- There are no more items in your cart
- Shipping Calculated at checkout
-
Sub-Total (inc. VAT)
£0.00
Need Help?
Micaceous Iron Oxide (MIO) Paints
Micaceous Iron Oxide (MIO) primers at Rawlins Paints - prolong the life of steel structures by using the correct primer, with industrial resistance to weathering and corrosion. Use the sidebar filter to narrow down product options to find the right primer for the job - our MIO primers properly prepare steel surfaces with excellent adhesion, providing better coverage for compatible topcoats. Many of our Micaceous Iron Oxide primers have properties and attributes to better suit your project requirements - low temperature curing, low VOC, high solids, heat resistance, immersion, zinc phosphate and much more. Click for more info.

PPG SigmaCover 435
PPG SigmaCover 435, two-component, high-build, micaceous iron oxide-pigmented, polyamide-cured recoatable epoxy coating. Used as a buildcoat or finish in protective coating systems, for steel and concrete structures exposed to atmospheric land or marine conditions, curing at temperatures down to -10°C (14°F). A high relative humidity...

Sherwin-Williams Macropoxy K267
Sherwin-Williams Macropoxy K267 (formerly known as Epigrip K267/Transgard TG121) is a two-pack, pigmented with micaceous iron oxide, designed as an intermediate coat in conjuction with Macropoxy high performance primers.

Teamac Micaceous Iron Oxide
Available in Silver Grey. Protective paint, designed to provide anti-corrosive protection for steel surfaces. For structural steel, including buildings, bridges, and other metal surfaces. Usable as a finishing coat, or overcoatable with a topcoat.

Jotun Penguard Express MIO
Jotun Penguard Express MIO is a two component amine cured epoxy coating that is a fast drying, micaceous iron oxide (MIO) pigmented, high solids, high build product. Specially designed for new construction where fast dry to handle and over coating times are required. Can be used as a primer, mid coat, finish coat or as a single coat system in...

Flag Anti Rugine (MIO) Anti-Rust Paint
Flag Anti Rugine (MIO) Anti-Rust Paint is a high quality one coat anti-rust metal paint based on Micaceous Iron Oxide. It is a high build primer and/or finish suitable for either brushing or spraying purposes. Ideal for both interior and exterior applications Provides excellent adhesion to ferrous metals and imparts good water resistance...

International Interplus 356
International Interplus 356 is a low VOC, two component, internally flexibilised, high build, low temperature curing (down to -5°C, 23°F), surface tolerant epoxy primer, metallic pigmented with aluminium and lamellar micaceous iron oxide for increased corrosion resistance. A high performance maintenance coating for use on a wide variety of...

Tor HB Micaceous Iron Oxide
Tor HB Micaceous Iron Oxide, a high build anti-corrosive coating for structural steelwork on structures such as cranes, bridges, gantries, tanks, etc. Apply by spray or brush Brush application will only achieve 45 to 70 microns dry film thickness 2 colours available Touch dry in 2 hours Overcoat after 16 hours Micaceous oxide of...

International Intercure 200
International Intercure 200 is a two component epoxy zinc phosphate/micaceous iron oxide primer, formulated on proprietary polymer technology, which provides rapid cure and overcoating even under low temperature conditions. A high solids, low VOC product. As a primer for steelwork intended for use in a wide range of aggressive environments,...
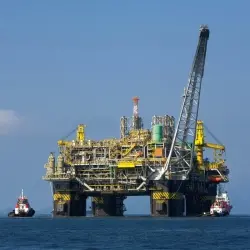
International Intercure 384
International Intercure 384 is a two component, high solids, low VOC epoxy micaceous iron oxide intermediate coating offering excellent barrier protection, low temperature cure and rapid overcoating properties. Pigmented with micaceous iron oxide to comply with the requirements of BS5493:1977 As a high build intermediate to provide...

