- There are no more items in your cart
- Shipping Calculated at checkout
-
Sub-Total (inc. VAT)
£0.00
Need Help?
Fire Protection for Concrete
Buy specialist fire protection for concrete surfaces, with 4,400+ colours available in up to 120 minutes fire protection for bare or suitably-painted internal concrete. Choose from top fire protection manufacturers including Thermoguard, Sherwin-Williams, Hensel, and Protecta, with fire certificates available on completion.
If you require more help to find and specify fire protection for your project or contract, our technical team are always on hand to advise. Give us a call on 0113 2455450 (option 2) or send a message to [email protected].
Subcategories
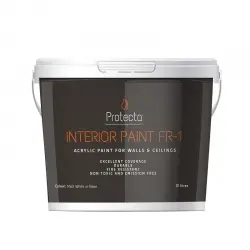
Protecta Interior Paint FR-1
Hardwearing interior decorative acrylic paint in 28 colours for most surfaces, including concrete, bricks, masonry, primed steel, wood, gypsum and most non-porous surfaces. Special properties protect against spread of fire. One-layer system normally requires no primer and no top coat. Easy to use and very easy to clean up. Smooth and...

Thermoguard Wallcoat 60, 90 & 120 Minute System for Concrete
Intumescent paint system in 4,000+ colours for interior fire rated concrete surfaces requiring an additional 30mins fire resistance - not subject to traffic. These packs have been created to help users ensure they are purchasing sufficient product for their project. Each pack contains the correct amount of basecoat (Wallcoat) and topcoat...

Sherwin-Williams Firetex Concrete WB-120
Water-based fire protection coating system for interior concrete structures. Mainly designed for refurbishing/ change of use of building structures like concrete, masonry and brickwork. Firetex Concrete WB-120 prohibits the spalling of concrete structures and significantly delays the heat buildup of steel reinforcements For professional use...

Sherwin-Williams Firetex Concrete WB
Water-based fire protection coating system for interior concrete structures. Mainly designed for refurbishing/ change of use of building structures like concrete, masonry and brickwork. Firetex Concrete WB prohibits the spalling of concrete structures and significantly delays the head buildup of steel reinforcements. For professional use...

Hensel Hensomastik B 3000
Water-based fire protection coating for interior and exterior concrete. Improves fire-resistance time of concrete and reinforced concrete structural parts up to 120 minutes and is used particularly in areas with high emission loading, such as underground and multi-storey car parks. Fulfils the requirements under DIBt (October 2010) and AgBB...

Hensel Hensotherm 820 KS
Thin-film water-based fire protection coating for interior concrete. It improves the fire-resistance time of pre-stressed concrete hollow ceilings up to 120 minutes, reinforced concrete beams and supports up to 150 minutes, and concrete flat slab ceilings and reinforced concrete ribbed slab ceilings up to 240 minutes. Forms a...

Sherwin-Williams Firetex FX5120
We no longer stock this product; please contact our technical team on 0113 2455450 (option 2) or send a message to [email protected] where we will be happy to find an alternative product. A water based TCEP free thin film intumescent coating designed to provide fire resistance for periods of up to 120 minutes on structural steel....
Need Help?
Need Help?
Fire protection is a critical aspect of building safety, designed to safeguard both human life and property in the event of a fire. A comprehensive fire protection strategy typically involves both active and passive measures. Active fire protection includes systems that require activation, such as sprinklers, fire alarms, and smoke control systems. In contrast, passive fire protection focuses on the use of building materials and design elements that inhibit the spread of fire and maintain the structural integrity of a building during a fire.
Fire Protection Strategies
Fire protection strategies are broadly classified into two categories: passive fire protection and active fire protection.
- Passive Fire Protection (PFP): This involves the use of fire-resistant materials and building components that help to contain a fire and prevent it from spreading. These components include fire-resistant walls, floors, ceilings, doors, and glazing, as well as protective coatings and paints. Passive fire protection measures are designed to maintain the integrity of fire compartments and ensure that the fire does not breach these barriers, allowing safe evacuation and reducing the risk of structural collapse.
