- There are no more items in your cart
- Shipping Calculated at checkout
-
Sub-Total (inc. VAT)
£0.00
2-component, high solids modified epoxy cured with an amine adduct curing agent. Designed specifically as a highly chemical-resistant, non-toxic, tank lining.
- Excellent overall chemical resistance to a wide range of acids, alkalies and solvents.
- Particularly good abrasion resistance and flexibility.
- Surface will normally be tack-free in 10 to 12 hours (at 21°C).
- Curing will take place in 5 days (at 32.2°C - or 7 days at 21°C).
- Self-priming.
- Resistant to continous dry temperatures of up to 121°C (204°C for short periods).
This product is only available as PRICE ON APPLICATION - For more information and to place an order please contact us on 0113 2455450 or email [email protected].
Carboline Plasite 9060 is a two-component, high solids modified epoxy cured with an amine adduct curing agent. Designed specifically as a highly chemical-resistant, non-toxic, tank lining.
Click To Jump To Section:
- Features and Benefits
- Product Specification
- Drying Times
- Surface Preparation
- Application Methods
- Health and Safety
Features and Benefits
- Excellent overall chemical resistance to a wide range of acids, alkalies and solvents
- Particularly good abrasion resistance and flexibility
- Tack-free in 10 to 12 hours at 21°C
- Cured for service in 7days at 21°C
- Self-priming
Product Specification
Technical Data | |
---|---|
Carboline Plasite 9060 | |
Volume Solids: | 80% +/- 2% |
Theoretical Coverage Rate: |
31.5 m²/l at 25 microns 5.2 m²/l at 150 microns 4.5 m²/l at 175 microns |
Allow for loss in mixing and application | |
Primer: | Self-priming |
Dry Film Thickness: |
152 - 178 microns per coat Two coats will produce a 300-375 microns film for immersion service |
VOC Values: |
As Supplied: 165 g/l ± 2% VOC Content varies between colours. Contact Rawlins for VOC of specific colours |
Dry Temp. Resistance: |
204°C for short periods: 121°C continuous. Immersion temperatures depend on chemical service |
Flash Point: |
Part A: -4°C Part B: -4°C |
Shelf Life: |
12 months at 21°C Film build drops upon aging |
Performance Data | ||
---|---|---|
Test Method | System | Results |
*Abrasion Resistance (Taber CS-17 Wheel, 1000 gram weight, 1000 cycles) | Plasite 9060 12-15 mils (300-375 microns) | 70 milligrams average loss |
*Surface Hardness (ASTM Method D4366-84) Konig Pendulum (Glass Standard = 250 seconds) | Plasite 9060 12-15 mils (300-375 microns) | 152 seconds |
NACE TM 0174 methodB, testing @ 100°F (38°C) | Plasite 9060 12-15 mils (300-375 microns) |
Gasoline OK Methyl ethyl ketone OK Methyl Alcohol OK |
NACE TM 0174 methodB, testing @ 150°F (65.5°C) | Plasite 9060 12-15 mils (300-375 microns) |
Ethyl Alcohol OK Ammonium Nitrate 65% OK Green Liquor Sulfate Process OK |
NACE TM 0174 methodB, testing @ 180°F (82°C) | Plasite 9060 12-15 mils (300-375 microns) |
Sodium Hydroxide OK Potassium Chloride 50% OK Fatty Acid OK |
NACE TM 0174 methodB, testing @ 210°F (99°C) | Plasite 9060 12-15 mils (300-375 microns) |
Crude Oil OK Ethylene Glycol 30% OK 1,1,1, Trichloroethane OK |
Thermal Shock | Plasite 9060 12-15 mils (300-375 microns) | Unaffected 5 cycles, minus -70°F (-57°C) to plus 200°F (93°C) |
*Note: Above tests were conducted on film cured at 65.5°C
Chemical Resistance
- These tests were conducted on mild steel panels
- The panels are one-half immersed in the solution for the noted time with no effect to the coating
- Plasite 9060 can also be used for more aggressive exposures (acids) for intermittent (splash or fume) use
- Contact Rawlins on Tech - 0113 2455450 (option 2) or [email protected] for specific recommendations
Drying Times
Curing Schedule | ||
---|---|---|
Surface Temp | Cure for Service | Immersion Service (Most Chemical Service) |
21°C | 12 Hours | 7 Days |
32°C | 9 Hours | 5 Days |
41°C | 6 Hours | 4.5 Days |
Drying Time
- Surface will normally be tack-free in 10 to 12 hours at 21°C.
