- There are no more items in your cart
- Shipping Calculated at checkout
-
Sub-Total (inc. VAT)
£0.00
PPG PSX 700 is a two-component, engineered siloxane coating that can be applied directly over inorganic zinc. Offers good resistance to splash and spillage of chemicals.
- Available in 2,500+ colours, inc. RAL, BS, NCS & the new NCS 2050 colours
- Used on Adelaide Oval Cricket Ground in Adelaide, South Australia, Rio Tinto Dampier Salt Jetty, Cape Cuvier, Australia, and Burnett River Bridge, Queensland, Australia
- Unique, high-gloss, isocyanate free solution
- SSPC Paint 36 Level 3 Performance
- NFPA Class A Flame Spread
- Qualified for ISO 12944 C5 with several systems
- Qualified for NORSOK M501 Rev.6 System 1 with several systems
- Meets requirements of ANSI N5.12 and ASTM D5144 for Coating Service Level II
Product customisation
Don't forget to save your customization to be able to add to cartPPG PSX 700 is a two-component, engineered siloxane coating that can be applied directly over inorganic zinc. Offers good resistance to splash and spillage of chemicals and can be applied by brush, roller or spray, without thinning.
Please Note: Fast Drying Hardener is available on request and subject to extended lead times please contact our Technical Department on 0113 2455450 (option 1) or send a message to [email protected] for details.
Features & Benefits
- Available in 2,500+ colours, inc. RAL, BS, NCS & the new NCS 2050 colours
- Used on Adelaide Oval Cricket Ground, Riverbank Stand, Adelaide, South Australia, Rio Tinto Dampier Salt Jetty, Cape Cuvier, Australia, Burnett River Bridge, Queensland, Australi, Danser van Gent Shipping, Delfzijl, The Netherlands
- Unique, high gloss, isocyanate free solution
- Excellent colour and gloss retention
- Resists graffiti
- High solids, VOC compliant
- Can be applied as a single coat, direct-to-metal for moderately corrosive environments (ISO 12944 C1-C3)
- Gloss finish
- SSPC Paint 36 Level 3 Performance
- NFPA Class A Flame Spread
- Qualified for ISO 12944 C5 with several systems
- Qualified for NORSOK M501 Rev.6 System 1 with several systems
- Meets requirements of ANSI N5.12 and ASTM D5144 for Coating Service Level II
Product Data
Basic data at 20°C (68°F)
Data for Mixed Product | |
---|---|
Number of components | Two |
Mass density | 1.4 kg/l (11.3 lb/US gal) |
Volume solids | 90 ± 2% |
VOC (supplied) | Directive 1999/13/EC, SED: max. 119.0 g/kg. max. 164.0 g/l (approx. 1.4 lb/US gal) EPA Method 24: 0.7 lb/US gal (84.0 g/l) |
Temperature resistance (continuous) | To 120°C (250°F) |
Recommended dry film thickness | 75 - 175 µm (3.0 - 7.0 mils) per coat |
Theoretical spreading rate | 7.2 m²/l for 125 µm (289 ft²/US gal for 5.0 mils) |
Dry to touch | 2 hours |
Overcoating interval | Minimum: 3 hours. Maximum: Unlimited |
Shelf life | Base: at least 36 months when stored cool and dry. Hardener: at least 24 months when stored cool and dry |
Notes:
See addtional data: Spreading rate and film thickness, Overcoating intervals and Curing time. When applying more than one coat, it is recommended that the total DFT should not exceed 250 µm (10.0 mils). Colour will drift at elevated temperatures.<p>
Recommended Substrate Conditions and Temperatures
- Coating performance is proportional to the degree of surface preparation.
- Steel; pretreated minimum ISO-Sa2 (SSPC SP-6) or higher with blasting profile 25 – 75 µm (1.0 – 3.0 mils).
- For touch up and repair, power tool cleaning in accordance with SSPC SP-11 is acceptable.
- Galvanized steel; sweep blasted to roughen the surface to remove any zinc salts which might be present, SSPC SP-16 with blasting profile 40 – 75 µm (1.5 – 3.0 mils).
- Stainless steel and non-ferrous metal; degreased and sweep blast, SSPC SP-16 with blasting profile 40 – 100 µm (1.5 – 4.0 mils).
- Concrete / Masonry; see specific primer.
- Compatible previous coat must be dry and free from any contamination.
- When applied to zinc silicate primer, a mist coat and full coat technique is required. 15% thinning is recommended for mist coat.
- Aged suitable coating must be dry and free from any contamination, it may require abrading prior to applying this product.
- Prepare damaged areas to original surface preparation specifications, feathering edges of intact coating.
- Substrate temperature during application and curing should be above 0°C (32°F).
- Substrate temperature during application and curing should be at least 3°C (5°F) above dew point.
- Relative humidity during application and curing should be above 40% to obtain optimal curing properties.
Note: FD hardener should be used when ambient temperature is below 5°C (40°F).