- Active Fire Protection (AFP): This includes systems and devices that are activated during a fire, such as fire alarms, sprinkler systems, and smoke control systems. These systems require a trigger, either automatically via sensors or manually by individuals, to function and actively combat the fire.
An effective fire protection strategy integrates both passive and active measures, often supported by fire safety management practices and, in some cases, fire safety engineering approaches tailored to specific building needs.
Role of Fire Protection Paints in Fire Safety for Concrete Structures
Concrete is a common material in modern construction due to its inherent fire resistance. However, under prolonged exposure to intense heat, concrete can suffer damage such as spalling, where pieces of concrete break away from the surface, potentially exposing the steel reinforcement and compromising the structural integrity. This is where fire protection paints, particularly intumescent coatings, play a crucial role.
Fire protection paints, also referred to as intumescent coatings, are a form of passive fire protection designed to enhance the fire resistance of materials like concrete. These coatings react to the heat from a fire by swelling and forming an insulating layer of char. This layer significantly slows down the heating process of the underlying concrete, thereby delaying the onset of spalling and preserving the structural integrity for a longer period.
The application of these coatings can be particularly important in ensuring that critical structural elements, such as load-bearing walls and columns, remain stable during a fire, thereby maintaining the overall safety of the building. The effectiveness of fire protection paints is dependent on proper application and adherence to the specific guidelines provided by manufacturers, as well as compliance with relevant fire safety standards.
In summary, fire protection paints are an integral component of passive fire protection strategies, particularly for concrete structures. They work by enhancing the inherent fire resistance of concrete, contributing to the overall fire safety of buildings and providing additional time for evacuation and fire-fighting efforts.
Intumescent Fire Protection Paints for Concrete
Mechanism on Concrete
Intumescent paints are formulated to react with heat during a fire, creating a thermally insulating barrier on the surface of the concrete. The paint contains chemical agents that, when exposed to high temperatures, decompose and release gases. These gases cause the paint to expand and form a thick, foam-like char layer. This layer acts as an insulating barrier, significantly reducing the heat transfer to the underlying concrete. The process slows the rise in temperature of the concrete, protecting it from the damaging effects of intense heat and reducing the risk of spalling, where pieces of concrete break off due to the internal pressure caused by steam formation.
Concrete itself is relatively resistant to fire; however, prolonged exposure to high temperatures can weaken it, especially in reinforced concrete structures where the steel reinforcement can lose its strength or become exposed due to spalling. Intumescent paints help mitigate these risks by maintaining the concrete's integrity for a longer period, thereby providing additional time for evacuation and firefighting efforts.
Applications
Intumescent paints are typically applied in environments where structural integrity is critical during a fire. They are used in high-risk areas like tunnels, where concrete surfaces are exposed to potential fire hazards. They are also used in industrial settings, such as chemical plants and refineries, where fires can reach extremely high temperatures. The application is usually specified where enhanced fire protection is required for structural elements, particularly in buildings that must comply with stringent fire safety regulations. In some cases, intumescent paints are also used in commercial and residential buildings to protect load-bearing walls and structural columns.
Advantages
- Provides excellent insulation, protecting the structural integrity of concrete.
- Delays the temperature rise, reducing the risk of spalling and structural failure.
- Can be applied to both new constructions and existing structures for retrofitting fire protection.
Challenges
- Requires precise application conditions, including correct thickness and environmental controls during curing.
- Can be sensitive to moisture, requiring careful selection and application in humid environments.
Standards and Certification in Fire Protection Paints for Concrete
The fire protection paints applied to concrete must comply with rigorous testing standards and certification processes to ensure they provide the required fire resistance and reaction to fire performance. The use of third-party certification, in particular, is critical for ensuring that these materials are reliable and meet all necessary safety requirements.
Relevant UK and European Standards
When it comes to fire protection paints, particularly those applied to concrete, the standards and testing procedures are crucial for ensuring the effectiveness and compliance of these materials. In the UK and Europe, several key standards guide the fire performance assessment of these materials:
- BS 476 Series: Historically, the British Standard BS 476 series has been used to assess fire resistance and reaction to fire of construction materials, including paints and coatings. This series includes:
- BS 476 Part 6: Focuses on the fire propagation characteristics of materials.
