- There are no more items in your cart
- Shipping Calculated at checkout
-
Sub-Total (inc. VAT)
£0.00
PPG SigmaCover 256 is a two component, high-build, polyamide-cured recoatable zinc phosphate epoxy primer.
- General-purpose epoxy primer or buildcoat in protective coating systems, for steel and concrete structures in atmospheric exposure.
- Suitable for atmospheric industrial and marine applications.
- Can be recoated with various two-component and conventional coatings, even after long weathering periods.
- Excellent rust preventing properties in industrial or coastal atmospheres
- Tough, with long-term flexibility
- Cures even at temperatures down to -10°C (14°F
- Good adhesion to steel, galvanized steel and aged epoxy coatings
- Easy application, both by airless spray and brush
- Can be used as epoxy primer/finish (for dry internal areas)
PPG SigmaCover 256 is a two-component, high-build, polyamide-cured recoatable zinc phosphate epoxy primer.
Click To Jump To Section:
- Features & Benefits
- Product Specification
- Film Thickness Range
- Drying Times
- Surface Preparation
- Application Methods
- Product Notes
- Health & Safety
Features & Benefits
- General-purpose epoxy primer or buildcoat in protective coating systems, for steel and concrete structures in atmospheric exposure.
- Suitable for atmospheric industrial and marine applications.
- Can be recoated with various two-component and conventional coatings, even after long weathering periods.
- Excellent rust preventing properties in industrial or coastal atmospheres
- Tough, with long-term flexibility
- Cures even at temperatures down to -10°C (14°F
- Good adhesion to steel, galvanized steel and aged epoxy coatings
- Easy application, both by airless spray and brush
- Can be used as epoxy primer/finish (for dry internal areas)
- Click to jump down to Technical Data
Product Specification
Technical Data | ||||||
---|---|---|---|---|---|---|
PPG SigmaCover 256 | ||||||
Number of Components: | Two | |||||
Mass Density: | 1.4 kg/l (11.7 lb/US gal) | |||||
Volume Solids: | 63 ± 2% | |||||
VOC (supplied): | Directive 1999/13/EC, SED: max. 245.0 g/kg | |||||
UK PG 6/23(92) Appendix 3: max. 338.0 g/l (approx. 2.8 lb/US gal) | ||||||
Recommended Dry Film Thickness: | 75 - 150 μm (3.0 - 6.0 mils) depending on system | |||||
Theoretical Spreading Rate: | 6.3 m²/l for 100 μm (253 ft²/US gal for 4.0 mils) | |||||
Shelf Life: | Base: at least 24 months when stored cool and dry | |||||
Hardener: at least 24 months when stored cool and dry |
Film Thickness Range
Spreading Rate & Film Thickness | |||
---|---|---|---|
DFT | Theoretical Spreading Rate | ||
75 μm (3.0 mils) | 8.4 m²/l (337 ft²/US gal) | ||
100 μm (4.0 mils) | 6.3 m²/l (253 ft²/US gal) | ||
150 μm (6.0 mils) | 4.2 m²/l (168 ft²/US gal) |
Drying Times
Curing time for DFT up to 100μm (4.0mils) | |||
---|---|---|---|
Substrate temperature | Dry To Handle | Fully Cured | |
-10°C (14°F) | 24 hours - 48 hours | 20 days | |
-5°C (23°F) | 24 hours - 30 hours | 14 days | |
0°C (32°F) | 18 hours - 24 hours | 10 days | |
5°C (41°F) | 18 hours | 8 days | |
10°C (50°F)) | 12 hours | 6 days | |
15°C (59°F) | 8 hours | 5 days | |
20°C (68°F) | 6 hours | 4 days | |
30°C (86°F) | 4 hours | 3 days | |
40°C (104°F) | 3 hours | 48 hours |
Notes:
- Adequate ventilation must be maintained during application and curing.