System Specification
Primers: Direct to substrate, DIMETCOTE Series, AMERCOAT 68 Series, AMERLOCK 400 / 2 Series, SIGMAZINC Series, AMERCOAT Epoxies and SIGMA Epoxies.
Instructions for Use
Mixing ratio by volume: base to hardener 80:20 (4:1). Use a power mixer powered by an air or explosion-proof electric motor. No induction time required. Pot life is 4 hours at 20°C (68°F); Note: See ADDITIONAL DATA – Pot life.
Air spray
Recommended thinner: THINNER 60-12 (AMERCOAT 911) or THINNER 21-06 (AMERCOAT 65) for global, THINNER 21-25 (AMERCOAT 101) is recommended for above 90°F (32°C) in US only
Volume of thinner: 5 - 10%, depending on required thickness and application conditions
Nozzle orifice: 1.5 – 2.0 mm (approx. 0.060 – 0.079 in)
Nozzle pressure: 0.3 - 0.4 MPa (approx. 3 - 4 bar; 44 - 58 p.s.i.)
Airless spray
Recommended thinner: THINNER 60-12 (AMERCOAT 911) or THINNER 21-06 (AMERCOAT 65) for global, THINNER 21-25 (AMERCOAT 101) is recommended for above 90°F (32°C) in US only
Volume of thinner: 0 - 5%, depending on required thickness and application conditions
Nozzle orifice: Approx. 0.38 – 0.48 mm (0.015 – 0.019 in)
Nozzle pressure: 20.0 MPa (approx. 200 bar; 2901 p.s.i.)
Brush/roller
The recommended DFT cannot be reached in one coat. Use a high quality natural bristle brush and/or solvent resistant, short nap roller. Ensure brush / roller is well loaded to void air entrainment. Be sure to maintain a wet edge.
Cleaning solvent
THINNER 90-53, THINNER 90-58 (AMERCOAT 12) or THINNER 60-12 (AMERCOAT 911)
Spreading Rate and Film Thickness
DFTTheoretical Spreading Rate
75 µm (3.0 mils) | 12.0 m²/l (481 ft²/US gal) |
125 µm (5.0 mils) | 7.2 m²/l (289 ft²/US gal) |
175 µm (7.0 mils) | 5.1 m²/l (206 ft²/US gal) |
Pot Life
10°C (50°F) = 6.5 hours
20°C (68°F) = 4 hours
30°C (86°F) = 1.5 hours
Note:
Same pot life between normal and FD hardener.
Overcoating interval for DFT up to 175 µm (7.0 mils) at RH 40% or above~
Itself (when PSX7OO is used) Miniumum
Maximum N/A
N/A 20 hours
Unlimited 9 hours
Unlimited 4.5 hours
Unlimited 3 hours
Unlimited
Overcoating with... | Interval | 0°C (32°F) | 5°C (41°F) | 10°C (50°F) | 20°C (68°F) | 30°C (86°F) |
Itself (when PSX700FD is used) | Minimum Maximum |
20 hours Unlimited |
12 hours Unlimited |
7 hours Unlimited |
3 hours Unlimited |
2 hours Unlimited |
Notes:
Surface should be dry and free from any contamination. When re-coat between dry through time and 7 days, solvent wipe surface with any of PSX 700 thinners prior to application of the second coat of PSX 700. Hardener manufactured in Europe is fast drying version only with "PSX 700 FDE Hardener" name.
Curing time with standard hardener for DFT up to 175 µm (7.0 mils) at RH 40% or above
Substrate temperature | Dry to touch | Dry to handle |
5°C (41°F) | 9 hours | 24 hours |
10°C (50°F) | 6 hours | 11 hours |
20°C (68°F) | 3 hours | 6 hours |
30°C (86°F) | 1.5 hours | 4 hours |
Curing time with FD (fast drying) hardener for DFT up to 175 µm (7.0 mils) at RH 40% or above
Substrate temperature | Dry to touch | Dry to handle |
0°C (32°F) | 9 hours | 24 hours |
5°C (41°F) | 7 hours | 16 hours |
10°C (50°F) | 4.5 hours | 8.5 hours |
20°C (68°F) | 2 hours | 4.5 hours |
30°C (86°F) | 1 hours | 3 hours |
Notes:
Adequate ventilation must be maintained during application and curing. Hardener manufactured in Europe is fast drying version only with "PSX 700 FDE Hardener" name.
Please Note: Fast Drying Hardener is available on request and subject to extended lead times please contact our Technical Department on 0113 2455450 (option 1) or send a message to [email protected] for details.
Safety Precautions
This is a solvent-borne paint and care should be taken to avoid inhalation of spray mist or vapor, as well as contact between the wet paint and exposed skin or eyes. For paint and recommended thinners, see information sheets 1430, 1431 and relevant Material Safety Data Sheets.
