- There are no more items in your cart
- Shipping Calculated at checkout
-
Sub-Total (inc. VAT)
£0.00
Carboline Polyclad 975 is an advanced two-component, 100% solids, hybrid epoxy pipeline coating. Polyclad 975 has performance properties designed for corrosion protection of steel and ductile iron pipe exteriors, girth welds or tie-ins.
- Quick dry to touch and QC times
- Colour indicator confirms proper mixing
- Low temperature cure 4.4°C
- Excellent cathodic protection performance
- Film build up to 50 mils DFT in one coat
- Excellent edge retention
- Superior adhesion to steel
- Excellent adhesion over prepared FBE, epoxy and polyurethane coated pipe
- Can be applied by spray, brush, roller, or dual cartridge
This product is only available as PRICE ON APPLICATION - For more information and to place an order please contact us on 0113 2455450 or email [email protected].
Carboline Polyclad 975 is an advanced two-component, 100% solids, hybrid epoxy pipeline coating. Polyclad 975 has performance properties designed for corrosion protection of steel and ductile iron pipe exteriors, girth welds or tie-ins. It can be used for new pipe or rehabilitation of coated pipe. Polyclad 975 cures fast to allow quick QC and backfill times.
Designed for spray application. Use Polyclad 975 H for hand applied applications.
Approvals
- Meets criteria for AWWA C210-7
Click To Jump To Section:
- Features and Benefits
- Product Specification
- Drying Times
- Surface Preparation
- Application Methods
- Application Conditions
- Health and Safety
Features and Benefits
- Quick dry to touch and QC times
- Colour indicator confirms proper mixing
- Low temperature cure 4.4°C
- Excellent cathodic protection performance
- Film build up to 50 mils DFT in one coat
- Excellent edge retention
- Superior adhesion to steel
- Excellent adhesion over prepared FBE, epoxy and polyurethane coated pipe
- Can be applied by spray, brush, roller, or dual cartridge
Product Specification
Technical Data | |
---|---|
Carboline Polyclad 975 | |
Volume Solids: | 99% +/- 1% |
Theoretical Coverage Rate: |
39.0 m²/l at 25 microns 1.9 m²/l at 500 microns 1.3 m²/l at 750 microns |
Allow for loss in mixing and application | |
Primer: | Self-priming |
Dry Film Thickness: |
508 - 762 microns typical DFT with hand application 508 - 762 microns typical for spray application Application up to 1250 microns in one coat is acceptable |
VOC Values: | As Supplied : 5 g/l |
Dry Temp. Resistance: |
Continuous: 93°C Non-Continuous: 121°C |
Flash Point: |
Part A: 96°C Part B: 96°C |
Shelf Life: |
Part A: 24 months Part B: 24 months *Shelf life: (actual stated shelf life) when kept at recommended storage conditions and in original unopened containers |
Storage and Humidity: |
4-43°C 0-90% Relative Humidity |
Performance Data | ||
---|---|---|
Test Method | System | Results |
Cathodic Disbondment ASTM G-95, 24°C (75°F), -1.5 V, 28 days | 20 to 30 mils DFT (500 to 750 microns) | <3 mm |
Cathodic Disbondment ASTM G-95, 65°C (149°F), -1.5 V, 28 days | 20 to 30 mils DFT (500 to 750 microns) | <4 mm |
Cathodic Disbondment ASTM G-95, 65°C (149°F), -3.0 V, 7 days | 20 to 30 mils DFT (500 to 750 microns) | <5 mm |
Cathodic Disbondment ASTM G-95, 80°C (176°F), -1.5 V, 28 days | 20 to 30 mils DFT (500 to 750 microns) | <6 mm |
Chemical resistance immersion, NACE TM 0174 method-B, 24°C for 7 days | 20 to 30 mils DFT (500 to 750 microns) | Results below |
Chemical tested: 10% Nitric Acid | 20 to 30 mils DFT (500 to 750 microns) | Pass, no effect |
Chemical tested: 10% Sodium Chloride | 20 to 30 mils DFT (500 to 750 microns) | Pass, no effect |
Chemical tested: 10% Sodium Hydroxide | 20 to 30 mils DFT (500 to 750 microns) | Pass, no effect |
Chemical tested: 5% Sulfuric Acid | 20 to 30 mils DFT (500 to 750 microns) | Pass, no effect |
Chemical tested: Fuel Grade Ethanol | 20 to 30 mils DFT (500 to 750 microns) | Pass, no effect |
Chemical tested: Toluene | 20 to 30 mils DFT (500 to 750 microns) | Pass, no effect |
