- There are no more items in your cart
- Shipping Calculated at checkout
-
Sub-Total (inc. VAT)
£0.00
Need Help?
Oil Tolerant Primers
Specialist oil-tolerant primers offer a unique solution for surfaces contaminated by oil or grease. These primers are specially formulated to bond effectively with substrates where other primers may fail. Commonly used in industrial settings, garages, or repair shops, these primers enable coatings to adhere even on previously oil-exposed surfaces. Their versatility makes them ideal for various metal, concrete, and masonry applications, ensuring a durable base for topcoat finishes. For optimal performance and compatibility, customers are encouraged to contact the technical support team to choose the most suitable product.

403 Oil Tolerant Primer
Developed for use in applications to oil contaminated floors prior to application of subsequent floor toppings. The product exhibits outstanding adhesion to concrete and other substrates and is particularly suitable where compromised surfaces exist. Solvent free, low odour Excellent adhesion to concrete and steel Surface tolerant...

RSL Resuprime OT
2-component epoxy resin floor membrane that combats any residual oil that has escaped into a concrete floor. It ensures that no oil will affect a top finish. Easy application Application onto substrates with engineering oil contamination Excellent adhesion Low odour High solids Formerly known as R.S. Oil Tolerant Primer
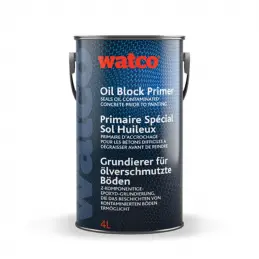
Watco Oil Block Primer
Allows hard to clean, contaminated surfaces, such as concrete floors, to be painted. Ideal for garage-and-machine workshop floors, factories and warehouses Two part epoxy primer Seals in grease and oil and makes a good base for painting Seals and binds weak, porous surfaces More Information Delivery Info
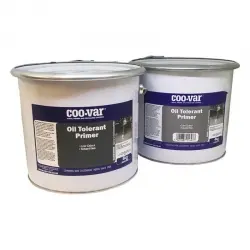
Coo-Var Oil Tolerant Primer
Clear two-component oil-tolerant primer. Improves adhesion on surfaces contaminated with oil. For metal and concrete surfaces. Excellent chemical resistance.
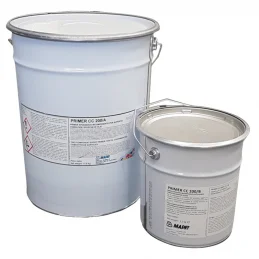
Mapei Primer CC 200
A special primer specifically formulated for oil contaminated cementitious surfaces and it is applied (after the substrate has been adequately prepared) to improve the adhesion of protective epoxy and polyurethane resin coatings on concrete industrial floor and cementitious substrates in general. Some application examples: Adhesion promoter...
Need Help?
Need Help?
Oil-tolerant primers are a game-changing product for industries dealing with surfaces contaminated by oil, grease, or other hydrocarbon-based substances. Unlike conventional primers, which require a meticulously clean substrate for proper adhesion, oil-tolerant primers are formulated to bind securely to surfaces even when residues of oils or greases are present. This makes them indispensable in environments such as automotive repair facilities, factories, and warehouses where oil contamination is frequent, and surface cleaning can be time-consuming or impossible. The ability to prime and coat without needing extensive cleaning not only saves time but ensures long-lasting protection of various surfaces.
In heavy industry, oil-tolerant primers serve as the backbone for coating systems. These products ensure that protective coatings adhere effectively to metal, concrete, or masonry surfaces that have been exposed to oils, lubricants, and even industrial solvents. In environments such as manufacturing plants, machine shops, and maintenance facilities, where oil spills and splashes are common, they are crucial for ensuring long-term structural integrity. Oil-tolerant primers are designed to tackle these challenges head-on, offering a seamless application process without the need for complete surface decontamination, thus reducing downtime and enhancing operational efficiency.