- Curing will take place in 5 days at 32.2°C and 7 days at 21°C
- For food grade service contact Rawlins for specific cure instructions
Recoat Time
- Must be topcoated within two weeks for metal temperature exposure to 54.4°C
- For temperature exposure of 55-66°C, must be topcoated in a maximum of 24 hours
Curing
- Normally curing will take place in 5 days at 32.2°C and 7 days at 21°C
- This coating should not be applied when air temperature or temperature of surface to be coated is below 10°C
- Within 24 hours after coating is applied, a minimum substrate temperature of 21°C is required for proper polymerization. In order to insure the complete removal of solvents and odour, force curing is generally recommended when coating is to be used in food related service
- Force cure as follows: An air-dry time of 2 to 5 hours at temperatures from 21°C to 37.8°C should be allowed before force curing.
- After the air dry period substrate temperature should be raised approximately 18°C each 30 minutes until the desired force curing metal temperature is reached. Curing time begins when the specific substrate temperature is reached
- Non-Food related services: 36 hours @ 49°C, 18 hours @ 55°C, 10 hours @ 60°C, 6.0 hours @ 65°C, 4.5 hours @ 71°C, 3.5 hours @ 77°C, 2.5 hours @ 82°C, 2 hours @ 88°C, 1.75 hours @ 93°C
- Final cure may be checked by exposing coated surface to MIBK for ten minutes. If no dissolving and only minor softening of film occurs, the curing can be considered complete. The film should reharden after exposure if cured. Epoxies may form an amine blush under some conditions. Blush must be removed before coating or placing in some services
Surface Preparation
Preparation | |
---|---|
General: |
Surfaces must be clean and dry Employ adequate methods to remove dirt, dust, oil and all other contaminants that could interfere with adhesion of the coating |
Steel: | Immersion: SSPC-SP10 Non-Immersion: SSPC-SP6 Surface Profile: 2.0-3.0 mils (50-75 micron) |
Aluminium: | Consult Rawlins on Tech - 0113 2455450 (option 2) or [email protected] for recommendations |
Concrete or CMU: | Consult Rawlins on Tech - 0113 2455450 (option 2) or [email protected] for recommendations |
Application Methods
Product Information | |
---|---|
Mixing: |
Power mix coating separately, then add curing agent slowly and mix completely. Do not mix partial kits |
Thinning: |
Thinner 225 E is the preferred thinner Thinners 246, or Plasite Thinner 71 may also be used as alternates depending on temperatures The amounts required will vary depending upon air and surface temperatures and application equipment Normal application temperatures and conditions will require approximately 5 to 10% by volume |
Ratio: | 4:1 A:B |
Pot Life: | Approximately 1 hour at 21°C |
Spray Application (General): | All spray equipment should be thoroughly cleaned of contaminants |
Conventional Spray: | Pressure pot equipped with dual regulators, 3/8” (9.5 mm) I.D. minimum material hose, 0.055-0.070” (0.38-0.53mm) I.D. fluid tip and appropriate air cap |
Airless Spray: |
Pump Ratio: 30:1 (min.) Output: 3.0 GPM (11.5 LPM) (min.) Material Hose: 3/8” (9.5 mm) I.D. (min.) Tip Size: .015-.021” (0.38-0.53mm) Output PSI: 2100-2300 (145-160 bar) Filter Size: 60 mesh |
Brush: |
Not recommended for tank lining applications except when striping welds and touching up Use short-nap solvent resistant roller Use medium bristle brush |
Health and Safety
Clean Up
- Use Carboline Thinner 2, Thinner 71, Thinner 225 E, or Thinner 246
- In case of spillage, absorb and dispose of in accordance with local applicable regulations
Safety
- Observe the precautionary notices on the container label, and read the material safety data sheet before use
- Employ normal workmanlike safety precautions
Ventilation
- When used in enclosed areas, thorough air circulation must be used during and after application until the coating is cured.