Zinga Zingaceram HS
Zingaceram HS (Formerly Zingaceram EP MIO HS), a high solid 2 pack intermediate coat to be applied as a sealer over Zinga. The coating has been used on both structural steelwork (for multi-million pound projects) and on sub-sea pipelines. 2 pack system Seals Zinga with good compatibility Apply by brush, roller, conventional sprayer or by...

Sherwin-Williams Macropoxy 267
Macropoxy 267 (formerly known as Sherwin-Williams Macropoxy C267V3 and as Epigrip C267V3) is a high solids 2-pack epoxy, pigmented with micaceous iron oxide. It is used as an undercoat in conjunction with high performance primers. Macropoxy 267 has excellent resistance to moisture, aliphatic solvents, abrasion, alkali spillage, weather and...
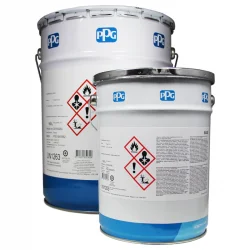
PPG SigmaCover 522
PPG SigmaCover 522 is a two-component, micaceous iron oxide-pigmented, polyamide-cured epoxy primer/sealer/coating. It has excellent adhesion to, and sealing of, weathered, cleaned, zinc-rich primers and metal-sprayed steel, with good adhesion to properly pre-treated galvanized steel. Can be used in systems for atmospheric or water-immersed...

International Intercure 200HS
A fast drying reputation isn`t all International Intercure 200HS is renowned for. Complete with MIO, this fast cure anti-corrosive primer/intermediate with added barrier protection, can improve your productivity and lower your solvent emissions. Primer and intermediate in just one coat Rapid recoat times Low temperature cure, cures down...

International Intergard 475HS
International Intergard 475HS is a low VOC, high solids, high build, two component epoxy coating. Available with conventional pigmentation, or alternatively can be pigmented with micaceous iron oxide to provide enhanced overcoating properties. High solids epoxy intermediate Micaceous Iron Oxide variant for additional barrier protection...

International Intercure 324
International Intercure 324 is a two component, high solids, low VOC, epoxy zinc phosphate/micaceous iron oxide primer. Excellent barrier protection Low temperature cure and Rapid overcoating properties Pigmented with zinc phosphate anti-corrosive pigment to comply with the requirements of BS5493:1977

Hempel Hempadur MIO 47950
Hempadur MIO 47950 is a two-component polyamide adduct cured, high build epoxy paint which combines a relatively high volume solids content with a short drying time. Has a high load of MIO-pigment. For professional use only For use as an intermediate or finishing coat in epoxy systems in atmospheric exposure Service temperature: up to...
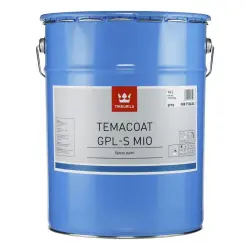
Tikkurila Temacoat GPL-S MIO
Tikkurila Temacoat GPL-S MIO is a two-component, polyamide cured epoxy paint pigmented with micaceous iron oxide, with superior adhesion to steel surfaces forming a very strong and durable film that can be used as a primer or an intermediate coat in aggressive environments Fast cure and low-temperature cure hardeners available - click to...

International Intergard 400
International Intergard 400 is a high build, two component epoxy, pigmented with lamellar micaceous iron oxide for enhanced corrosion resistance and improved overcoating properties after ageing.

Hempel Hempadur Speed-Dry ZP 500
Hempadur Speed-dry ZP 500 is an epoxy paint which combines high volume solids with a short drying time and optimised properties for shop application of full coating systems. It contains zinc phosphate for better corrosion protection. Suitable for onshore corrosion protection of new-build steel and constructions where fast to handle and...

Jotun Penguard HSP MIO
Jotun Penguard HSP MIO is a two component polyamide cured epoxy coating that is a fast drying, micaceous iron oxide (MIO) pigmented, high solids, high build product. Can be used as a primer or a mid coat in atmospheric environments. Specially designed for new construction where fast dry to handle and over coating times are required. *Red,...

