate 398
International Interplate 398 is a two component, fast drying modified epoxy phosphate prefabrication primer for manual or automatic spray application. It is intended to pre-prime steel prior to the fabrication process and can can be overcoated with a large range of coating systems.
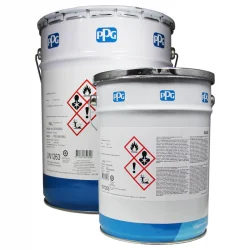
PPG SigmaWeld 120
PPG SigmaWeld 120 is a two-component, polyamide-cured epoxy prefabrication primer that is suitable for automatic application on shot blasted steel plates.Good cutting and welding properties, including MMA and gravity welding Provides corrosion protection up to 6 months Fast-drying properties Can be used as a first coat in various paint...
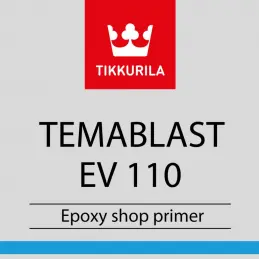
Tikkurila Temablast EV 110
Tikkurila Temablast EV 110 is a two-component, iron oxide pigmented epoxy shop primer that protects blast cleaned steel during storage, fabrication and construction.Does not cause any harm during welding, cutting and burning or other treating of the steel The product is found to comply with:DNV GL class programme DNVGL-CP-0109 – Type...
Need Help?
Need Help?
Shop primers are specialised coatings designed for the protection of metal surfaces, particularly structural steel, during the fabrication and assembly processes. These primers are essential for industries that handle large-scale metal components, where corrosion protection is critical even before the final protective coating is applied. Commonly used in construction, shipbuilding, and heavy manufacturing, shop primers offer an effective solution to shield steel from environmental damage such as rust and oxidation, which can occur as the steel awaits further processing or coating.
The role of shop primers for structural steel is especially vital in protecting metal surfaces during stages like transportation, storage, and assembly. The steel is often exposed to the elements before the topcoat is applied, and the shop primer acts as the first line of defence, safeguarding the material from corrosive agents such as moisture, salt, and air. The effectiveness of a shop primer lies in its ability to form a protective layer without hindering subsequent fabrication processes such as welding and cutting.
Industries reliant on metal structures and components, such as oil and gas, shipbuilding, and construction, benefit greatly from using shop primers. Not only do they prolong the life of steel components, but they also ensure that fabrication and assembly can continue smoothly, without the need for repeated surface preparation. By acting as a temporary corrosion shield, shop primers save time, reduce costs, and improve the overall quality of metal structures.
Key Features to Consider When Choosing Shop Primers
When selecting a shop primer for structural steel, it's important to evaluate a range of features to ensure that the chosen product meets the requirements of the specific application. Here are some of the most critical features to consider:
- Corrosion Resistance: One of the primary reasons to use a shop primer is its ability to protect metal surfaces from corrosion during fabrication. High-quality primers provide a robust barrier that prevents moisture, oxygen, and other corrosive agents from interacting with the steel surface. For example, in shipbuilding, where components are often exposed to seawater, a highly corrosion-resistant shop primer is essential to prevent rust before final coatings are applied.
- Weldability: Shop primers must allow for clean and efficient welding without interfering with the welding process. Primers designed for structural steel are formulated to burn away during welding, ensuring a strong bond between welded joints. For example, in steel bridge construction, where welded connections are vital for structural integrity, a shop primer that doesn’t hinder the welding process is critical.
- Adhesion: A good shop primer will adhere strongly to steel surfaces, forming a durable bond that provides an excellent base for topcoats. Poor adhesion can lead to issues such as peeling and flaking, reducing the effectiveness of both the primer and subsequent coatings. In large infrastructure projects, such as the construction of power plants, a primer with exceptional adhesion ensures that both the primer and final coating stay intact throughout the life of the structure.