- The ventilation system should be capable of preventing the solvent vapor concentration from reaching the lower explosion limit for the solvents used
- User should test and monitor exposure levels to ensure all personnel are below guidelines
- If not sure or if not able to monitor levels, use MSHA/NIOSH approved supplied air respirator
Caution
- This product contains flammable solvents
- Keep away from sparks and open flames
- All electrical equipment and installations should be made and grounded in accordance with regulations
- Refer to the product data sheet and safety data sheets in the attachments section above for further details
Data sheet
- Manufacturer
- Carboline
- For Use On
- Steel, Aluminium, Concrete
- Application Method
- Brush, Spray
- Colour
- Standard / Ready Mixed
- Single, Two or Three Pack
- Two-Pack
- Pack Size
- 3.79L Kit, 18.93L Kit
- Mixing Ratio
- 4:1 A:B
- Coverage
- 31.5 m²/l at 25 microns, 5.2 m²/l at 150 microns, 4.5 m²/l at 175 microns
- Recommended Thinner/Cleaner
- Carboline Thinner 2, Thinner 71, Thinner 225 E, Thinner 246
- Solids by Volume
- 80% +/- 2%
- Heat Resistance (up-to)
- 204°C for short periods: 121°C continuous.
- VOC
- As Supplied: 1.37 lbs/gal (165 g/l) ± 2%
- Shelf Life (from date of manufacture)
- 12 months at 21°C
- Recommended Dry Film Thickness
- 152 - 178 microns per coat
- UN Number (Activator)
- UN3469
- UN Number (Base)
- UN1263
- Pot Life
- Approximately 1 hour at 21°C
- Fully Cured
- 21°C: 12 Hours, 32°C: 9 Hours, 41°C: 6 Hours
- Suitable For Use On
- Concrete
- Suitable For Use On
- Aluminium
- Suitable For Use On
- Steel
- Application Method
- Brush
- Application Method
- Spray
- Product Usage Type
- Tank Lining
- Product Range
- Plasite
Questions
Question about the product
Be the first to ask a question about this product!
IMPORTANT SHIPPING & DELIVERY INFORMATION
Carboline Plasite 9060 is only available with the shipping and delivery timescales listed below - please do not contact our Customer Support Team with enquiries about alternative or earlier shipping and delivery times.
Saturdays and Sundays, as well as Bank Holidays, are not classed as working days.
Orders placed after the cut-off for this product will not be processed for earliest dispatch until 9am the next working day.
All delivery costs below are excluding VAT

Carboline Thinner 2
Carboline Thinner 2 is a thinner for use in industrial coatings.
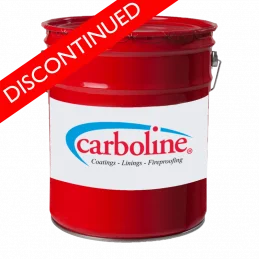
Carboline Thinner 225 E
We no longer stock this product; please contact our technical team on 0113 2455450 (option 2) or send a message to [email protected] where we will be happy to find an alternative product.
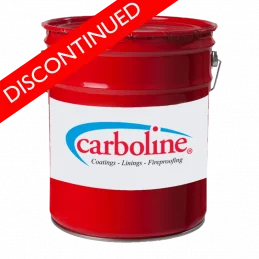
Carboline Thinner 246
We no longer stock this product; please contact our technical team on 0113 2455450 (option 2) or send a message to [email protected] where we will be happy to find an alternative product.

Surface Preparation Kits for Steel
These surface preparation kits for steel have been created to help provide customers with an easily accessible bundle of tools to aid in the preparation of steel surfaces in accordance with ISO 8501-1 (St2/3) and SSPC (SP 2/3). Please click here for important information about these kits. Kit Contents: SET 1 (Hand Tools) 1 x Rust-Oleum...