International Intercure 420
International Intercure 420 is a two component, high solids, low VOC epoxy micaceous iron oxide coating formulated on proprietary polymer technology which provides rapid cure and overcoating even under low temperature conditions. Excellent barrier protection as part of a high performance system Suitable for use in aggressive environments...
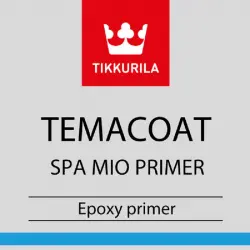
Tikkurila Temacoat SPA Primer MIO
Tikkurila Temacoat SPA Primer MIO, a two-component resin modified epoxy paint containing micaceous iron oxide, used as a primer or an intermediate coat on surfaces exposed to climatic, mechanical and chemical stress. Good adhesion to steel, zinc and aluminium surfaces Recommended for building frameworks, tubular bridges, conveyors and...

Carboline Carboguard 890 MIO
Carboline Carboguard 890 MIO is a highly chemical resistant epoxy mastic coating with exceptionally versatile uses in all steel and concrete industrial markets. Excellent chemical resistance Surface tolerant characteristics Self-priming Available in 350+ colours, including RAL and BS Please note: Colours are sold in the nearest tin...

Carboline Carboguard 893 MIO
Carboline Carboguard 893 MIO is a two-component, high solids corrosion resistant primer or intermediate coat on concrete, steel and (in)organic zinc primers. Excellent corrosion protection Excellent film build and edge protection Used as a primer or an intermediate coating Good abrasion resistance VOC compliant to current AIM...
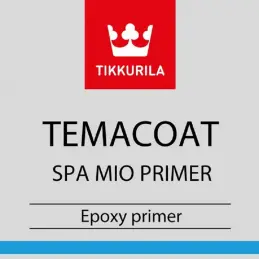
Tikkurila Temacoat SPA MIO
Temacoat SPA MIO, a two component, polyamide-cured epoxy paint, pigmented with aluminium, micaceous iron oxide and zinc phosphate. Good adhesion to steel, zinc and aluminium surfaces Used as a primer or as an intermediate coat in epoxy and polyurethane systems exposed to severe climatic conditions, abrasion, splashes and chemical dust...
Need Help?
Need Help?
What is MIO Paint?
Micaceous Iron Oxide (MIO) paint is a highly specialised protective coating widely used in heavy-duty industrial environments to safeguard steel and other metal surfaces from corrosion, environmental damage, and wear. MIO stands for Micaceous Iron Oxide, a naturally occurring form of iron oxide that has a unique flake-like, lamellar structure. These flakes align themselves in a layered, shingle-like pattern when the paint is applied, creating a highly impermeable and durable protective film.
MIO paints are renowned for their superior resistance to corrosion, particularly in aggressive environments where surfaces are exposed to moisture, chemicals, UV radiation, or saltwater. The paint’s robust formulation ensures that metal substrates remain protected from the degrading effects of rust and corrosion for extended periods, making it a preferred solution in industries where longevity and reduced maintenance are essential. Available in a range of micaceous iron oxide paint colours, these coatings are both functional and visually striking, offering a textured finish ideal for large-scale infrastructure projects.
Where and Why MIO Paints Are Used
MIO paints have found applications in several key sectors due to their exceptional protective qualities. These coatings are predominantly used in situations where structures and equipment are subjected to harsh environmental conditions or exposed to chemicals and moisture that can cause degradation. The primary areas where MIO paints are applied include:
- Marine and Offshore Structures Marine and offshore environments are some of the most challenging settings for metal structures, as they are continuously exposed to saltwater, which accelerates corrosion. Ships, oil rigs, and offshore platforms require high-performance coatings that can withstand both the corrosive effects of salt and the physical wear and tear of constant wave action, loading, and unloading. MIO paint is an ideal choice for protecting these assets because its lamellar structure acts as a barrier to moisture, greatly reducing the risk of rusting and extending the service life of marine equipment.
Common applications include: - Hull protection for ships and boats: The constant immersion of hulls in saltwater makes them highly vulnerable to rust, especially in seawater environments. MIO paint serves as an excellent protective coating for the steel hulls of marine vessels.
- Offshore platforms: Oil rigs and other offshore facilities rely on MIO paints to protect the steel infrastructure from harsh marine conditions, including the corrosive effects of saltwater spray.
- Dockside equipment and containers: Loading cranes, storage containers, and dockside machinery coated with MIO paints benefit from reduced maintenance needs due to the paint’s superior weather resistance.