Flexibility, CSA Z245.20-10 (12.11) at 23°C | 27 to 30 mils DFT (686 to 750 microns) | Pass 1.0°/pd |
Impact resistance, ASTM D2794 | 20 to 30 mils DFT (500 to 750 microns) | 45 in-lbs |
Shore D hardness, ASTM D2240 | 30 to 40 mils DFT (750 to 1000 microns) | 75-85 Shore D |
Wet Adhesion, hot water soak for 24 hours | 20 to 30 mils DFT (500 to 750 microns | Rating #1 |
Drying Times
Curing Schedule | |||
---|---|---|---|
Surface Temp | Dry to Handle | Dry to Touch | Maximum Recoat Time |
2°C | 15 Hours | 6 Hours | 12 Hours |
10°C | 13 Hours | 3.5 Hours | 6 Hours |
24°C | 3 Hours | 1 Hour | 4 Hours |
32°C | 1.5 Hours | 0.75 Hours | 2 Hours |
- Over-coating after the maximum recoat time requires that the surface be abraded prior to application
- Use a medium grit, 60 to 80 grit paper or sweep blast to roughen the surface
- Clean abraded area of dust before recoating or repair
- Coating is ready for backfill when it is "thumb nail" hard
- The thumb nail hardness is defined by when one cannot make a permanent indention in the coating with one's thumb
Surface Preparation
Preparation | |
---|---|
General: |
All sharp edges shall be ground to produce a radius and all imperfections, such as, delaminations, scabs, slivers and slag shall be corrected prior to abrasive blasting Degrease surface prior to abrasive blast in accordance to SSPC SP-1 Organic solvents, alkaline solutions, steam, hot water with detergents or other systems that will completely remove dirt, oil, grease, etc. may be used |
Steel: | Steel substrate must be blasted to a minimum Near-White Metal Finish (SSPC SP10 or NACE NO. 2) with a 2.5 to 4.5 mil (62 to 112 microns) dense, sharp angular profile |
Application Methods
Product Information | |
---|---|
Mixing: |
Power mix part A and part B separately until uniform for plural airless spray application Do not over mix or incorporate air by mixing too fast Hand apply kits are hand mixed until colour is consistent Green kit consists of Part A in yellow 0600; Part B in blue P100 Grey kit consists of Part A in grey 0700; Part B in 0909 Blue kit consists of Part A in blue 0100; Part B in 0909 |
Thinning: | Thinning is not required |
Ratio: | 4:1 Ratio by volume (A to B) |
Pot Life: |
15 minutes @ 23°C *These are general guidelines for the application of this product. Job site conditions may require modifications to these guidelines to achieve the desired results |
Conventional Spray: | Not recommended |
Airless Spray: |
Use fixed ratio (4:1 by volume) heated plural component spray equipment with heated hoppers, heated hoses leading to a mixer manifold and static mixer, attach to a 15 to 25 ft. ¼” ID whip hose (depending on tip size used) followed by an airless gun utilizing self-cleaning reverse “a” tips from 0.019-0.031 inches Check with Rawlins on Tech - 0113 2455450 (option 2) or [email protected] to review your application set up Note: Heat the “A” side material to 43-54°C and the “B” side material to 90 to 32-38°C Fluid pressure will range from 2500 to 3500 psi. This will ensure proper spraying Take care to prevent the mixed material from setting up in your whip hoses For best results, keep your whip hoses as short as possible, purge them immediately if work is interrupted, keep them insulated from hot surfaces |
Brush and Roller (General): |
May be hand applied for small repair areas by first mixing the coating and spreading the coating to desire thickness using brush or roller Polyclad 975 H is our hand applied version and is better suited for hand application |
Application Conditions
Conditions | ||||
---|---|---|---|---|
Condition | Material | Surface | Ambient | Humidity |
Minimum | 32°C | 4°C | -7°C | 0% |
Maximum | 54°C | 43°C | 43°C | 90% |
- This product simply requires the substrate temperature to be above the dew point
- Condensation due to substrate temperatures below the dew point can cause flash rusting on prepared steel and interfere with proper adhesion to the substrate
Health and Safety
Clean Up
- Use Thinner 2 or Thinner 225 E
