- There are no more items in your cart
- Shipping Calculated at checkout
-
Sub-Total (inc. VAT)
£0.00
Solvent-free, two-component epoxy floor coating that provides an economical wear resistant surface on concrete and polymer modified screeds.
- Ronacrete RonaFloor HB100 is available in a range of colours available for decorative appearance and demarcation of zones
- Apply to RonaFloor Epoxy DPM on drying concrete
- BS 8204-6 & FeRFA Class 2 floor coating
- Low maintenance, hygienic surface - Slip resistant with aggregate scatter
- Case studies include use at Royal London Hospital (helicopter landing deck), Gogar Tram Depot, Edinburgh (maintenance pits, workshops, control room, tram wash area, stabling areas)
- Standard and rapid-grade versions available from the drop-down menu below
- RonaFloor HB100 Rapid can be trafficked by foot after only 4-6 hours and by fork lift truck traffic after 12-24 hours
- The Rapid Grade has a shorter working time and pot life and material must therefore be mixed close to the area of application. The mixed resin must be immediately discharged onto the floor and spread before it begins to cure
- For professional and industrial use
Product customisation
Don't forget to save your customization to be able to add to cartRonaFloor HB100 is a FeRFA Class 2 two component, solvent free epoxy floor coatings for use on concrete and polymer modified screeds. RonaFloor HB100 provides excellent abrasion and chemical resistance to floors subject to constant traffic. Cured dry film thickness for a 2 coat application is approximately 0.2mm.
RonaFloor HB100 provides an economical wear resistant surface. RonaFloor HB200 should be used when greater wear is expected or a longer life is required. Apply RonaFloor HB Vertical Grade to vertical surfaces.
Quick Links - Click To Jump To Section:
- Features & Benefits
- Case Studies
- Substrate Preparation
- Application Conditions
- Substrate Priming
- Mixing
- Application
- Cleaning
- Slip Resistance
- Colour Variation
- Chemical Resistance
- Osmotic Blistering
Features & Benefits
- Self smoothing epoxy floor screed
- Seamless
- High strength
- Decorative
- Good chemical resistance
- Easy to clean
- Can be applied to ‘green’ concrete with use of RonaFloor Epoxy DPM
Case Studies
Royal London Hospital
The hospital's helicopter landing pad ensures a swift emergency response to patients requiring attention, flying above the capital's congested roads. RonaFloor HB100 Rapid was applied to the steel structure to provide an anti-slip surface for parademics racing to and from aircraft, curing quickly in just 4 hours to return this vital area back into service fast.
Gogar Tram Depot
The depot services the crucial Glasgow-to-Edinburgh line includes a two storey accommodation block incorporating staff offices and associated staff facilities plus the tramway system control room. It also houses main workshop areas, an internal tram wash area, maintenance pits for tram maintenance as well as stabling areas where the trams are due to be located overnight.
5000m² of RonaFloor HB100 was applied to surfaces to clearly define hazardous areas, and was particular suited for the tram depot's environment due to its resistance to abrasion by constant traffic, its tolerance of train wash chemicals and oil spills.
Substrate Preparation
To achieve optimal adhesion it is essential that RonaFloor HB coatings are applied to structurally sound, clean and dry substrates.
Surfaces must:
- Be prepared after making good any defects in the floor, ensuring that friable materials are removed and replaced (for fast cure repairs refer to RonaFloor Repair 1 Hour data sheets)
- Be prepared by captive shot blasting or similar approved method to produce lightly textured, laitance free surfaces
- Be cleaned to remove grease, oil and dirt
- Be allowed to dry after washing
- Be vacuum cleaned, to remove loose shot and other loose materials
New concrete or screeds should be allowed to dry out for at least 28 days prior to coating. RH at the surface must be below 75% when measured with a hygrometer, or have a moisture content less than 5%.
Application Conditions
The workability and application characteristics of RonaFloor HB100 are adversely affected by low temperature; viscosity and curing time will increase.
Therefore the material should ideally be stored, mixed and applied at 15°C to 20°C.