Pot Life (at application viscosity) | |
---|---|
Mixed Product Temperature | Pot Life |
10°C (50°F) | 16 hours |
15°C (59°F) | 10 hours |
20°C (68°F) | 8 hours |
30°C (86°F) | 5 hours |
35°C (95°F) | 4 hours |
Overcoating interval for DFT up to 150μm (6.0mils) | |||||||
---|---|---|---|---|---|---|---|
Overcoating with: | Interval: | -5°C (23°F) | 5°C (41°F) | 10°C (50°F) | 20°C 68°F) | 30°C (86°F) | 40°C (104°F) |
SIGMADUR 520, SIGMADUR 550, various chlorinated rubbers, vinyls, acrylates and alkyd paints. | |||||||
Minimum | 3 days | 24 hours | 16 hours | 8 hours | 5 hours | 3 hours | |
Maximum | Unlimited | Unlimited | Unlimited | Unlimited | Unlimited | Unlimited |
Notes:
- - Maximum interval is only unlimited when the surface is free from any contamination
- - SIGMACOVER 256 should not be overcoated with coal tar epoxy coatings
Surface Preparation
Substrate Conditions
- Steel; blast cleaned to ISO-Sa2½, blasting profile 40 – 70 μm (1.6 – 2.8 mils)
- Shop primed steel; pretreated to SPSS-Pt3 / SSPC-SP3
- Galvanized steel must be sweep blasted until an even flat appearance (only for internal dry exposure conditions)
- Aged suitable coating must be dry and free from any contamination
Substrate Temperature
- Substrate temperature during application and curing down to -10°C (14°F) is acceptable; provided the substrate is free from ice and dry
- Substrate temperature during application should be at least 3°C (5°F) above dew point
- Relative humidity during application and curing should not exceed 95%
Application Methods
Mixing Ratio By Volume: Base To Hardener 82:18
- The temperature of the mixed base and hardener should preferably be above 15°C (59°F), otherwise extra thinner may be required to obtain application viscosity
- Adding too much thinner results in reduced sag resistance and slower cure
- Thinner should be added after mixing the components
Pot Life:
- 8 hours at 20°C (68°F)
Air Spray:
- Recommended Thinner: THINNER 91-92
- Volume Of Thinner: 10 - 15%, depending on required thickness and application conditions
- Nozzle Orifice: 1.5 – 3.0 mm (approx. 0.060 – 0.110 in)
- Nozzle Pressure: 0.3 - 0.4 MPa (approx. 3 - 4 bar; 44 - 58 p.s.i.)
Airless Spray:
- Recommended Thinner: THINNER 91-92
- Volume Of Thinner: 5 - 10%, depending on required thickness and application conditions
- Nozzle Orifice: Approx. 0.48 mm (0.019 in)
- Nozzle Pressure: 15.0 MPa (approx. 150 bar; 2176 p.s.i.)
Brush/Roller:
- Thinner: THINNER 91-92
- Volume Of Thinner: 0 – 5%
Product Notes
Information On Basic Physical And Chemical Properties | ||||||
---|---|---|---|---|---|---|
PPG SigmaCover 256 Base | PPG SigmaCover 256 Hardener | |||||
Form: | Liquid | Liquid | ||||
Colour: | Various | Not available | ||||
Odour: | Aromatic | Amine-like | ||||
Odour Threshold: | Not available | Not available | ||||
pH-value 20°C: | Insoluble in water. | Insoluble in water. | ||||
Melting point/freezing point: | May start to solidify at the following temperature: <-7°C (<19.4°F) This is based on data for the following ingredient: 4-nonylphenol, branched. Weighted average: -90.56°C (-131°F) | May start to solidify at the following temperature: 12°C (53.6°F) This is based on data for the following ingredient: 3,6-diazaoctanethylenediamin. Weighted average: -84.56°C (-120.2°F) | ||||
Initial boiling point and boiling range: | >37.78°C | >37.78°C | ||||
Flash Point: | Closed cup: 34°C | Closed cup: 25°C | ||||
Evaporation Rate: | Highest known value: 0.84 (ethylbenzene) Weighted average: 0.77compared with butyl acetate | Highest known value: 0.84 (ethylbenzene) Weighted average: 0.71compared with butyl acetate | ||||
Flammability (solid, gas): | liquid | liquid | ||||
Upper/lower flammability or : explosive limits: | Greatest known range: Lower: 1.48% Upper: 13.74% (1-methoxy-2-propanol)) | Greatest known range: Lower: 1.7% Upper: 10.9% (2-methylpropan-1-ol) | ||||
Vapour pressure: | Highest known value: <1.6 kPa (<12 mm Hg) (at 20°C) (2-methylpropan-1-ol). Weighted average: 1.02 kPa (7.65 mm Hg) (at 20°C) | Highest known value: <1.6 kPa (<12 mm Hg) (at 20°C) (2-methylpropan-1-ol). Weighted average: 0.8 kPa (6 mm Hg) (at 20°C) | ||||
Vapour Density: | Highest known value: 7.59 (Air = 1) (4-nonylphenol, branched). Weighted average: 3.74 (Air = 1) | Highest known value: 5.04 (Air = 1) (3,6-diazaoctanethylenediamin). Weighted average: 3.17 (Air = 1) | ||||
Relative density: | 1.48 | 0.95 | ||||
Solubility(ies): | Insoluble in the following materials: cold water | Insoluble in the following materials: cold water | ||||
Partition coefficient: n-octanol/ water: | Not applicable | Not applicable | ||||
Auto-ignition temperature: | 290°C | Flash point 430°C | ||||
Decomposition temperature: | Stable under recommended storage and handling conditions | Stable under recommended storage and handling conditions | ||||
Viscosity: | Kinematic (40°C): >0.21 cm² /s: 60 - 100 s (ISO 6mm) | Kinematic (room temperature): >4 cm² /s: Kinematic (40°C): >0.21 cm² /s | ||||
Explosive properties: | The product itself is not explosive, but the formation of an explosible mixture of vapour or dust with air is possible. | The product itself is not explosive, but the formation of an explosible mixture of vapour or dust with air is possible. | ||||
Oxidising properties: | Product does not present an oxidizing hazard | Product does not present an oxidizing hazard |
Health & Safety
- This is a solvent-borne paint and care should be taken to avoid inhalation of spray mist or vapor, as well as contact between the wet paint and exposed skin or eyes.
