- There are no more items in your cart
- Shipping Calculated at checkout
-
Sub-Total (inc. VAT)
£0.00
Need Help?
Intermediates
Intermediate primers for metal play a crucial role in enhancing the durability and protection of metal surfaces across industrial, commercial, and architectural sectors. These primers act as a bonding layer between a base coat and a topcoat, providing superior adhesion, corrosion resistance, and surface protection. Ideal for heavy-duty applications, they ensure a long-lasting finish even in extreme environments. Whether for steel frameworks, machinery, or marine equipment, intermediate primers are an essential part of a multi-coat system designed to offer robust protection and prolong the lifespan of metal structures.

PPG SigmaCover 456
PPG SigmaCover 456, a two-component, high-build, polyamide-cured recoatable epoxy coating available in 2,600+ colours, for steel and concrete structures exposed to atmospheric land or marine conditions, curing at temperatures down to -10°C (14°F). SigmaCover 456 can be recoated with various two-component and conventional coatings, even after...
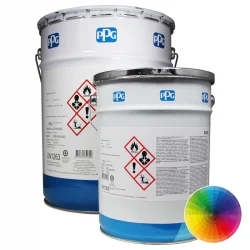
PPG AquaCover 400
PPG AquaCover 400 (also known as Sigma Aquacover 400) is a two-component, polyamine-cured, waterborne epoxy coating for steel structures in atmospheric exposure, touch dry in 90 minutes. Also suitable for concrete floors. Particularly suitable when solvents are not permitted because of health and safety reasons Free from lead- and...
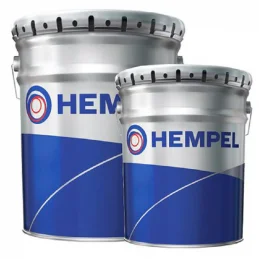
Hempel Hempadur 47140
Hempadur 47140 is a two-component polyamide adducts cured, high build epoxy paint which combines a relatively high volume solids content with a short drying time. VOC compliant. For professional use only Primer for mild to medium atmospheric environments, or intermediate/finishing coat for epoxy systems in medium to severely corrosive...

Sherwin-Williams Macropoxy C123
Sherwin-Williams Macropoxy C123 (formerly known as Epigrip C123) is a high solids, glass flake epoxy coating for the anti-corrosive protection of blast cleaned steel. Macropoxy C123 is especially suitable for steel structures, bridges and infrastructure in aggressive atmospheric conditions. Network Rail Item 7.2.3., Highways Agency Item No....
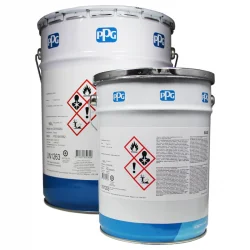
PPG SigmaCover 410
PPG SigmaCover 410, formerley known as AmerCoat 410, a two-component general-purpose epoxy buildcoat in protective coating systems for steel and concrete structures exposed to atmospheric land or marine conditions. The coating has excellent durability and can be recoated with various two-component and conventional coatings, even after long...
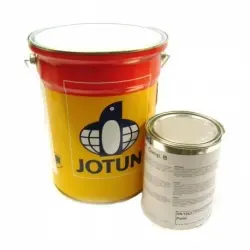
Jotun Penguard Midcoat
We no longer stock this product, but can recommend Jotun Penguard Express as a great alternative. Please note: it is important to check that any alternative product is suitable for your requirements, as our suggestion is given in good faith but without warranty. If you are in any doubt please first contact our technical team on 0113 2455450...

International Intergard 214
International Intergard 214 is a two component epoxy sealer coat pigmented with aluminium flake for the effective penetration and sealing of thermally sprayed aluminium coatings to eliminate porosity. Has specification approval for UK Department of Transport Item No.159.