- Bridges and Infrastructure Bridges, overpasses, and other metal-heavy infrastructure components face constant exposure to moisture, road salts, pollutants, and temperature fluctuations. Without protection, metal components of these structures are prone to rust, leading to weakening and, eventually, structural failures. MIO paint provides a durable, long-lasting solution for protecting steel bridges from these harsh environmental elements.
- Steel beams and supports: Many large infrastructure projects involve the use of steel beams as primary supports. Coating these beams with MIO paint ensures they remain structurally sound, even in environments with high humidity or pollution levels.
- Road barriers and guardrails: These structures are continuously exposed to moisture and road salts, particularly in colder climates. MIO coatings help protect them from the corrosive effects of these elements, increasing their lifespan.
- Industrial Equipment Factories, refineries, and processing plants often have machinery, pipes, and other equipment made from metal, which is vulnerable to corrosion when exposed to moisture, chemicals, or heat. MIO paint is frequently applied to these surfaces to prevent rust and ensure the longevity of critical equipment.
- Chemical plants and refineries: In industrial settings where chemicals and other corrosive substances are handled, MIO paints protect against the degradation of equipment caused by chemical exposure. For example, pipelines used in refineries often benefit from the enhanced protection offered by MIO coatings.
- Manufacturing equipment: Machinery that operates in humid or moist conditions, such as those in food processing plants, benefits from the durable, moisture-resistant properties of MIO paint.
- Petrochemical and Oil & Gas Industries In the oil and gas sector, pipelines, storage tanks, and offshore drilling rigs are all highly susceptible to corrosion due to their exposure to hydrocarbons, chemicals, and saltwater. The use of MIO paint in this industry is critical for maintaining the integrity of essential infrastructure, ensuring continuous operation, and preventing leaks or failures caused by rust.
- Storage tanks: Large storage tanks that hold oil, chemicals, or gases need robust protection against corrosion. MIO coatings offer long-term protection against rust, reducing the need for frequent recoating or repairs.
- Pipeline protection: Pipelines that transport oil and gas, whether underground or exposed, are prone to rust and chemical degradation. MIO paints are applied as part of a corrosion control system to prolong the lifespan of these pipelines.
- Power Plants Power plants of all types—coal, nuclear, hydroelectric, and even renewable energy plants—rely on metal infrastructure that must remain functional under extreme conditions, such as high heat, exposure to chemicals, and humidity. MIO paints are applied to various metal surfaces in power plants to protect against the degrading effects of heat and corrosion.
- Turbine housings: In thermal power plants, turbines are exposed to intense heat and moisture. MIO paint helps protect turbine housings from the combined effects of heat and humidity, extending their operational life.
- Boiler and heat exchanger components: Components of boilers and heat exchangers in power plants often require high-temperature-resistant coatings to prevent corrosion. MIO paints with high heat tolerance are frequently used in these applications.
What Micaceous Iron Oxide Paint is Used On
MIO paints are incredibly versatile and can be applied to a wide range of surfaces, although they are most commonly used on metals, particularly steel. The specific characteristics of MIO paint make it an excellent choice for protecting surfaces in environments that are prone to corrosion, weathering, and chemical exposure. Some of the most common surfaces treated with MIO paint include:
- Structural Steel: Steel is the backbone of modern construction and industrial infrastructure, but it is also highly susceptible to rust when exposed to moisture and oxygen. MIO paint forms an impervious layer on steel surfaces, protecting them from the elements and greatly reducing the risk of corrosion. Steel beams, girders, and frameworks in buildings, bridges, and industrial plants are frequently coated with MIO paint to extend their lifespan and ensure structural integrity.
- Pipelines: Pipelines used in oil, gas, and water distribution are vulnerable to both external and internal corrosion. External exposure to moisture, chemicals, and fluctuating temperatures can degrade pipeline coatings over time. MIO paint provides a highly durable, anti-corrosive coating for both external and internal surfaces of pipelines, ensuring they remain operational without leaks or failures.