Data sheet
- Manufacturer
- PPG
- For Use On
- Steel
- Application Method
- Brush, Roller, Spray
- Sheen
- Gloss
- Colour
- Fully Tintable
- Single, Two or Three Pack
- Two-Pack
- Pack Size
- 5L, 20L
- Parts
- Two
- Solvent
- Solvent Based
- Mixing Ratio
- 4:1
- Suitable Substrates
- Steel, galvanised steel and non-ferrous metals, concrete & masonry
- Key Features
- Resists graffiti, excellent colour and gloss retention, isocyanate free solution
- Touch Dry (at 20°C)
- 3 hours
- Dry to Handle (at 20°C)
- 6 hours
- Dry to Recoat (at 20°C)
- 4.5 hours
- Fully Cured (at 20°C)
- -
- Pot Life (at 20°C)
- 4 hours
- Coverage
- 7.2 m²/l for 125 µm (289 ft²/US gal for 5.0 mils)
- Recommended Thinner/Cleaner
- PPG Thinner 60-12, PPG Thinner 21-06, PPG Thinner 90-53, PPG Thinner 90-58
- Unit Contents
- -
- Compatible Primers
- -
- Compatible Topcoats
- Itself
- Max. Application Temperature
- -
- Min. Application Temperature
- 0°C (32°F), and at least 3°C (5°F) above dew point
- Density
- 1.4 kg/l (11.3 lb/US gal)
- Solids by Volume
- 90 ± 2%
- Heat Resistance (up-to)
- 120°C (250°F)
- VOC
- Directive 1999/13/EC, SED: max. 119.0 g/kg. max. 164.0 g/l (approx. 1.4 lb/US gal) EPA Method 24: 0.7 lb/US gal (84.0 g/l)
- Shelf Life (Once Opened)
- Base: at least 36 months when stored cool and dry. Hardener: at least 24 months when stored cool and dry
- UN Number (Activator)
- UN3469
- UN Number (Base)
- Not Regulated
- Base Type
- Solvent-Based
- Suitable For Use On
- Steel
- Suitable For Use On
- Galvanised Steel
- Suitable For Use On
- Primed Surfaces
- Suitable For Use On
- Compatible Existing Coatings
- Suitable For Use On
- Stainless Steel
- Finish
- High Gloss
- Application Method
- Brush
- Application Method
- Roller
- Application Method
- Spray
- Usages
- Direct to Metal
- Usages
- High Solids
- Usages
- Chemical Resistance
- Usages
- Atmospheric
- Usages
- Gloss Retention
- Usages
- Isocyanate Free/Non-Isocyanate
- Usages
- Colour Retention
- Usages
- 1 Coat
- Usages
- Graffiti Resistance
- Product Usage Type
- Topcoat
- Product Range
- PSX
- Colour Family
- Anthracite Grey
- Colour Family
- Grey
- Colour Family
- Green
- Colour Family
- Blue
- Colour Family
- Red
- Colour Family
- Brown
- Colour Family
- Pink
- Colour Family
- Orange
- Colour Family
- Purple
- Colour Family
- Yellow
- Colour Family
- Black
- Colour Family
- White
- Colour Family
- Neutral
- Non - Isocyanate
- Isocyanate Free/Non-Isocyanate
- Product Type
- Siloxane
- Environment
- Atmospheric
- Touch Dry/Dust Free (@ 20-25°C)
- 3 hours
- Product Attributes
- 1 coat
- Product Attributes
- High Solids
- Product Attributes
- Gloss Retention
- Product Attributes
- Colour Retention
- Product Attributes
- Isocyanate Free
- Resistance to
- Chemicals
- Resistance to
- Graffiti
Questions
Question about the product
Be the first to ask a question about this product!
IMPORTANT SHIPPING & DELIVERY INFORMATION
PPG PSX 700 is only available with the shipping and delivery timescales listed below - please do not contact our Customer Support Team with enquiries about alternative or earlier shipping and delivery times.
Saturdays and Sundays, as well as Bank Holidays, are not classed as working days.
Orders placed after the cut-off for this product will not be processed for earliest dispatch until 9am the next working day.
All delivery costs below are excluding VAT

PPG Thinner 21-06
This thinner has been developed by PPG Protective and Marine Coatings for use with selected paint products.
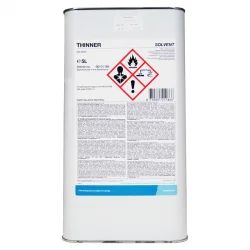
PPG Thinner 60-12
We no longer stock this product; please contact our technical team on 0113 2455450 (option 2) or send a message to [email protected] where we will be happy to find an alternative product. This thinner has been developed by PPG Protective and Marine Coatings for use with selected paint products. More Information Delivery Info

Surface Preparation Kits for Steel
These surface preparation kits for steel have been created to help provide customers with an easily accessible bundle of tools to aid in the preparation of steel surfaces in accordance with ISO 8501-1 (St2/3) and SSPC (SP 2/3). Please click here for important information about these kits. Kit Contents: SET 1 (Hand Tools) 1 x Rust-Oleum...