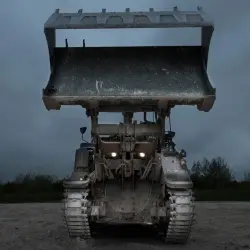
International Intergard 405
International Intergard 405 is a two component epoxy sealer coat, pigmented with micaceous iron oxide. Formulated on proprietary polymer technology, which provides rapid cure and overcoating, even at low temperatures. Provide efficient sealing of zinc silicate primers in order to prevent pinholing of subsequent topcoats Can also be used...

Sherwin-Williams Macropoxy M330
Sherwin-Williams Macropoxy M330 (formerly known as Epigrip M330) is a 2-pack epoxy sealercoat for use over zinc silicate and other types of zinc rich primers. It is also used as a blast primer for use over stainless steel. Please note: This product is made to order subject to a minimum order quantity of 150L and an extended lead time of 14...
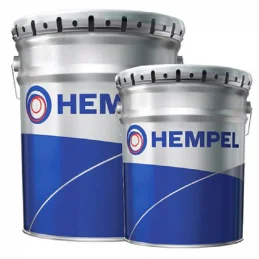
Hempel Hempadur 17940
Hempadur 17940 is a two-component polyamide adduct-cured epoxy paint. It cures to a flexible, well adhering coating. Contains aluminium. Sealer for Hempadur systems on aluminium/zinc metal sprayed substrate in atmospheric exposure Service temperature: - Maximum, dry exposure only: 140°C For professional use only. More Information...
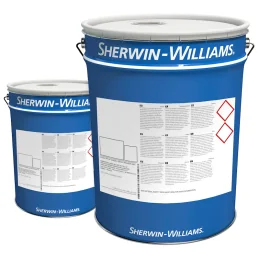
Sherwin-Williams Macropoxy 2706 EG
A 2-pack epoxy primer and intermediate coating pigmented with micaceous iron oxide (MIO). Direct to hot-dip galvanized steel, stainless steel and aluminium Can be used as an intermediate coating for atmospheric corrosion protection on steel Suitable as sealer for thermal-sprayed zinc coatings Can be used as a primer under Firetex,...
Need Help?
Need Help?
What Are Intermediate Primers for Metal?
Intermediate primers for metal are a key part of multi-coat systems designed to protect metal surfaces from corrosion, wear, and harsh environmental conditions. They serve as a bridge between the base coat and topcoat, enhancing adhesion, smoothing surfaces, and increasing the durability of the entire coating system.
These primers are indispensable in industries facing significant exposure to moisture, chemicals, and other corrosive elements. They not only ensure the longevity of metal surfaces but also prevent costly repairs or replacements due to corrosion and degradation. Often known as "tie coats," intermediate primers make sure that each layer of coating bonds properly to the one beneath it. This enhances the overall protection and performance of the coating system.
Why Are Intermediate Primers Important?
Intermediate primers are essential because they offer more than just a bond between coating layers. They play a critical role in improving the resilience of metal coatings, particularly in challenging environments. Corrosion is a major threat to metals exposed to air, water, or chemicals. Intermediate primers create a strong barrier that prevents these elements from reaching the metal, thereby prolonging the life of the structure.
One of the most significant functions of intermediate primers is improving bonding between the base and topcoat. Without this layer, the topcoat may peel, blister, or fail to adhere properly, especially in environments where the metal is exposed to moisture or temperature changes. The corrosion resistance provided by intermediate primers is another important feature. They block the elements that cause rust and oxidation, which is particularly important for metals like steel or aluminium.
These primers also increase surface durability by protecting against mechanical damage, chemical exposure, and daily wear. In addition, many intermediate primers help smooth the surface of the base coat, correcting imperfections that could affect the appearance or performance of the topcoat. Another critical function is their ability to withstand extreme conditions, including intense heat, humidity, and chemical exposure. This makes them a preferred choice for environments such as offshore oil platforms and industrial facilities.
Top Features and Benefits of Intermediate Primers
Versatile Adhesion
Intermediate primers ensure strong adhesion between the base coat and the topcoat, allowing the entire system to act as a unified, durable layer of protection. This prevents the topcoat from chipping or peeling off, which is crucial for long-term protection.