- Tanks and Silos: Industrial tanks and silos that store chemicals, water, and other materials need protection from both their contents and the environment. MIO paint is used to coat the exterior and interior surfaces of these structures to prevent rust and chemical degradation. Its high resistance to abrasion also ensures that the coating remains intact, even when exposed to harsh mechanical forces during loading and unloading operations.
- Ships and Marine Vessels: Ships and other marine vessels are constantly exposed to saltwater, which accelerates the rusting process on metal surfaces. MIO paint is commonly used to coat ship hulls, decks, and other metal components that are exposed to water, providing long-term protection from corrosion. Additionally, MIO coatings help prevent biofouling, where marine organisms attach themselves to the ship’s hull, further protecting the vessel from damage.
- Industrial Machinery: Machinery used in factories, refineries, and chemical plants often operates in conditions that promote corrosion. The application of MIO paint helps protect this equipment from the effects of moisture, chemicals, and mechanical wear, reducing the need for frequent maintenance and repairs. MIO coatings are commonly used on machinery components such as conveyors, cranes, and heavy-duty processing equipment.
Top Features to Consider When Purchasing MIO Paint
When selecting a micaceous iron oxide paint, there are several essential features to consider to ensure the right product is chosen for the specific needs of the project. These features will help you identify the right MIO paint for various industrial and structural applications:
- Corrosion Resistance: MIO paints are designed to offer outstanding corrosion protection. The lamellar structure of the micaceous iron oxide flakes creates a barrier that prevents moisture, oxygen, and corrosive substances from penetrating the paint and reaching the underlying metal surface. This corrosion resistance makes MIO paints an excellent choice for environments where metal surfaces are exposed to harsh weather, chemicals, or saltwater.
- Example: In coastal regions, where high humidity and saltwater exposure are common, MIO paints are applied to steel bridges and piers to prevent rust and deterioration.
- Durability: One of the standout features of MIO paint is its durability. The hard, flake-like structure of the micaceous iron oxide particles creates a tough, abrasion-resistant surface that can withstand mechanical wear and tear. This makes MIO coatings ideal for high-traffic areas or environments where surfaces are subjected to heavy use or impact.
- Example: Factories and warehouses often use MIO coatings on machinery and equipment that is exposed to constant physical stress, such as conveyor belts, cranes, and loading docks.
- Adhesion: MIO paints are known for their excellent adhesion properties, meaning they bond securely to the substrate they are applied to. This ensures that the paint remains intact and does not peel, crack, or blister over time, even when exposed to fluctuating temperatures or mechanical stress.
- Example: MIO coatings are commonly used in industrial plants where metal surfaces are exposed to high temperatures, such as boilers and heat exchangers, because of their ability to adhere even under extreme conditions.
- Weather Resistance: MIO paints offer exceptional resistance to UV radiation, rain, snow, and other environmental factors. The micaceous iron oxide flakes reflect UV light, which helps prevent the paint from degrading or fading when exposed to sunlight. This makes MIO coatings an excellent choice for outdoor applications, where long-term exposure to the elements can cause traditional paints to break down.
- Example: In highway infrastructure, such as guardrails and streetlights, MIO paint ensures the surfaces remain protected from the elements, reducing the need for frequent repainting or repair.
- Chemical Resistance: In industrial settings where exposure to chemicals is a regular occurrence, MIO paints provide excellent resistance to acidic, alkaline, and solvent-based chemicals. This makes them ideal for use in environments where traditional paints would degrade or fail due to chemical exposure.
- Example: Chemical processing plants apply MIO paints to pipes, tanks, and reactors to protect them from corrosion caused by the chemicals they handle, extending the operational life of the equipment.