- Application Speed and Coverage: In large-scale industrial environments, the speed and ease with which a primer can be applied are critical. Fast-drying primers allow for quicker turnaround times, reducing delays in the fabrication process. For example, in manufacturing sectors like automotive production, where time is of the essence, a shop primer that dries quickly can significantly streamline operations without sacrificing quality.
- Compatibility with Top Coats: Shop primers must be compatible with a range of topcoats, including epoxy, polyurethane, and alkyd-based systems. This compatibility ensures that the final protective layer can be applied without issues, leading to a seamless and durable finish. For instance, in offshore platforms exposed to both saltwater and chemicals, the primer must work harmoniously with high-performance epoxy topcoats to provide long-lasting corrosion resistance.
- Durability During Handling: During the transportation and assembly stages, steel components are often subjected to rough handling. A robust shop primer should withstand abrasion, chipping, and scratching, which could otherwise expose the metal to corrosive elements. For instance, in heavy equipment manufacturing, steel parts that are transported across large distances need to maintain their primer protection, ensuring they arrive in prime condition for final assembly and coating.
- Environmental Compliance: Modern industrial processes demand adherence to environmental regulations. Many shop primers are formulated with reduced volatile organic compounds (VOCs) to minimise harmful emissions during application. Low-VOC primers are particularly useful in industries such as shipbuilding, where large quantities of paint are used, and environmental impact must be kept to a minimum.
- Ease of Use: In high-volume industrial settings, ease of application is paramount. Shop primers that can be sprayed, brushed, or rolled onto metal surfaces without the need for specialised equipment save both time and labour costs. For example, in prefabricated building component production, a versatile shop primer can be quickly applied across various steel components, allowing the process to move efficiently from priming to assembly.
- Heat Resistance: In industries where steel is exposed to high temperatures during fabrication, such as welding and cutting, the shop primer must be able to withstand these conditions without degrading. Heat-resistant shop primers ensure that the protective layer remains intact, even in the most demanding environments. This is particularly crucial in industries like shipbuilding, where steel components are exposed to extreme heat during the welding process.
- Chemical Resistance: For industries like petrochemicals, where steel structures may be exposed to harsh chemicals, the shop primer must offer a degree of resistance to these corrosive agents. By selecting a chemically resistant shop primer, the steel is protected from both atmospheric corrosion and chemical degradation.
Benefits of Shop Primers for Metal Surfaces
- Prevents Corrosion: Shop primers are designed to form a protective layer on metal surfaces, shielding them from moisture, air, and other corrosive elements. This is particularly valuable in industries such as oil and gas, where steel components are often exposed to corrosive environments during transport and installation. By using a high-quality shop primer, steel parts can be protected from rust and corrosion before the final coatings are applied, ensuring their longevity.
- Enhances Adhesion: A shop primer provides a smooth surface for subsequent coatings, enhancing the adhesion of topcoats. This ensures that the final protective layer adheres strongly to the metal, resulting in a more durable and long-lasting finish. In large infrastructure projects, such as steel bridges, the adhesion provided by a shop primer helps ensure that topcoats don’t peel or flake, extending the lifespan of the protective system.
- Facilitates Fabrication Processes: Shop primers are formulated to be compatible with welding, cutting, and other fabrication processes. This makes them ideal for use in industries where steel needs to be primed before being worked on. For instance, in the construction of skyscrapers, steel components are often primed with a shop primer before being welded or bolted together, allowing for smoother construction processes.
- Cost-Effective Corrosion Protection: Shop primers offer a cost-effective solution for protecting steel surfaces from corrosion before the final coating is applied. By providing an initial layer of protection, these primers help reduce the need for extensive surface preparation later on. In the shipbuilding industry, for example, applying a shop primer early in the construction process helps protect steel hulls from rust, reducing the amount of surface preparation required before final painting.
- Minimises Damage During Transport and Storage: Steel components are often transported and stored before they are assembled and coated. Shop primers provide a protective layer that minimises the risk of damage caused by moisture, salt air, and rough handling. For example, in offshore oil platforms, steel components may be transported over long distances and stored for extended periods before assembly. The application of a shop primer ensures that these components remain protected from the elements during this time.