- For further information please see the safety data sheets in the attachments section above.
Data sheet
- Manufacturer
- PPG
- For Use By
- Professional Use
- For Use On
- Steel, Concrete, Galvanized Steel,
- Application Method
- Spray, Airless Spray, Brush, Roller
- Sheen
- Eggshell
- Colour
- Standard / Ready Mixed
- Single, Two or Three Pack
- Two-Pack
- Pack Size
- 4L, 20L
- Mixing Ratio
- Base To Hardener 82:18
- Dry to Handle (at 20°C)
- 6 hours
- Fully Cured (at 20°C)
- 4 days
- Pot Life (at 20°C)
- 8 hours
- Coverage
- 6.3 m²/l for 100 μm (253 ft²/US gal for 4.0 mils)
- Recommended Thinner/Cleaner
- THINNER 91-92
- Min. Application Temperature
- (-10°C)
- Density
- 1.4 kg/l (11.7 lb/US gal)
- Solids by Volume
- 63 ± 2%
- VOC
- Directive 1999/13/EC, SED: max. 245.0 g/kg - UK PG 6/23(92) Appendix 3: max. 338.0 g/l (approx. 2.8 lb/US gal)
- Shelf Life (from date of manufacture)
- Base: at least 24 months when stored cool and dry Hardener: at least 24 months when stored cool and dry
- Recommended Dry Film Thickness
- 75 - 150 μm (3.0 - 6.0 mils) depending on system
- UN Number
- UN1263
- Dry to Handle (at 10°C)
- 12 hours
- Pot Life (at 10°C)
- 16 hours
- Fully Cured (at 10°C)
- 6 days
- Pot Life
- 15°C (59°F) - 10 hours
- Pot Life
- 30°C (86°F) - 5 hours
- Pot Life
- 35°C (95°F) - 4 hours
- Base Type
- Solvent-Based
- Base Type
- Epoxy
- Suitable For Use On
- Concrete
- Suitable For Use On
- Steel
- Suitable For Use On
- Galvanised Steel
- Suitable For Use On
- Compatible Existing Coatings
- Finish
- Eggshell
- Application Method
- Spray
- Application Method
- Brush
- Application Method
- Roller
- Usages
- High Build
- Usages
- Flexible
- Usages
- Low Temperature
- Usages
- Atmospheric
- Usages
- Anti-Corrosive
- Usages
- Zinc Phosphate
- Product Usage Type
- Primer
- Product Range
- SigmaCover
- Colour Family
- Cream
- Colour Family
- Red
- Dry to Recoat (@ 20-25°C)
- 3 hours
- Categorised As
- Metal Paints > Low Temperature Primers
- Seasonal
- Cold Weather
Questions
Question about the product
Be the first to ask a question about this product!
IMPORTANT SHIPPING & DELIVERY INFORMATION
PPG SigmaCover 256 is only available with the shipping and delivery timescales listed below - please do not contact our Customer Support Team with enquiries about alternative or earlier shipping and delivery times.
Saturdays and Sundays, as well as Bank Holidays, are not classed as working days.
Orders placed after the cut-off for this product will not be processed for earliest dispatch until 9am the next working day.
All delivery costs below are excluding VAT

PPG SigmaDur 520
PPG SigmaDur 520, a two-component, high-build semi-gloss aliphatic acrylic polyurethane finish that can be recoated an unlimited amount, with excellent resistance to atmospheric exposure conditions. Available in 2,300+ colours, inc. RAL, BS, NCS & the new NCS 2050 colours Easy application by roller and airless spray - Can be recoated...
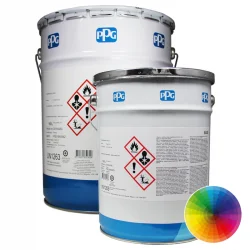
PPG SigmaDur 550 H
PPG Sigmadur 550 H (formerly known as Sigmadur 568) is a two-component, high solids, high-build aliphatic acrylic polyurethane finish with excellent resistance to atmospheric exposure conditions with good colour and gloss retention, resisting splash of mineral and vegetable oils, paraffins, aliphatic petroleum products and mild chemicals....

Surface Preparation Kits for Steel
These surface preparation kits for steel have been created to help provide customers with an easily accessible bundle of tools to aid in the preparation of steel surfaces in accordance with ISO 8501-1 (St2/3) and SSPC (SP 2/3). Please click here for important information about these kits. Kit Contents: SET 1 (Hand Tools) 1 x Rust-Oleum...