Top Features and Benefits of Oil-Tolerant Primers
One of the standout features of oil-tolerant primers is their exceptional adhesion capabilities. Standard primers often fail to bond correctly to surfaces contaminated by oils or greases, leading to premature failure of the coating system. However, oil-tolerant primers contain specialised binders that allow them to grip onto surfaces even in oily environments, ensuring that the topcoat remains intact and resistant to wear. This means a reduction in the likelihood of blistering, peeling, or flaking, which can occur when traditional primers are used in less-than-ideal conditions.
Oil-tolerant primers are also known for their versatility. These primers can be applied to a range of surfaces, including metals, concrete, and masonry, making them suitable for various industries, from automotive to heavy manufacturing. Their chemical composition allows for strong performance under a wide range of temperatures and conditions, making them adaptable to both indoor and outdoor environments. The flexibility of oil-tolerant primers helps reduce inventory requirements as one product can serve multiple applications.
Another key benefit of oil-tolerant primers is their durability. These products form a robust and resilient film that resists chipping, corrosion, and abrasion, even when subjected to harsh chemicals, oils, and solvents. The ability to create a stable base for further coating layers significantly extends the lifespan of the protective system, reducing the need for frequent re-coating and thereby saving costs in the long term. These primers are also compatible with a variety of topcoat products, which adds to their convenience for end users.
Where Oil-Tolerant Primers Are Commonly Used
Oil-tolerant primers are indispensable across a variety of industries and market sectors, each benefiting from their unique properties that allow for reliable bonding and durable protection even when surfaces are contaminated with oils, grease, and hydrocarbons. From automotive repair shops and industrial plants to marine and food processing environments, oil-tolerant primers offer versatile solutions to many of the challenges faced in these settings. Below, we'll explore the common uses of these primers in more detail, focusing on their role in specific market sectors and the types of surfaces and environments they protect.
Automotive Repair and Workshops
The automotive industry is one of the primary users of oil-tolerant primers. In repair shops and garages, where vehicles, machinery, and tools are regularly exposed to oils, greases, and other automotive fluids, maintaining clean surfaces for coating applications can be extremely difficult. Floors, walls, and metal surfaces often suffer from oil contamination, which can lead to the failure of standard primers and coatings. Oil-tolerant primers, however, are formulated to bond effectively to these contaminated surfaces, ensuring that coatings adhere securely and provide long-lasting protection.
In automotive repair shops, oil-tolerant primers are commonly used on concrete workshop floors that are frequently exposed to oil spills, tyre marks, and heavy equipment. Applying a primer that tolerates oil contamination allows mechanics to maintain safer, more durable floors without having to halt operations for extensive cleaning. These primers are also used on machinery and equipment that come into contact with oils and greases, providing corrosion resistance and ensuring that metal components last longer under harsh working conditions. The use of oil-tolerant primers in automotive facilities reduces downtime, minimises maintenance costs, and enhances the longevity of both the workspace and equipment.
Industrial Maintenance and Manufacturing Plants
Oil-tolerant primers play a crucial role in industrial settings, particularly in maintenance and manufacturing plants where oil spills and contamination are part of everyday operations. Industrial machinery, conveyor belts, and factory floors are constantly exposed to oils, solvents, and industrial fluids that can degrade the surfaces and structures over time. In these environments, stopping production for extensive cleaning is not always feasible, making oil-tolerant primers an invaluable solution.
One of the most common uses of oil-tolerant primers in industrial plants is on the floors and walkways surrounding heavy machinery. Oils and lubricants are often spilled or splashed in these areas, and if left unprotected, the concrete or metal surfaces can become weakened, slippery, or damaged. Oil-tolerant primers provide a secure foundation for additional protective coatings, such as anti-slip floor finishes, ensuring that these surfaces remain safe and durable despite oil exposure.
In addition to floors, oil-tolerant primers are also used on machinery, metal frameworks, and pipes within manufacturing plants. These surfaces are often difficult to keep free of oil contamination, especially in high-traffic areas where production is constant. The ability of oil-tolerant primers to adhere to oily surfaces means that industrial equipment can be coated without interrupting production schedules, protecting against corrosion, wear, and chemical damage while extending the service life of critical infrastructure.
