- There are no more items in your cart
- Shipping Calculated at checkout
-
Sub-Total (inc. VAT)
£0.00
PPG PhenGuard 985 is a two-component, high-build, amine adduct-cured novolac phenolic epoxy coating. This product has excellent resistance to a wide range of organic acids, alcohols, edible oils, solvents and fats (regardless of free fatty acid content).
- Maximum cargo flexibility
- Can be specified as a 2 or 3 coat system
- Good resistance to hot water
- Pot life of 4 hours [at 20°C (68°F)]
- Primer, Intermediate/finish coat
PPG PhenGuard 985 is a two-component, high-build, amine adduct-cured novolac phenolic epoxy coating. This product has excellent resistance to a wide range of organic acids, alcohols, edible oils, solvents and fats (regardless of free fatty acid content).
Quick Links - Click To Jump To Section:
- Features & Benefits
- Product Data
- Recommended Substrate Conditions & Temperatures
- System Specification
- Instructions For Use
- Spreading Rate and Overcoating Times
- Curing Times and Pot Life
- Safety Information
Features & Benefits
- 2-component, high-build, amine adduct-cured novolac phenolic epoxy coating
- Excellent resistance to a wide range of:
- Organic acids
- Alcohols
- Edible oils
- Fats (regardless of free fatty acid content)
- Solvents
- Maximum cargo flexibility
- Good resistance to hot water
- Pot life of 4 hours [at 20°C (68°F)]
- Can be specified as a 2 or 3 coat system
- Primer, Intermediate/finish coat
Product Data
Basic data at 20°C (68°F)
Data for Mixed Product | |
---|---|
Mass density | 1.7 kg/l (14.2 lb/US gal) |
Volume solids | 66 ± 2% |
VOC (Supplied) | |
max. 339.0 g/l (approx. 2.8 lb/US gal) | |
Recommended dry film thickness | 100 µm - 160 µm (4.0 - 6.3 mils) |
Theoretical spreading rate |
6.6 m²/l for 100 µm (265 ft²/US gal for 4.0 mils) 4.4 m²/l for 150 µm (176 ft²/US gal for 4.0 mils) |
Overcoating Interval | Minimum: 36 hours |
Maximum: 28 days | |
Dry to touch | 2 hours |
Full Cure | See Cure table further below |
Notes:
- Refer to tables below for information regarding spreading rate and film thickness, overcoating intervals and curing times
Recommended Substrate Conditions & Temperatures
Substrate conditions:
- Steel should be blast cleaned in situ to at least ISO-Sa2½
- Blasting profile 50 – 100 µm (2.0 – 4.0 mils)
- Steel must be free from rust, scale, shop primer and any other contamination
- Previous coat must be sound, dry and free from any contamination
Substrate Temperature & Application Conditions:
- Substrate temperature during application and curing should be above 10°C (50°F)
- Substrate temperature during application and curing should be at least 3°C (5°F) above dew point
System Specification
For use as a tank coating
- 2 coats of 150 microns (6mils) each, or 3 coats of 100 microns (4mils) each, to reach 300 microns (12 mils) total dry film thickness
Notes:
- For more information on min and max DFT see 'Explanation of Product Data Sheets' document in the DATA SHEETS tab
- On critical areas of a structure painted with PHENGUARD 985, 10% of the spot readings can be between 600 and 800µm. Individual gauge readings can be between 800 and 900µm. Critical areas are e.g. weld seams, edges, bolts, corners, nuts and areas of difficult access
Instructions For Use
Mixing ratio by volume: base to hardener 88:12
- The temperature of the paint should preferably be above 15°C (59°F), otherwise extra thinner may be required to obtain application viscosity
- Adding too much thinner results in reduced sag resistance and slower cure
- Thinner should be added after mixing the components
Induction time
Allow induction time before use.
Mixed product induction time | |
---|---|
Mixed product temperature | Induction time |
15°C (59°F) | 20 minutes |
20°C (68°F) | 15 minutes |
25°C (77°F) | 10 minutes |
Air spray:
Recommended Thinner
Volume of thinner
- 0 - 10%, depending on required thickness and application conditions
Nozzle orifice
- 2.0 mm (approx. 0.079 in)
Nozzle pressure
- 0.3 MPa (approx. 3 Bar; 44 p.s.i.)