Corrosion Protection
The most vital benefit of intermediate primers is their role in preventing corrosion. When applied correctly, they act as a shield, keeping moisture, air, and contaminants from reaching the metal surface, which greatly reduces the risk of rust.
Extended Coating Lifespan
Intermediate primers help extend the life of the entire coating system. By enhancing adhesion and adding an extra layer of protection, they reduce the likelihood of the topcoat failing prematurely. This translates to fewer maintenance cycles and longer-lasting metal protection.
Compatibility with Multiple Metals
These primers are versatile enough to be applied on various metals, such as steel, aluminium, and galvanised surfaces. Their flexibility means they can be used across many industries, from automotive manufacturing to industrial equipment.
Environmental Resistance
Many intermediate primers are designed to endure the harshest conditions, such as UV exposure, chemical spills, and fluctuating temperatures. This makes them an ideal choice for use in marine and offshore industries, where metal surfaces are constantly exposed to the elements.
Ease of Application
Intermediate primers are simple to apply and can be used with multiple methods, such as spraying, brushing, or rolling. This versatility ensures that they can be applied quickly and evenly, making them suitable for a wide range of projects, from small repairs to large-scale industrial applications.
Fast Drying Times
Some intermediate primers have the advantage of fast drying times, allowing the topcoat to be applied more quickly. This speeds up the overall project timeline, especially in industries where downtime can be costly.
Abrasion and Impact Resistance
In addition to protecting against corrosion, intermediate primers also offer resistance to scratches, impacts, and general wear. This makes them ideal for environments where metal surfaces are subject to constant physical stress, such as machinery in industrial plants.
Common Uses and Market Sectors for Intermediate Primers
Intermediate primers for metal are essential across a wide range of industries that rely on metal surfaces for structural integrity. These industries include construction, marine, automotive, aerospace, and oil and gas. Below is a detailed exploration of how these primers are applied across these sectors.
Structural Steel in Construction
In the construction industry, intermediate primers are critical for protecting steel frameworks, beams, and other structural elements. Steel structures are often exposed to harsh outdoor conditions, including rain, UV radiation, and pollutants. Without the use of primers, these metal surfaces would corrode, compromising the integrity of the building or infrastructure. For example, bridges and skyscrapers commonly use intermediate primers as part of their protective coating systems. This ensures the longevity of the steel components, which are exposed to the elements continuously. The steel beams used in these projects benefit greatly from the enhanced adhesion and corrosion resistance offered by the primer, which protects them from rust and structural degradation.
Marine and Offshore Applications
The marine environment presents one of the most challenging settings for metal protection. Saltwater, wind, and constant exposure to moisture mean that metal surfaces are highly susceptible to rust and corrosion. Intermediate primers are a key component in coating systems for ships, oil rigs, and other marine structures. For instance, offshore oil platforms use intermediate primers to protect their steel structures from the corrosive effects of saltwater. These primers help ensure that the steel remains protected even when exposed to the constant crashing of waves and the abrasive effects of salt. In the shipping industry, intermediate primers are also applied to the hulls of vessels to prevent corrosion, even when exposed to the harsh conditions of the open sea.
Automotive Industry
In the automotive sector, intermediate primers are used to protect car bodies and frames from rust and wear. Vehicles are frequently exposed to moisture, road salt, and other elements that can degrade metal surfaces. The undercarriages of vehicles, in particular, face significant exposure to water and debris from the road. Intermediate primers ensure that these metal surfaces remain protected, preventing rust from forming. They also help improve the durability of paintwork, making sure that it adheres properly to the metal surface underneath. This results in longer-lasting finishes and better protection against the elements. The added corrosion resistance provided by intermediate primers is critical for ensuring the longevity of vehicles, especially those driven in harsh conditions.
Industrial Manufacturing
In manufacturing plants, metal machinery and equipment are exposed to chemicals, high temperatures, and abrasive materials. Intermediate primers are used to protect these metal surfaces from corrosion, wear, and damage. For example, machinery used in chemical processing plants often has metal components that come into direct contact with corrosive substances. Without the protection of intermediate primers, these components would quickly degrade. By applying an intermediate primer, the machinery's lifespan is extended, and the frequency of maintenance is reduced. Similarly, metal conveyor belts used in industrial plants can be coated with intermediate primers to prevent damage caused by the friction and abrasion of materials being processed.