At lower application temperatures the material should be stored at or warmed to 15°C to 20°C prior to use.
Application characteristics are severely affected below 10°C, minimum application temperature is 5°C.
Substrate Priming
When applying to porous concrete it is advisable to seal the prepared surface with RonaFloor Epoxy Primer, coverage up to 5m² per kg depending on porosity.
Mixing
Add the full contents of the B component to the full contents of the A component and mix with a slow speed drill and spiral mixing paddle (MR3 type) until a homogeneous colour is achieved. Typical mixing time is 3-4 minutes.
Transfer to a shallow paint tray immediately after mixing, or pour onto the floor, to control exothermic reaction and extend working time. This is of even greater importance when using Rapid Grade.
Material must never be taken directly from the mixing vessel, to avoid the risk of unmixed material being used.
Application
Apply minimum 2 coats by short or medium nap mohair or lambswool (not foam) roller directly from a paint tray.
Ensure intimate contact with the surface to ensure the floor is fully wetted.
Ensure that the required thickness is achieved, periodically checking thickness with a wet film gauge.
Do not attempt to apply the coating at a reduced thickness, which may produce roller marks and pigment separation.
The Rapid Grade has a shorter working time and pot life and material must therefore be mixed close to the area of application. The mixed resin must be immediately discharged onto the floor and spread before it begins to cure.
Cleaning
Brushes and tools should be cleaned immediately with xylene based solvent or RonaDeck Low VOC Cleaner.
Slip Resistance
Scatter RonaFloor A/S Aggregate onto the freshly applied first coat at the rate of approximately 1—3kg/m² and allow to cure. Remove excess aggregate with a vacuum cleaner and apply the second coat to encapsulate the aggregate.
Coverage of the second coat will be considerably reduced. The use of A/S Aggregate will reduce the ease with which the floor can be cleaned and the use of cold water power washers or scrubber/ dryers should be considered.
Coating with A/S Aggregate 0.1—0.3mm
- SRV (dry): 70
- SRV (wet): 64
- Surface roughness: 63µ
- Potential for Slip (dry): Extremely Low
- Potential for Slip (wet): Low
Coating with A/S Aggregate 0.4—0.8mm
- SRV (dry): 71
- SRV (wet): 62
- Surface roughness: 95µ
- Potential for Slip (dry): Extremely Low
- Potential for Slip (wet): Low
Colour Variation
Colour variation - Packs should be used in strict batch rotation. Individual areas or rooms should be treated with material from a single batch to avoid the inevitable minor variations in shade resulting from batch manufacture, otherwise matched batches should be used to minimise these variations (an extract from FeRFA Guide To The Specification And Application Of Synthetic Resin Flooring).
Chemical Resistance
- 10% Acetic Acid: Resistant
- 10% Lactic Acid: Spillage only
- 10% Nitric Acid: Spillage only
- 10% Teepol: Resistant
- 16% Bleach: Resistant
- 25% Ammonia: Resistant
- 30% Chromic Acid: Resistant
- 30% Hydrochloric Acid: Resistant
- 50% Phosphoric Acid: Spillage only
- 50% Sodium Hydroxide: Resistant
- 50% Sugar Solution: Resistant
- 20—50% Sulphuric Acid: Spillage only
- Acetone: Not recommended
- Animal Fats: Resistant
- Citric Acid: Resistant
- Engine Oil: Resistant
- Industrial Methylated Spirits: Spillage only
- Methanol: Spillage only
- Petrol: Resistant
- Skydrol: Resistant
- Tap Water: Resistant
- Toluene: Spillage only
- White Spirit: Resistant
- Xylene: Spillage only
Osmotic Blistering
In a few cases severe blistering of thin synthetic resin floorings can occur between 3 months and two years after laying. These blisters commonly vary in size from a few mm in diameter up to 100 mm, with heights up to 15 mm. When drilled into or otherwise broken the blisters are found to contain an aqueous liquid under very high pressure.