- BS 476 Part 7: Evaluates the surface spread of flame. These tests collectively contribute to the classification of materials under the UK’s Class 0 rating, which is often required for wall and ceiling linings.
- EN 13501-1: This European standard has been adopted across EU member states, including the UK. It classifies the reaction to fire performance of building products and systems into Euroclasses (A1 to F), where A1 represents non-combustible materials, and F indicates materials with no determined performance. This standard incorporates several testing methods, such as:
- EN ISO 1182: Non-combustibility test.
- EN 13823: Single Burning Item (SBI) test for measuring flame spread, heat release, and smoke production.
- EN ISO 1716: Determination of the heat of combustion.
Testing Requirements
Before any fire protection paint or coating can be applied to concrete in a building, it must undergo rigorous testing to assess its fire resistance and reaction to fire:
- Fire Resistance Testing: This involves exposing the material to controlled fire conditions to evaluate how well it can maintain its integrity, insulation, and load-bearing capacity for a specified period, typically ranging from 30 minutes to several hours. The performance under these tests is critical in determining the material's suitability for use in specific fire safety applications.
- Reaction to Fire Testing: These tests assess how a material reacts when exposed to fire, focusing on its ignitability, flame spread, heat release, and the production of smoke and toxic gases. The results from these tests are used to classify the material according to standards such as BS 476 and EN 13501-1.
Certification Processes
Certification plays a vital role in ensuring that fire protection paints meet the necessary safety standards and are suitable for use in construction:
- Third-Party Certification: This is considered the most reliable form of certification. An independent certification body, accredited by the UK Accreditation Service (UKAS), assesses the product’s compliance with relevant standards. This process involves reviewing test data, conducting factory production control audits, and ongoing product verification through audit tests and inspections. Third-party certification is often required at the construction tender stage and is endorsed by industry bodies like the Association for Specialist Fire Protection (ASFP).
- Assessments and Expert Judgments: In cases where full testing may not be feasible, assessments by accredited fire test laboratories or qualified fire consultants can provide supporting evidence for a product’s fire performance. However, these assessments do not include the quality control aspects of third-party certification and are generally considered a step below full certification.
- Fire Test Reports: While not as robust as third-party certification, fire test reports provide detailed results from standard fire tests. These reports are essential for demonstrating compliance with fire safety regulations but do not include ongoing quality assurance measures.
Application Methods for Fire Protection Paint on Concrete
Surface Preparation
Proper surface preparation is fundamental to ensuring that fire protection paint adheres correctly to concrete surfaces, providing the necessary protection. The preparation process typically involves several critical steps, but users must always consult the technical data sheet or the manufacturer to ensure their surface preparation guidelines are met:
- Cleaning: The concrete surface must be thoroughly cleaned to remove all contaminants, including dust, dirt, grease, oil, old coatings, or any other substances that could hinder the adhesion of the fire protection paint. Methods such as pressure washing, sandblasting, or grinding may be employed depending on the extent of contamination.
- Drying: The surface must be dry before applying any paint. Moisture in the concrete can prevent proper adhesion and curing of the paint, leading to reduced effectiveness of the fire protection. It may also cause the paint to blister or peel off over time. The drying process should be closely monitored, especially in humid environments.
- Surface Profiling: Creating a suitable surface profile is often necessary to ensure that the fire protection paint adheres properly. This can involve light abrasive blasting or grinding to roughen the surface, providing a better mechanical bond for the primer and subsequent coats.
- Priming: Depending on the type of fire protection paint being used, a primer may be required to enhance adhesion and provide a uniform surface for the paint. The type of primer and the method of application should follow the manufacturer’s recommendations.
- Inspection: Before applying the fire protection paint, a thorough inspection should be conducted to ensure that the surface is adequately prepared. Any defects such as cracks, voids, or areas of weak adhesion should be addressed before proceeding.
On-Site vs. Factory Application
When deciding between on-site and factory application of fire protection paint on concrete, several factors must be considered:
On-Site Application:
- Advantages:
- Adaptability to Site Conditions: On-site application allows the paint to be applied after all construction or renovation work is completed, reducing the risk of damage during transport or installation. This method is particularly advantageous for retrofitting older buildings or in complex structures where access is limited.