- Ease of Application: Many MIO paints are available in formulations that can be easily applied by brush, roller, or spray, making them versatile and suitable for a wide range of projects. Their ease of application ensures that they can be used effectively on both large industrial surfaces and more intricate components.
- Example: For large infrastructure projects, such as bridges or overpasses, MIO coatings are often applied by spray to ensure even coverage over vast steel surfaces.
- Epoxy Formulations: Epoxy micaceous iron oxide paints offer enhanced protection due to their improved chemical and mechanical resistance. These formulations are particularly useful in environments where both corrosion and physical impact are significant concerns, such as in petrochemical facilities or marine environments.
- Example: Epoxy MIO coatings are applied to offshore oil rigs to protect them from the combined effects of saltwater exposure, mechanical stress from wave action, and chemical exposure from the hydrocarbons being processed.
- Colour Range: While MIO paints are primarily valued for their protective qualities, they are available in a range of micaceous iron oxide paint colours. This allows industries to not only protect their structures but also choose colours that match corporate branding, enhance visibility, or blend in with the surrounding environment.
- Example: Infrastructure projects often use grey or metallic MIO coatings that blend seamlessly with the surrounding environment, while industrial plants may opt for brighter colours to enhance visibility and safety.
- Longevity: One of the most significant benefits of MIO paint is its long service life. The combination of its durability, corrosion resistance, and weather resistance ensures that MIO coatings remain intact for years, reducing the frequency of maintenance and repainting. This longevity makes MIO paint a cost-effective choice for large-scale industrial projects where regular maintenance is both time-consuming and costly.
- Example: Steel bridges coated with MIO paint require significantly less maintenance than those coated with traditional paints, resulting in reduced downtime and maintenance costs over the structure’s lifespan.
Common Uses for MIO Paints
Micaceous Iron Oxide (MIO) paints offer exceptional protective properties that make them indispensable in a wide range of industries. Their ability to resist corrosion, withstand environmental stressors, and protect against wear and tear means they are used in some of the most demanding applications across various sectors. Below are detailed examples of the most common uses of MIO paints, along with specific instances where their unique characteristics prove invaluable.
1. Bridge Coatings
Bridges are often built with steel as the primary structural component due to its strength and flexibility. However, steel is highly susceptible to rust, particularly when exposed to environmental factors such as moisture, salt, and pollution. MIO paints are extensively used as protective coatings on steel bridges to enhance their durability, minimise maintenance needs, and prolong their operational lifespan.
MIO coatings are frequently employed as part of multi-layer paint systems, including primer, intermediate, and topcoat layers. These systems are designed to offer long-lasting protection against environmental factors that would otherwise cause rapid corrosion. The lamellar structure of micaceous iron oxide flakes provides a shingle-like barrier that prevents water, oxygen, and other corrosive agents from reaching the steel surface.
Examples:
- Golden Gate Bridge, USA: Exposed to harsh sea spray and fog in San Francisco Bay, the Golden Gate Bridge has undergone extensive maintenance using corrosion-resistant coatings, including MIO paints, to protect its steel structure. The regular repainting process utilises MIO-based systems to maintain the bridge’s iconic appearance and structural integrity.
- Forth Road Bridge, Scotland: As a major steel suspension bridge exposed to the challenging coastal environment of the Firth of Forth, the Forth Road Bridge is protected with MIO paint to prevent rust. This coating system helps extend the bridge’s life span, even in one of the UK’s harshest climates.
2. Marine Structures
The marine environment is one of the most challenging for metal structures, primarily due to constant exposure to saltwater, high humidity, and fluctuating temperatures. These factors accelerate the corrosion of steel, leading to structural degradation if not adequately protected. MIO paints are widely used in marine and offshore applications because their dense, impermeable barrier effectively blocks saltwater and moisture, providing long-lasting protection against rust.