Marine Industry
The marine sector, including shipbuilding, offshore oil platforms, and port facilities, relies heavily on oil-tolerant primers to protect against the dual threats of oil contamination and saltwater corrosion. Marine environments are particularly harsh due to constant exposure to both water and oil-based contaminants, making it essential to use products designed to withstand these challenging conditions.
Ships, boats, and marine structures such as docks and oil rigs are regularly exposed to oil spills, engine lubricants, and other hydrocarbon-based substances. Applying standard primers to these surfaces without removing the oil contamination can result in poor adhesion and premature failure of the protective coating. Oil-tolerant primers are specifically designed to bond effectively to surfaces contaminated with oils, ensuring that marine vessels and structures are adequately protected.
In shipyards and offshore oil platforms, oil-tolerant primers are commonly used on the hulls of ships, metal railings, pipelines, and storage tanks. These surfaces are often exposed to both saltwater and oil-based pollutants, which can lead to rapid corrosion if left unprotected. Oil-tolerant primers not only provide corrosion resistance but also form a strong bond with the substrate, allowing for the successful application of further coatings, such as anti-corrosive paints and water-resistant topcoats.
Food Processing Plants and Commercial Kitchens
In food processing environments and commercial kitchens, oil-tolerant primers serve as an essential tool for maintaining cleanliness and durability in areas frequently exposed to cooking oils, greases, and food residues. Walls, floors, and equipment in these settings are subject to constant oil contamination, which can degrade surfaces and lead to hygiene issues if not properly managed. The use of oil-tolerant primers ensures that these surfaces can be protected without requiring exhaustive cleaning or downtime.
Commercial kitchens are particularly challenging environments when it comes to surface protection. Floors and walls around cooking stations, fryers, and preparation areas are often coated in oils and greases, which are difficult to clean thoroughly. Oil-tolerant primers provide a solution by allowing protective coatings to be applied even on contaminated surfaces, ensuring that these areas remain durable and easy to clean over time.
In food processing plants, where large-scale production of food products occurs, machinery and flooring are constantly exposed to oils and other substances. Oil-tolerant primers help maintain the structural integrity of these surfaces by providing a barrier that prevents oils from penetrating and damaging the substrate. This is particularly important in ensuring that floors remain safe and slip-resistant, and that machinery operates efficiently without the risk of corrosion or chemical damage.
Car Parks and Garages
Concrete floors in car parks and garages are prone to oil contamination from vehicles, making them another ideal setting for the use of oil-tolerant primers. Motor oils, brake fluids, and transmission fluids can all seep into the surface of concrete, weakening it over time and causing it to crack or become discoloured. Oil-tolerant primers allow for the application of protective coatings that seal the concrete, preventing oil and chemical penetration and extending the life of the surface.
In multi-level car parks, where concrete floors are exposed to both vehicle traffic and the elements, oil-tolerant primers play a vital role in preventing wear and tear. They provide a stable base for further coatings such as anti-slip or waterproof layers, ensuring that the surface remains both safe and aesthetically appealing. Garages, whether commercial or residential, also benefit from oil-tolerant primers applied to workbench surfaces, tool storage areas, and machinery.
Chemical Processing Plants
In chemical processing plants, oil-tolerant primers are essential for protecting surfaces exposed to both oils and aggressive chemicals. Pipelines, tanks, and metal structures in these plants often encounter a combination of chemical spills, oil leaks, and solvent exposure, which can lead to rapid corrosion and structural damage if not adequately protected. Oil-tolerant primers ensure that protective coatings adhere securely to these surfaces, even when oil contamination is present.
Chemical plants must comply with stringent safety regulations to ensure that equipment and surfaces are properly maintained. Oil-tolerant primers help these facilities achieve compliance by providing a durable and long-lasting coating solution that resists both oil and chemical exposure. This reduces the need for frequent maintenance and helps prevent costly downtime due to equipment failure.
Oil Refineries and Petrochemical Facilities
Perhaps one of the most critical applications of oil-tolerant primers is in oil refineries and petrochemical facilities, where the presence of oil, grease, and hydrocarbons is a constant challenge. In these environments, surfaces such as storage tanks, pipelines, and metal frameworks are regularly contaminated with oil, making it difficult to apply standard protective coatings. Oil-tolerant primers are specifically designed to bond securely to these surfaces, allowing for the successful application of corrosion-resistant topcoats that protect against harsh chemicals, heat, and moisture.