The mechanism of their formation is not fully understood but it is assumed because of their physical state that they are caused by a process of osmosis. Because the mechanism is not fully understood it is not possible to be specific about the steps which should be taken to avoid osmotic blistering. However it is considered good practice to take steps in order to minimise the risk (an extract from FeRFA Guidance Note No 2: Osmosis in Resin Flooring ISBN 0 9538020 5 1)
.
Data sheet
- Manufacturer
- Ronacrete
- For Use By
- Professional Use
- Interior / Exterior Use
- Interior Use
- For Use On
- Concrete
Polymer Modified Screed - Application Method
- Roller
- Single, Two or Three Pack
- Two-Pack
- Pack Size
- 5KG
20KG - Pot Life (at 20°C)
- Standard grade: 30-45 minutes
Rapid grade: 10-15 minutes - Coverage
- Up to 25m²/pack/coat depending on surface profile
- Flexural Strength (at 20°C)
- 28N/mm²
- Max. Application Temperature
- 20°C
- Min. Application Temperature
- 5°C
- Layer Thickness
- 0.2mm
- Compressive Strength
- 55N/mm²
- Initial Cure
- Standard grade: 6-8 hours
Rapid cure: 4-6 hours - Colour(s)
- Standard Colours
- Base Type
- Solvent-Free
- Suitable For Use On
- Concrete Screed
- Suitable For Use On
- Polymer Modified Screed
- Finish
- Slip-Resistant
- Application Method
- Roller
- Manufacturer
- Ronacrete
- Usages
- Chemical Resistance
- Product Usage Type
- Topcoat
- Product Range
- RonaFloor
- Foot Traffic
- Standard: 12-24 hours
Rapid: 4-6 hours - Foot Traffic
- Standard grade: 12-24 hours
Rapid cure: 4-6 hours - Forklift Traffic
- Standard grade: 24-48 hours
Rapid cure: 12-24 hours - Full Chemical Resistance
- 7 days
- Abrasion Resistance
- 0.04mm
- Colour Family
- Grey
- Colour Family
- Green
- Colour Family
- Blue
- Colour Family
- Red
- Colour Family
- Yellow
- Colour Family
- Black
- Intercoat Period
- Standard grade: 6-24 hours
Rapid cure: 4-6 hours - Product Type
- Epoxy
- Product Attributes
- Tintable
Questions
Question about the product
Be the first to ask a question about this product!
IMPORTANT SHIPPING & DELIVERY INFORMATION
Ronacrete RonaFloor HB100 is only available with the shipping and delivery timescales listed below - please do not contact our Customer Support Team with enquiries about alternative or earlier shipping and delivery times.
Saturdays and Sundays, as well as Bank Holidays, are not classed as working days.
Orders placed after the cut-off for this product will not be processed for earliest dispatch until 9am the next working day.
All delivery costs below are excluding VAT
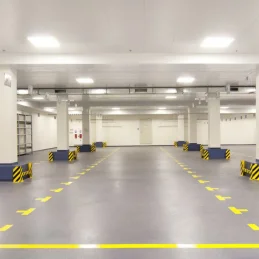
Ronacrete RonaFloor HB200
A FeRFA Class 3 and BS 8204-6, two-component, solvent-free epoxy floor coating for use on concrete and polymer modified screeds. Ronacrete RonaFloor HB200 provides excellent abrasion and chemical resistance to floors subject to constant traffic, suitable for use in chemical plant storage areas, warehousing, toilets, laboratories and food...
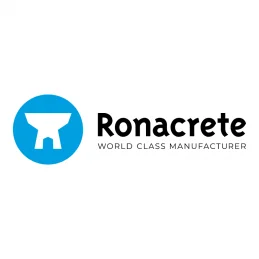
Ronacrete RonaFloor A/S Aggregate
Kiln-dried fine and medium anti-slip aggregate for broadcasting into resin flooring systems. Fine grade (0.1-0.3mm) and medium grade (0.4-0.8mm) available Designed to increase the slip resistance of resin surfaces With the addition of 1-2kg per m2 you can achieve a slip resistance value of up to 70 giving extremely low risk of slip...