- Reduces Maintenance Costs: By protecting steel surfaces from corrosion and damage during the fabrication process, shop primers help reduce long-term maintenance costs. Steel structures that are properly primed are less likely to require extensive repair or repainting later on. In the construction of large industrial plants, for instance, the use of a shop primer can significantly reduce the need for costly surface preparation and repairs after installation.
- Improves Safety: Corrosion can weaken steel structures, making them more susceptible to failure. By using a shop primer to protect steel components from rust and corrosion, industries can ensure that their structures remain safe and reliable. For example, in the construction of oil refineries, where steel structures are exposed to harsh chemicals and environmental conditions, shop primers provide an essential layer of protection that helps prevent corrosion-related failures.
- Versatility Across Multiple Industries: Shop primers are used across a wide range of industries, from construction and manufacturing to shipbuilding and oil and gas. Their versatility makes them an invaluable tool for protecting steel in virtually any application. For example, in the automotive industry, shop primers are used to protect steel parts from corrosion during the manufacturing process, ensuring that vehicles are built to last.
- Environmentally Friendly Options: Many shop primers are formulated with low levels of VOCs, making them a more environmentally friendly option. These primers help reduce air pollution and are safer for workers to apply. In industries such as shipbuilding, where large quantities of paint are used, the use of low-VOC shop primers can help reduce the environmental impact of the painting process.
- Meets Industry Standards: High-quality shop primers are formulated to meet the specific standards and requirements of various industries. For example, in the shipbuilding industry, shop primers must meet strict corrosion resistance standards to ensure the long-term durability of steel hulls and other components. By choosing a shop primer that meets industry standards, companies can be confident that their steel structures will perform reliably in demanding environments.
Common Uses of Shop Primers
Shop primers are widely utilised across various industries where protecting metal surfaces, particularly structural steel, is paramount. These primers play an essential role in enhancing the durability and integrity of steel during fabrication, storage, transportation, and installation. Below are more detailed descriptions of the common uses of shop primers, with specific examples illustrating their importance in various industries.
Structural Steel Protection
Structural steel forms the backbone of many industrial and commercial buildings, and shop primers are a crucial first step in protecting these vital components. The primer acts as a temporary protective layer during the steel’s fabrication and assembly phases. For example, in the construction of high-rise office buildings or industrial warehouses, the steel beams, columns, and girders that support these structures need to be protected from corrosion before the building’s external cladding and insulation are applied. Without a shop primer, these critical elements could rust during construction, compromising the long-term stability of the building.
Another important application is in sports arenas or stadiums, where large exposed steel structures are part of the design. These structures are fabricated off-site, transported, and then assembled, with a significant amount of time passing before the final coatings are applied. Shop primers ensure that the steel remains protected from moisture, oxygen, and contaminants that could lead to corrosion during this period.
Shipbuilding
The shipbuilding industry, one of the most challenging environments for metal protection, depends heavily on shop primers to protect steel from the harsh marine environment. Ships, whether they are cargo vessels, passenger ships, or naval vessels, are exposed to highly corrosive saltwater, which accelerates the rusting process. Shop primers are applied to steel hulls, decks, and other components during assembly to protect them before the final topcoat of marine-grade paint is applied.
For example, during the construction of an oil tanker, which can take several months to complete, the steel hull sections are built and assembled in outdoor shipyards, fully exposed to the elements. By applying a shop primer immediately after the steel is fabricated, shipbuilders ensure that the steel remains rust-free throughout the construction process. Furthermore, these primers are designed to withstand the rigours of the shipbuilding process, including welding, cutting, and fitting, ensuring that the structural integrity of the ship is maintained.
Another significant application is in the construction of naval vessels, which require an exceptionally high level of corrosion protection due to their demanding operational environments. The steel used in these ships is often primed with highly advanced shop primers that are designed to offer resistance to both saltwater and chemical agents, ensuring that the ship’s structural integrity is preserved throughout its operational life.