In addition to protecting steel structures from corrosion, MIO coatings can also reduce the impact of marine organisms such as barnacles and algae, which tend to attach themselves to ship hulls and offshore structures. This can help improve the efficiency of marine vessels by reducing drag and minimising the need for regular cleaning.
Examples:
- Offshore Oil Rigs: Offshore platforms operating in environments like the North Sea and the Gulf of Mexico are subject to intense wave action, salt spray, and extreme weather conditions. MIO paint is applied to the steel framework of these rigs to prevent corrosion and ensure they remain operational for extended periods without costly maintenance or downtime.
- Port Cranes and Dockside Equipment: Loading cranes and other dockside equipment used in ports are regularly exposed to saltwater and harsh weather conditions. MIO paint helps protect these structures from corrosion, allowing them to remain functional even under constant use in corrosive environments.
- Ships and Cargo Vessels: The hulls of ships, which are constantly submerged in seawater, benefit greatly from MIO coatings. These paints help protect the hull from rust and biofouling, reducing maintenance needs and improving the longevity of the vessel.
3. Pipelines and Storage Tanks
In industries such as oil and gas, chemical processing, and water distribution, pipelines and storage tanks are critical assets that require robust protection from both internal and external corrosion. MIO paints are frequently applied to these structures due to their superior ability to resist chemical attack, moisture ingress, and environmental degradation. These coatings are designed to withstand the combined effects of external weathering and the corrosive nature of the substances being stored or transported.
Pipelines that are exposed to the elements, such as those running through deserts or laid offshore, are particularly vulnerable to corrosion. MIO paints are applied as part of protective coating systems that guard against the impact of UV radiation, saltwater, and harsh industrial chemicals.
Examples:
- Oil Pipelines in Desert Regions: In areas such as the Middle East or North Africa, where pipelines are exposed to high temperatures, wind erosion, and sand abrasion, MIO coatings help protect the steel from corrosion caused by intense UV radiation and fluctuating temperatures. The paint’s ability to reflect heat also helps mitigate the effects of thermal expansion and contraction.
- Gas Storage Tanks in Chemical Plants: Large storage tanks holding volatile chemicals or gas are frequently coated with MIO paint to protect against both external weathering and internal chemical corrosion. This ensures that the tanks remain structurally sound and leak-free, even when subjected to aggressive substances.
4. Industrial Equipment
Factories, refineries, and processing plants often rely on heavy-duty machinery that operates in harsh industrial environments. These environments frequently expose equipment to high levels of humidity, chemicals, and mechanical wear, all of which can lead to premature corrosion and equipment failure. MIO paints provide essential protection in these settings, helping industrial machinery remain operational for longer periods and reducing the need for frequent maintenance.
The durability and chemical resistance of MIO coatings make them ideal for equipment such as conveyor systems, cranes, and storage vessels, where constant exposure to moisture, chemicals, or abrasive materials is common. The protective properties of MIO paint also help ensure that sensitive equipment, such as heat exchangers and processing reactors, is shielded from damage.
Examples:
- Food Processing Plants: Equipment used in food processing facilities is often subject to high humidity, frequent washdowns, and exposure to cleaning chemicals. MIO coatings help prevent corrosion on critical machinery, ensuring hygiene standards are maintained and operational downtime is minimised.
- Cement Plants and Kilns: In cement plants, where machinery is exposed to abrasive dust and extreme temperatures, MIO paints are applied to protect the steel framework and mechanical components from wear and corrosion.
- Chemical Reactors and Mixers: MIO coatings are commonly used in chemical plants to protect the internal and external surfaces of reactors and mixers that are exposed to corrosive substances such as acids and solvents. This protection extends the life of the equipment and ensures efficient operation.
5. Power Plants