Bridges and Infrastructure
Steel bridges and other infrastructure projects that are constantly exposed to outdoor elements rely heavily on intermediate primers to protect against corrosion. Bridges, in particular, face significant exposure to rain, snow, road salt, and air pollution, all of which can contribute to the rapid degradation of steel surfaces. Applying an intermediate primer to these structures helps ensure their longevity and safety. The primer creates a strong barrier that prevents moisture from reaching the steel, reducing the risk of rust. This is especially important in areas where bridges must withstand high traffic loads and variable weather conditions. Intermediate primers are a key part of the coating systems used in infrastructure projects to protect steel components from environmental damage.
Oil and Gas Industry
In the oil and gas industry, intermediate primers play an important role in protecting pipelines, storage tanks, and drilling equipment. These metal surfaces are often exposed to chemicals, moisture, and high temperatures, which can lead to corrosion. Pipelines that transport crude oil or natural gas, for example, are typically coated with multiple layers of protection, including an intermediate primer. This helps prevent leaks and damage caused by corrosive elements. In offshore drilling rigs, intermediate primers are used to protect steel platforms and structures from the corrosive effects of saltwater and harsh weather conditions. This protection is critical for ensuring the safety and functionality of equipment used in these environments.
Aerospace and Aviation
In the aerospace industry, metal components are subject to extreme conditions, including high altitudes, fluctuating temperatures, and UV exposure. Intermediate primers are applied to protect aircraft components, such as wings, fuselages, and landing gear, from corrosion and wear. These primers are formulated to withstand the high stresses and environmental challenges of flight, ensuring that the metal surfaces remain protected. Aircraft wings, for example, benefit from the use of intermediate primers that improve the adhesion of specialised topcoats, which are designed to withstand the pressure and temperature changes that occur at high altitudes. This ensures that the protective coatings on these components remain intact throughout the life of the aircraft.
Frequently Asked Questions (FAQs)
What is the purpose of an intermediate primer in metal coating systems?
Intermediate primers serve as a bonding layer between the base coat and topcoat. They improve adhesion, prevent corrosion, and enhance the overall durability of the coating system.
Can intermediate primers be used on all metal surfaces?
Yes, intermediate primers are designed to work on a wide range of metal surfaces, including steel, aluminium, and galvanised metals. It is important to choose the right product for each specific metal to ensure maximum protection.
How long does an intermediate primer take to dry before applying a topcoat?
The drying time for intermediate primers can vary based on the product and environmental conditions. However, many are formulated for quick drying, allowing the topcoat to be applied within a few hours.
Are intermediate primers resistant to chemicals and solvents?
Many intermediate primers offer resistance to chemicals and solvents, making them suitable for use in industrial environments where metal surfaces may come into contact with corrosive substances.
Is it necessary to use an intermediate primer on metal that has already been painted?
In some cases, intermediate primers can be applied over existing coatings, provided the surface is clean and properly prepared. It is essential to ensure that the primer is compatible with the existing paint system.
Do intermediate primers offer UV protection?
Yes, some intermediate primers are formulated to provide UV resistance. This helps prevent chalking and fading, which can compromise the appearance and performance of the topcoat.
Can intermediate primers be used in high-temperature environments?
Certain intermediate primers are designed to withstand high temperatures, making them ideal for use on metal surfaces exposed to heat, such as machinery or pipelines.
What type of topcoats are compatible with intermediate primers?
Intermediate primers can work with a range of topcoats, including epoxy, polyurethane, and acrylic finishes. The choice of topcoat depends on the specific requirements of the project.
How do I ensure that an intermediate primer will work with my chosen topcoat?
To ensure compatibility between your primer and topcoat, check the product specifications or contact Rawlins Paints' technical support team for guidance on the best products for your project.