Oil and Gas Industry
The oil and gas industry involves extensive use of steel in harsh environments, such as offshore platforms, pipelines, and refineries. Shop primers are integral to protecting these steel structures from the aggressive conditions they encounter. Offshore platforms, for example, are exposed to constant saltwater spray, high humidity, and sometimes chemical exposure from the oil extraction process. The steel used in constructing these platforms must be primed with a highly durable shop primer that can withstand these conditions and prevent corrosion during both fabrication and installation.
An example can be seen in the construction of offshore oil rigs, where steel is often prefabricated on land and then transported by sea to the installation site. During transport, these steel sections are exposed to seawater, and without a shop primer, corrosion could begin even before the rig is assembled. The primer ensures that the steel remains protected until the final coatings, designed for extreme environments, are applied after assembly.
Similarly, pipelines that transport oil and gas across vast distances, both onshore and offshore, benefit from shop primers. These steel pipes are manufactured and coated with a shop primer to protect them from rusting during storage, transport, and installation. In coastal or arid regions, where the environment is particularly harsh, the use of a shop primer is critical to ensure the longevity and performance of the pipeline system.
Bridges and Infrastructure
Steel is a fundamental material in the construction of bridges and other infrastructure projects, where it must be protected from the elements to ensure long-term durability. Shop primers are applied to steel bridge components, such as girders, trusses, and cables, before they are transported to the construction site. These primers protect the steel from corrosion during the time between fabrication and the application of final protective coatings.
For example, in the construction of suspension bridges, the steel cables and towers are fabricated off-site and often stored outdoors before being transported to the construction site. Without a protective shop primer, these steel components would quickly begin to corrode, particularly in coastal areas where bridges are often built. By applying a durable shop primer, contractors can ensure that the steel remains in optimal condition until the final corrosion-resistant coatings are applied.
Infrastructure projects, such as railways and airports, also use shop primers extensively. For instance, steel railway tracks and structural components for railway stations are primed with a protective coating during manufacturing to ensure that they are shielded from rust and wear before final assembly. Similarly, in airport construction, steel components for terminals, hangars, and runways are primed to protect them from corrosion due to exposure to fuel, chemicals, and varying weather conditions.
Heavy Manufacturing
In heavy manufacturing industries, such as automotive and machinery production, steel parts undergo extensive fabrication processes. Shop primers are applied to these steel components to protect them from corrosion and damage during the manufacturing process. For example, in automotive production, steel body panels are often primed before they are welded and assembled into the final vehicle. The shop primer provides a protective layer that ensures the steel remains rust-free until the final paint job is completed.
Another example is the production of heavy machinery, such as cranes, bulldozers, and agricultural equipment. These machines often have large steel components that are fabricated, transported, and stored before final assembly. A shop primer helps protect these parts from rust and damage, ensuring that the finished product is of the highest quality. In the case of agricultural machinery, which operates in environments with high levels of moisture, dirt, and chemicals, a robust shop primer is essential to extend the lifespan of the equipment.
Market Sectors and Industries Using Shop Primers
Shop primers are indispensable across a range of industries, each with its unique challenges and requirements. Below is an expanded look at the key sectors that rely on shop primers for structural steel and other metal components, with detailed examples of how these primers are used in each sector.
Construction
The construction industry is one of the largest users of shop primers, particularly for projects involving structural steel. Buildings, bridges, and industrial facilities all require steel components that are protected from corrosion during the fabrication, transportation, and assembly phases. Shop primers ensure that these steel elements remain rust-free during construction, reducing the need for costly rework or surface preparation later on.
A notable example in the construction sector is the use of shop primers in the erection of skyscrapers. Steel beams, columns, and girders are fabricated off-site, primed with a shop primer, and then transported to the building site. The primer protects the steel from corrosion during storage and transportation, ensuring that the structure remains intact and rust-free until the final protective coatings are applied once the building is complete.