Airless spray:
Recommended Thinner
Volume of thinner
- 0 - 5%, depending on required thickness and application conditions
Nozzle orifice
- Approx. 0.43 – 0.53 mm (0.017 – 0.021 in)
Nozzle pressure
- 15.0 MPa (approx. 150 bar; 2176 p.s.i.)
Brush/Roller:
Brush: for stripe coating and spot repair only
Recommended Thinner
Volume of thinner
- 0 – 5%
Cleaning solvent
Spreading Rate and Overcoating Times
Spreading Rate and Film Thickness
Note: Maximum DFT when brushing: 150 µm (6.0 mils)
Spreading rate and film thickness | |
---|---|
DFT | Theoretical spreading rate |
100 µm (4.0 mils) | 6.6 m²/l |
150 µm (6.0 mils) | 4.4 m²/l |
160 µm (6.3 mils) | 4.1 m²/l |
Overcoating Intervals
Overcoating interval for DFT up to 100 µm (4.0 mils) when used as a primer | ||||||
---|---|---|---|---|---|---|
Overcoating with... | Interval | 10°C (50°F) | 15°C (59°F) | 20°C (68°F) | 30°C (86°F) | 40°C (104°F) |
itself and approved topcoats | Minimum | 60 hours | 48 hours | 36 hours | 24 hours | 16 hours |
Maximum | 28 days | 25 days | 28 days | 21 days | 10 days |
Notes:
- The performance of the applied system strongly depends on the curing degree of the first coat at the time of recoating. Therefore overcoating time between 1st and 2nd coat is extended in comparison between 2nd and 3rd coat (see overcoating details)
- When used as a primer under solvent-free tank linings the DFT must be limited to a maximum of 100 µm
Overcoating interval for DFT up to 160 µm (4.0 mils) when used as a primer | ||||||
---|---|---|---|---|---|---|
Overcoating with... | Interval | 10°C (50°F) | 15°C (59°F) | 20°C (68°F) | 30°C (86°F) | 40°C (104°F) |
itself and approved topcoats | Minimum | 3 days | 58 hours | 45 hours | 30 hours | 20 hours |
Maximum | 28 days | 28 days | 28 days | 21 days | 10 days |
Notes:
- The performance of the applied system strongly depends on the curing degree of the first coat at the time of recoating. Therefore overcoating time between 1st and 2nd coat is extended in comparison between 2nd and 3rd coat (see overcoating details)
- When used as a primer under solvent-free tank linings the DFT must be limited to a maximum of 100 µm
Overcoating interval for DFT up to 100 µm (4.0 mils) when used as intermediate | ||||||
---|---|---|---|---|---|---|
Overcoating with... | Interval | 10°C (50°F) | 15°C (59°F) | 20°C (68°F) | 30°C (86°F) | 40°C (104°F) |
itself and approved topcoats | Minimum | 36 hours | 32 hours | 24 hours | 16 hours | 12 hours |
Maximum | 28 days | 28 days | 28 days | 21 days | 10 days |
Notes:
- Surface should be dry and free from any contamination
Curing Times and Pot Life
Curing Times:
Curing time for DFT up to 150 µm (6.0 mils) | |
---|---|
Substrate temperature | Minimum curing time before transport of cargoes without note 4, 7, 8 or 11 and ballast water or tank test with sea water |
10°C (50°F) | 14 days |
15°C (59°F) | 14 days |
20°C (68°F) | 10 days |
30°C (86°F) | 7 days |
40°C (104°F) | 5 days |
Notes:
- Minimum curing time of before transport of cargoes with note 4, 7, 8 or 11: 3 months
- For detailed information on resistance and resistance notes, please refer to the latest issue of the cargo resistance list
- For transport of methanol and vinyl acetate monomer, a hot cure is required, which cannot be substituted by a service period of 3 months with non-aggressive cargoes
- Adequate ventilation must be maintained during application and curing (please refer to INFORMATION SHEETS 1433 and 1434)