- In case of spillage, absorb and dispose of in accordance with local applicable regulations
Safety
- Observe the precautionary notices on the container label, and read the Material Safety Data Sheet before use
- Employ normal workmanlike safety precautions
Ventilation
- When used as a tank lining or in enclosed areas, thorough air circulation must be used during and after application until the coating is cured
- Minimal protection is needed when proper ventilation is achieved
Caution
- This product contains flammable solvents
- Keep away from sparks and open flames
- All electrical equipment and installations should be made and grounded in accordance with regulations
- In areas where explosion hazards exist, workers should be required to use non-ferrous tools and wear conductive and non-sparking shoes
- Refer to the product data sheet and safety data sheet in the attachments section above for further details
Data sheet
- Manufacturer
- Carboline
- For Use By
- Industrial Use
- For Use On
- Steel
- Application Method
- Brush, Roller, Spray
- Sheen
- Semi-Gloss
- Colour
- Standard / Ready Mixed
- VOC Levels
- Ultra-Low (5-49 g/l)
- Single, Two or Three Pack
- Two-Pack
- Product Certifications
- AWWA C210-7
- Mixing Ratio
- 4:1 Ratio by volume (A to B)
- Coverage
- 39.0 m²/l at 25 microns, 1.9 m²/l at 500 microns, 1.3 m²/l at 750 microns
- Recommended Thinner/Cleaner
- Carboline Thinner 2, Thinner 225E
- Max. Application Temperature
- Material: 54°C, Surface: 43°C, Ambient: 43°C, Humidity: 90%
- Min. Application Temperature
- Material: 32°C, Surface: 4°C, Ambient: -7°C, Humidity: 0%
- Solids by Volume
- 99% +/- 1%
- Heat Resistance (up-to)
- Continuous: 93°C, Non-Continuous: 121°C
- VOC
- 5 g/l
- Shelf Life (from date of manufacture)
- 24 months
- Touch Dry
- 2°C: 6 Hours, 10°C: 3.5 Hours, 24°C: 1 Hour, 32°C: 0.75 Hours
- Recommended Dry Film Thickness
- 508 - 762 microns
- UN Number (Activator)
- UN3066
- UN Number (Base)
- UN3082
- Dry to Handle (at 10°C)
- 13 Hours
- Pot Life
- 15 minutes @ 75°F
- Suitable For Use On
- Steel
- Finish
- Semi-Gloss
- Application Method
- Brush
- Application Method
- Roller
- Application Method
- Spray
- Product Usage Type
- Pipe Lining
- Product Range
- Polyclad
- Categorised As
- Special Use > Low Temperature Tank & Pipe Lining Coatings
- Seasonal
- Cold Weather
- For Tanks or Pipes
- Pipe
Questions
Question about the product
Be the first to ask a question about this product!
IMPORTANT SHIPPING & DELIVERY INFORMATION
Carboline Polyclad 975 is only available with the shipping and delivery timescales listed below - please do not contact our Customer Support Team with enquiries about alternative or earlier shipping and delivery times.
Saturdays and Sundays, as well as Bank Holidays, are not classed as working days.
Orders placed after the cut-off for this product will not be processed for earliest dispatch until 9am the next working day.
All delivery costs below are excluding VAT

Carboline Polyclad 975 H
Carboline Polyclad 975 H is an advanced two-component epoxy, 100% solids, hybrid epoxy pipeline coating. Quick dry to touch and QC times - good brush and roll properties Colour indicator confirms proper mixing Low temperature cure 4.4°C Excellent cathodic protection performance Film build up to 30 mils DFT in one coat Excellent edge...

Carboline Thinner 2
Carboline Thinner 2 is a thinner for use in industrial coatings.
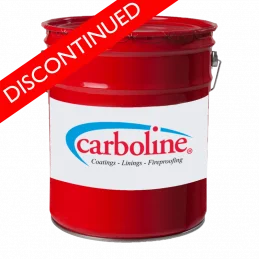
Carboline Thinner 225 E
We no longer stock this product; please contact our technical team on 0113 2455450 (option 2) or send a message to [email protected] where we will be happy to find an alternative product.

Surface Preparation Kits for Steel
These surface preparation kits for steel have been created to help provide customers with an easily accessible bundle of tools to aid in the preparation of steel surfaces in accordance with ISO 8501-1 (St2/3) and SSPC (SP 2/3). Please click here for important information about these kits. Kit Contents: SET 1 (Hand Tools) 1 x Rust-Oleum...