Another important application is in the construction of power plants and industrial facilities, where steel is used extensively. In these projects, shop primers provide an essential layer of protection for steel components that are exposed to both the elements and potentially corrosive industrial environments. By using shop primers, contractors can ensure that these critical structures maintain their integrity and durability over time.
Shipbuilding and Marine
The marine industry is particularly demanding when it comes to protecting steel from corrosion. Shop primers are used extensively in shipbuilding, where steel hulls, decks, and other components are exposed to saltwater, humidity, and rough handling during the assembly process. The use of shop primers ensures that the steel remains protected from corrosion throughout the construction process, preventing costly repairs and rework.
An example of this can be seen in the construction of naval vessels, where steel components are primed to resist corrosion from both saltwater and chemical exposure. Shop primers specifically designed for marine environments offer enhanced protection against the harsh conditions these ships will encounter during their operational life.
Offshore oil and gas platforms also fall under the marine sector. The steel structures of these platforms are exposed to saltwater, wind, and harsh chemicals, making them highly susceptible to corrosion. Shop primers play a crucial role in ensuring that these platforms maintain their structural integrity during transport, installation, and operation in such aggressive environments.
Oil and Gas
In the oil and gas industry, steel components are subject to some of the harshest environments, both offshore and onshore. Shop primers are essential for protecting steel used in pipelines, refineries, and offshore platforms from corrosion caused by saltwater, chemicals, and extreme temperatures. The use of these primers extends the lifespan of critical infrastructure, reduces maintenance costs, and improves the safety and reliability of operations.
Offshore drilling platforms are one of the most prominent examples of how shop primers are used in the oil and gas industry. These platforms are constructed from steel that must withstand not only the corrosive effects of saltwater but also the constant exposure to oil and gas, which can be highly corrosive. Shop primers provide a protective layer that ensures the steel remains rust-free until the final, heavy-duty coatings are applied to withstand the platform’s operational conditions.
Onshore pipelines, which transport oil and gas across vast distances, are another key application. These pipelines often traverse areas with high moisture levels, such as wetlands or coastal regions, where the risk of corrosion is particularly high. Shop primers are applied to the steel pipes during manufacturing to ensure that they remain protected from corrosion during transport, storage, and installation.
Manufacturing
The manufacturing sector, particularly in the production of vehicles, heavy machinery, and equipment, uses shop primers to protect steel components from corrosion during the fabrication process. In the automotive industry, for example, steel body panels are primed to prevent rust and corrosion before the final paint job is applied. This ensures that the vehicle’s steel components remain durable and corrosion-resistant throughout their lifecycle.
Heavy machinery, such as tractors, excavators, and cranes, is another area where shop primers play a crucial role. These machines are often used in harsh environments, such as construction sites, mines, and farms, where they are exposed to moisture, dirt, and chemicals. By applying a shop primer to the steel components during manufacturing, companies can ensure that these machines maintain their structural integrity and performance over time.
In the aerospace industry, shop primers are used to protect steel components in aircraft manufacturing. Steel parts used in landing gear, structural supports, and other critical components are primed to protect them from corrosion caused by environmental exposure, fuel, and other chemicals during the aircraft’s operational life.
Transportation
The transportation sector also relies on shop primers to protect steel infrastructure, such as railway tracks, bridges, and airport terminals. Steel components used in these projects are often exposed to the elements, including moisture, salt, and chemicals, making them susceptible to corrosion. By applying shop primers during fabrication, companies can ensure that these components remain protected until the final coatings are applied, enhancing the durability and longevity of the infrastructure.
For example, in railway construction, steel tracks, bridges, and support structures are primed to prevent corrosion during installation and operation. The use of shop primers helps ensure that the steel remains rust-free, reducing maintenance costs and improving the safety and reliability of the rail network.
Similarly, in airport construction, steel components for terminals, runways, and hangars are primed with shop primers to protect them from corrosion caused by exposure to fuel, chemicals, and varying weather conditions. This ensures that the airport’s infrastructure remains safe, durable, and operational over the long term.