In oil refineries, the safety and efficiency of the operation depend heavily on the condition of the equipment and infrastructure. Corrosion caused by oil contamination can lead to leaks, mechanical failures, and even accidents if not properly managed. By using oil-tolerant primers, refineries can ensure that their equipment remains protected, reducing the risk of corrosion-related damage and extending the service life of critical infrastructure.
Transport and Logistics Facilities
Transport and logistics hubs, including freight terminals, loading docks, and warehouses, often deal with oil contamination due to the movement of trucks, forklifts, and heavy equipment. Oil-tolerant primers are used in these facilities to protect concrete floors, metal loading docks, and warehouse racking from the wear and tear caused by oil spills, grease build-up, and constant vehicle traffic.
In freight terminals, where large trucks are constantly loading and unloading goods, oil spills can cause significant damage to concrete surfaces if left untreated. Oil-tolerant primers allow for the application of protective coatings that seal the surface, preventing oil from seeping into the concrete and causing cracks or deterioration. This helps reduce maintenance costs and ensures that the terminal remains safe and functional for both workers and equipment.
Public Infrastructure and Transportation
Beyond industrial and commercial applications, oil-tolerant primers are also used in public infrastructure and transportation projects. Bridges, tunnels, and roadways often come into contact with oils, greases, and pollutants from vehicle traffic. Applying oil-tolerant primers to these structures helps ensure that protective coatings adhere effectively, even in contaminated environments. This is especially important in extending the lifespan of critical infrastructure exposed to the elements and urban pollution.
In the railway industry, where tracks, stations, and maintenance facilities are often exposed to oils and greases from locomotives and heavy machinery, oil-tolerant primers are used to protect metal and concrete surfaces from corrosion. These primers provide a crucial layer of protection in high-traffic areas, ensuring that railway infrastructure remains safe, functional, and durable for years to come.
In conclusion, oil-tolerant primers offer versatile solutions across various industries, from automotive repair and industrial maintenance to marine and food processing environments. Their ability to bond securely to contaminated surfaces makes them an essential product for ensuring long-lasting protection in settings where oil contamination is a constant challenge. Whether it's protecting machinery in a manufacturing plant, sealing concrete floors in a car park, or safeguarding metal structures in a marine environment, oil-tolerant primers provide a reliable and durable coating solution that reduces maintenance costs, enhances safety, and extends the life of critical infrastructure.
FAQs
Can oil-tolerant primers be applied to wet or damp surfaces?
Oil-tolerant primers are designed to bond with surfaces contaminated by oil and grease, but most are not intended for application on wet or damp surfaces. Before applying, ensure that the surface is dry to maximise adhesion and performance. However, there are specialised products that might tolerate some moisture—always check product specifications or consult technical support for guidance.
How long does an oil-tolerant primer last before re-coating is necessary?
The longevity of oil-tolerant primers depends on the environmental conditions and the specific use case. In normal industrial or commercial settings, they can last several years before re-coating is required. Factors like heavy mechanical wear, chemical exposure, or outdoor elements can affect the lifespan, so monitoring the coated surfaces regularly is recommended.
Are oil-tolerant primers suitable for residential use?
While oil-tolerant primers are primarily designed for industrial and commercial applications, they can be used in residential settings if necessary, such as in garages or workshops. For residential projects, particularly where oil or grease contamination is present, these primers can be applied to concrete floors, driveways, or outdoor metal fixtures.
Can oil-tolerant primers be tinted or coloured?
Many oil-tolerant primers are available in a range of colours or can be tinted to match specific project requirements. However, not all primers can be tinted, so it's essential to check the product's technical data sheet or consult technical support to determine whether tinting is possible for the chosen primer.
Are oil-tolerant primers resistant to UV light?
Some oil-tolerant primers offer UV resistance, but not all are designed for prolonged exposure to sunlight. For outdoor applications or areas exposed to direct sunlight, it’s crucial to verify the UV resistance of the specific primer and, if necessary, apply a UV-resistant topcoat for additional protection.