- Reduced Transport Costs: Since the application is done directly at the construction site, there is no need to transport large, pre-coated components, which can be costly and logistically challenging.
- Challenges:
- Environmental Control: Maintaining the ideal environmental conditions (temperature, humidity, cleanliness) is more difficult on-site, which can affect the quality of the application. Variations in these conditions can lead to inconsistent drying and curing, potentially compromising the fire resistance of the coating.
- Time-Consuming: On-site application may take longer, especially in adverse weather conditions, which can delay the project.
Factory Application:
- Advantages:
- Controlled Environment: Factory application allows the fire protection paint to be applied under optimal conditions, ensuring consistent quality and performance. The environment can be tightly controlled for temperature, humidity, and cleanliness, leading to a more reliable application.
- Efficiency: Once the components are coated and cured in the factory, they can be quickly installed on-site, reducing overall project timelines and on-site labour costs.
- Challenges:
- Risk of Damage During Transport: Pre-coated components can be susceptible to damage during transportation to the site, which might necessitate touch-ups or even reapplication of the fire protection paint.
- Initial Costs: The setup for factory application can be more expensive initially, due to the need for specialized facilities and equipment. Additionally, logistics and transportation add to the overall cost.
- Considerations for Large Projects: For large-scale construction projects or where consistency is critical, factory application is often preferred despite the higher initial cost because of the control and quality assurance it provides.
Environmental Considerations
Environmental conditions play a critical role in the application and performance of fire protection paint. Several factors need to be considered:
- Temperature: The ambient and surface temperature during application is crucial. Most fire protection paints have an optimal temperature range for application, typically between 10°C and 35°C. Temperatures outside this range can lead to problems such as improper curing or drying. For example, high temperatures can cause the paint to dry too quickly, leading to cracks and insufficient coverage, while low temperatures may prevent the paint from curing properly.
- Humidity: High humidity levels can slow down the drying process and affect the adhesion of the paint to the concrete surface. In very humid conditions, moisture can become trapped under the paint layer, leading to blistering or peeling over time. Conversely, very low humidity can cause the paint to dry too fast, leading to an incomplete cure. It’s essential to monitor humidity levels during application and to ensure they are within the recommended range specified by the paint manufacturer.
- Ventilation: Adequate ventilation is necessary, especially for solvent-based paints, to allow fumes to dissipate and to ensure that the curing process is not impeded. Poor ventilation can lead to slow drying times and potential safety hazards due to the accumulation of volatile organic compounds (VOCs).
- Dust and Airborne Particles: In environments where dust or other airborne particles are present, there is a risk of these contaminants settling on the wet paint, which can compromise the finish and effectiveness of the fire protection. Steps should be taken to minimize dust during application, including possibly enclosing the work area or applying the paint during off-peak times when dust levels are lower.
- Curing Time: Environmental conditions will also affect the curing time of the fire protection paint. Adequate curing is essential for the paint to develop its full fire-resistant properties. Any exposure to moisture, extreme temperatures, or mechanical stress before the paint has fully cured can reduce its effectiveness.
By taking into account these detailed aspects of surface preparation, application methods, and environmental conditions, it is possible to ensure that fire protection paint on concrete surfaces performs as intended, providing critical fire resistance to the structure.
Upgrading Existing Concrete Structures with Fire Protection Paints
Assessment of Existing Structures
When upgrading older concrete structures with fire protection paints, a thorough assessment of the existing concrete is crucial. This assessment involves several key steps:
- Structural Integrity and Condition:
- Surface Preparation: The surface condition of the concrete must be thoroughly examined. Any dirt, grease, old paint, or other contaminants should be removed to ensure proper adhesion of the fire protection paint. This step is vital as older materials may not provide a suitable surface for modern fire protection coatings, potentially leading to adhesion problems.
- Environmental Considerations:
- Moisture Content: The moisture level within the concrete should be checked and maintained within the manufacturer’s specified range. High moisture content can interfere with the curing and performance of fire protection paints, particularly those sensitive to humidity.
- Exposure Conditions: Assess the environmental conditions where the concrete is located, including exposure to varying temperatures and humidity. This helps in selecting a fire protection paint that is suitable for the specific environmental conditions the structure will face .