Power plants, whether they are coal-fired, nuclear, or renewable energy facilities, utilise metal structures and equipment that are constantly exposed to extreme conditions, including high temperatures, steam, and corrosive chemicals. MIO paints are applied to protect these critical components from rust and degradation, ensuring that power generation equipment operates efficiently and reliably.
In particular, components such as boilers, heat exchangers, and cooling towers are coated with MIO paint to resist the combined effects of high heat, moisture, and chemical exposure. The superior heat resistance of some MIO coatings makes them especially useful in high-temperature environments.
Examples:
- Boilers and Turbines in Coal Plants: Boilers and turbines are essential components of coal power plants that operate under extreme heat and pressure. MIO paint is used to coat these components, preventing corrosion caused by high temperatures and moisture from steam.
- Cooling Towers in Nuclear Plants: In nuclear power plants, cooling towers are exposed to high levels of moisture and radiation. MIO paints help protect the steel framework of these towers from rust and corrosion, ensuring the structural integrity of the plant’s cooling system.
- Wind Turbine Structures: Wind turbines, particularly offshore turbines, are exposed to both saltwater and high wind speeds. MIO coatings are applied to the towers and rotor blades to prevent corrosion, ensuring the turbines remain operational and efficient for decades.
6. Highway Infrastructure
Highway infrastructure such as guardrails, streetlights, overhead signposts, and bridges are exposed to environmental factors like rain, snow, road salt, and pollution. These structures are often made of steel, which requires robust protection to prevent corrosion and structural weakening. MIO paints are widely used in this sector due to their ability to provide long-lasting protection in outdoor environments.
MIO paints are commonly used in transportation infrastructure projects because they not only provide excellent corrosion resistance but also enhance visibility and safety through the availability of different colours. These paints are applied to steel components as part of a multi-coat system that ensures the longevity and reliability of vital transportation structures.
Examples:
- Streetlight Poles and Guardrails: In regions that use de-icing salts on roads during winter, streetlight poles and guardrails are constantly exposed to corrosive salt. MIO paint provides these steel components with a durable protective coating that prevents rust, extending the life of the infrastructure and reducing maintenance costs.
- Overhead Highway Sign Supports: The steel structures that hold highway signs are often exposed to harsh weather conditions and pollution. MIO coatings are applied to these supports to protect them from rust and corrosion, ensuring the signs remain securely in place.
- Tunnels and Sound Barriers: Steel components in road tunnels and noise-reducing sound barriers often require additional protection from moisture and vehicle emissions. MIO paint helps safeguard these structures from the corrosive effects of water and exhaust fumes.
7. Historic Building Restoration
In addition to industrial and infrastructure uses, MIO paint is also used in the restoration of historic buildings and landmarks. Many older structures contain steel or iron components, such as window frames, railings, and balconies, that are susceptible to rust over time. MIO paint provides a historically appropriate solution for protecting these metal elements while preserving the structure’s original appearance.
The textured, matte finish of MIO paint mimics the look of aged, weathered metal, making it an ideal choice for restoration projects that require both protective coatings and an authentic aesthetic. The paint’s long-lasting durability ensures that historic structures remain protected from environmental damage for many years.
Examples:
- Cast Iron Railings and Balconies: In heritage buildings, cast iron railings and balconies are prone to rust, particularly in humid or coastal environments. MIO paint is applied to these structures to prevent corrosion and maintain their historical appearance.
- Window Frames and Doors in Victorian Buildings: Many historic buildings feature steel or iron window frames and doors. MIO paint is used to protect these elements from rust while preserving the architectural integrity of the building.
- Industrial Heritage Sites: Former industrial sites that have been converted into museums or public spaces often contain large steel structures that require protection from corrosion. MIO paint is applied to these structures to ensure their preservation for future generations.