Pot Life:
Pot life (at application viscosity) | |
---|---|
Mixed product temperature | Pot life |
10°C (50°F) | 6 hours |
20°C (68°F) | 4 hours |
30°C (86°F) | 1.5 hours |
Safety Precautions
- This is a solvent-borne paint and care should be taken to avoid inhalation of spray mist or vapour, as well as contact between the wet paint and exposed skin or eyes
- See Safety Data Sheets for detailed information
Data sheet
- Manufacturer
- PPG
- For Use By
- Professional Use
- For Use On
- Steel
- Application Method
- Spray
- Sheen
- Low Sheen
- Colour
- Standard / Ready Mixed
- Single, Two or Three Pack
- Two-Pack
- Pack Size
- 4L, 20L
- Parts
- Two
- Base Type
- -
- Solvent
- -
- Mixing Ratio
- 88:12
- Suitable Substrates
- Steel
- Key Features
- Maximum cargo flexibility with low absorption, Good resistance to hot water, Recognised corrosion control coating (Lloyd's register)
- Dry to Handle (at 20°C)
- -
- Dry to Recoat (at 20°C)
- At 100 DFT As Primer - Minimum: 36 hours, Maximum: 28 days.
- Fully Cured (at 20°C)
- 10 days
- Pot Life (at 20°C)
- 4 hours
- Coverage
- 6.6 m²/l for 100 µm (265 ft²/US gal for 4.0 mils
- Recommended Thinner/Cleaner
- PPG Thinner 90-53, PPG Thinner 91-92
- Unit Contents
- -
- Compatible Primers
- -
- Max. Application Temperature
- -
- Min. Application Temperature
- 10°C (50°F)
- Density
- 1.7 kg/l (14.2 lb/US gal)
- Solids by Volume
- 66 ± 2%
- Heat Resistance (up-to)
- -
- VOC
- max. 191.0 g/kg. max. 339.0 g/l (approx. 2.8 lb/US gal)
- Shelf Life (Once Opened)
- Base/Hardener: at least 12 months when stored cool and dry
- UN Number (Activator)
- UN3470
- UN Number (Base)
- UN1263
- Suitable For Use On
- Steel
- Finish
- Low Sheen
- Application Method
- Spray
- Product Usage Type
- Primer
- Product Range
- PhenGuard
- Colour Family
- Grey
- Colour Family
- Off-White
Questions
Question about the product
Be the first to ask a question about this product!
IMPORTANT SHIPPING & DELIVERY INFORMATION
PPG PhenGuard 985 is only available with the shipping and delivery timescales listed below - please do not contact our Customer Support Team with enquiries about alternative or earlier shipping and delivery times.
Saturdays and Sundays, as well as Bank Holidays, are not classed as working days.
Orders placed after the cut-off for this product will not be processed for earliest dispatch until 9am the next working day.
All delivery costs below are excluding VAT

PPG Thinner 90-53
This thinner has been developed by PPG Protective and Marine Coatings for use with selected paint products.

PPG Thinner 91-92
This thinner has been developed by PPG Protective and Marine Coatings for use with selected paint products.
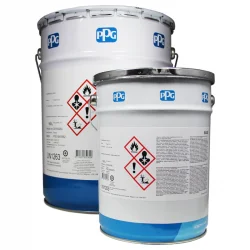
PPG PhenGuard 935
Availability dependant on application; please contact our technical team on 0113 2455450 (option 2) or send a message to [email protected] where we can discuss your project requirements. PPG PhenGuard 935 is a two-component, high-build, amine adduct-cured novolac phenolic epoxy coating, developed as the second coat in the Phenguard...

PPG PhenGuard 940
PPG PhenGuard 940 is a two-component, high-build, amine adduct-cured novolac phenolic epoxy finish; the final coat in the Phenguard tank coating system, with excellent resistance to a wide range of acids, alcohols, edible oils, solvents and fats (regardless of free fatty acid content). Final coat in the PHENGUARD tank coating system:...