Application for Upgrades
Applying fire protection paints to upgrade the fire resistance of existing concrete structures requires adherence to best practices to ensure efficacy and compliance with fire safety standards:
- Surface Preparation:
- Cleaning and Priming: All surfaces must be clean, dry, and free from contaminants before applying fire protection paint. In cases where old coatings exist, their removal or proper treatment is necessary to avoid adhesion issues. A primer may be required to ensure that the fire protection paint adheres well to the concrete .
- Testing Adhesion: Before full application, a small test area should be treated to confirm that the paint adheres properly and cures as expected. This step is especially important when dealing with older or previously treated surfaces.
- Application Techniques:
- Thickness and Coating Layers: The application should follow the manufacturer's guidelines regarding the number of coats and the thickness of each layer. Fire protection paints, especially intumescent types, require specific thicknesses to be effective. Multiple coats may be necessary, with each layer allowed to dry before the next is applied.
- Use of Appropriate Tools: Fire protection paints can be applied using brushes, rollers, or spray equipment. The method used will depend on the paint type, the surface area, and the complexity of the structure. Airless spray application is common for large areas, but care must be taken to achieve an even coat.
- Environmental Controls:
- Curing Conditions: The environment during and after application must be controlled to ensure the paint cures correctly. This includes maintaining appropriate temperature and humidity levels as specified by the paint manufacturer. Failure to do so may result in reduced fire resistance performance .
- Certification and Testing:
- Post-Application Testing: After the fire protection paint has been applied and cured, the structure should be tested to verify that the desired level of fire resistance has been achieved. This may involve fire resistance testing of the coated structure or certification based on the paint's proven performance under similar conditions.
- Documentation: Ensure that all application processes are documented and that the fire protection system is certified for the specific conditions of the structure. This includes adhering to any limitations specified in the product’s test reports and assessments.
By following these detailed procedures, existing concrete structures can be effectively upgraded to meet modern fire resistance standards, enhancing their safety and prolonging their service life.
Common Challenges and Solutions for Fire Protection Paints on Concrete
Adhesion Issues
Adhesion problems are a common challenge when applying fire protection paints on concrete surfaces. Poor adhesion can result from several factors, including surface contamination and the inherent characteristics of the concrete substrate. Concrete surfaces may contain dust, oil, or moisture, which can hinder the paint's ability to bond effectively. Additionally, older concrete surfaces with unknown previous treatments or coatings can further complicate adhesion.
Solutions:
- Surface Preparation: Proper surface preparation is crucial. Concrete surfaces should be thoroughly cleaned to remove dirt, dust, grease, oils, and any previous coatings that may interfere with adhesion. Surface preparation might include mechanical abrasion, washing, or the application of primers specifically designed for use on concrete substrates .
- Use of Primers: Primers are often necessary to improve the bonding between the concrete and the fire protection paint. Selecting a primer compatible with both the concrete substrate and the fire protection paint can significantly enhance adhesion. Always check with the manufacturer for their approved primer, if relevant.
- Trial Application: Conducting a trial application on a small area can help ensure that the paint adheres properly before applying it to the entire surface. This step is particularly important when dealing with surfaces that have been previously coated or treated .
Environmental Exposure
Concrete structures often endure harsh environmental conditions, such as extreme temperatures, humidity, and exposure to chemicals or pollutants. These conditions can affect the performance and durability of fire protection paints.
Solutions:
- Selecting the Right Paint: Fire protection paints must be chosen based on their ability to withstand the specific environmental conditions they will be exposed to. For example, some intumescent coatings are moisture-sensitive and may not perform well in high-humidity environments. It is essential to select a paint system that is appropriate for the environmental exposure it will face, and one that has been tested for the project detail.
- Application Conditions: The application of fire protection paints should be carried out under controlled conditions. Ambient temperature, substrate temperature, and humidity levels must be within the manufacturer’s specified range to ensure optimal performance. Applying the paint outside of these conditions can result in reduced effectiveness and durability .
- Ongoing Maintenance: Regular inspections and maintenance are necessary to ensure that the fire protection paint continues to perform as expected. Environmental factors can degrade the paint over time, so it’s important to monitor its condition and reapply as needed to maintain fire protection integrity. Always refer to the manufacturer’s maintenance schedule to ensure the coatings are kept in optimal condition.
Regulatory Compliance
Ensuring that fire protection paints meet local and national regulations is critical for both safety and legal compliance. Different jurisdictions may have specific standards that dictate the required fire resistance levels and testing procedures for materials used in building construction.
Solutions:
- Compliance with Standards: Fire protection paints must be tested and certified according to relevant standards, such as BS 476 in the UK or the EN 13381 series in Europe. These standards ensure that the paints meet the necessary fire resistance requirements for the specific application .
- Documentation and Certification: Proper documentation, including fire test reports, certification from accredited bodies, and compliance with applicable standards, must be maintained. This documentation is often required during building inspections and for legal compliance purposes .
- Third-Party Certification: Obtaining third-party certification can provide additional assurance that the fire protection system meets all necessary regulatory requirements. This involves an independent assessment by a certification body, which evaluates the performance of the paint system under various conditions .
By addressing these challenges with appropriate solutions, fire protection paints can be effectively applied to concrete surfaces, ensuring both safety and compliance with relevant regulations.
FAQs
Can fire protection paints be used on previously coated concrete surfaces?
Yes, fire protection paints can be applied to previously coated surfaces, but several factors need to be considered to ensure proper adhesion and performance:
- Surface Preparation: The existing coating must be thoroughly cleaned to remove any contaminants that could interfere with adhesion. In some cases, the old coating may need to be partially or fully removed, especially if it is incompatible with the new fire protection paint.
- Compatibility Testing: It is recommended to conduct a small-scale test application to check the compatibility of the new fire protection paint with the existing surface. This test will help identify any issues with adhesion, drying, or curing before the full application is undertaken.
- Manufacturer’s Guidelines: Always follow the manufacturer’s instructions regarding surface preparation and the application of fire protection paints over existing coatings. Failure to do so can result in poor performance or reduced fire resistance.
How often should fire protection paints on concrete be inspected or maintained?
Regular maintenance and inspection are vital to ensure the continued effectiveness of fire protection paints. The frequency and scope of these inspections depend on the environment and usage conditions:
- Routine Inspections: It is recommended that inspections be conducted at least annually, or more frequently in harsh environments. During these inspections, look for signs of damage such as cracking, flaking, or discoloration, which can indicate that the paint’s protective qualities have been compromised.
- Touch-Ups and Repairs: Minor damages should be addressed promptly to prevent them from worsening. Touch-ups may involve reapplying the fire protection paint to affected areas, ensuring that the new coating blends seamlessly with the existing paint.
- Documentation: Keep detailed records of all inspections and maintenance activities. This documentation is important for compliance with fire safety regulations and for ensuring that the fire protection system remains effective over time.
7. What are the limitations of using fire protection paints on concrete?
While fire protection paints provide valuable passive fire resistance, there are limitations to their use:
- Structural Reinforcement: Fire protection paints are primarily designed to enhance the surface fire resistance of concrete. They do not provide significant structural reinforcement and should not be relied upon to prevent structural collapse in severe fire scenarios. In cases where structural integrity is a concern, other fire-resistant construction methods may be necessary.
- Environmental Sensitivity: Some fire protection paints, particularly intumescent coatings, are sensitive to environmental conditions such as humidity and temperature during application and curing. Inappropriate conditions can lead to poor performance or even failure of the paint to provide the expected fire resistance.
- Application Challenges: Achieving the correct thickness and uniform application is critical for the effectiveness of fire protection paints. This requires careful preparation and attention to detail during application. Inconsistent application can result in areas with insufficient protection, which could compromise the fire safety of the entire structure.
Can intumescent paint be used on concrete?
While intumescent paint can enhance the fire resistance of concrete structures, its use requires careful consideration of the substrate's properties, proper application techniques, and thorough testing and certification to ensure it meets the necessary fire resistance standards. Adherence to manufacturers' guidelines and regular maintenance are also crucial for ensuring long-term performance.
Fire Resistance and Concrete
Concrete naturally possesses some fire-resistant properties. However, it can suffer from spalling under high temperatures, where pieces of concrete break off, potentially exposing the structural elements beneath to higher temperatures and increasing the risk of structural failure.