- There are no more items in your cart
- Shipping Calculated at checkout
-
Sub-Total (inc. VAT)
£0.00
Sherwin-Williams Envirolastic 2500 is a single coat, two-pack direct to metal polyaspartic primer/finish or a topcoat over approved primers.
- Long-term corrosion protection
- Independently certified to ISO12944:2018 Part 6 C3, C4 and C5 (Regime 2)
- Coating system design life up to 25 years or over
- Excellent gloss and colour retention
- Excellent aesthetic finish and UV protection
- Ideal for application to large steel structures and OEMs such as cranes, dockyard equipment, machinery & conveyer systems
- Externally pre-qualified in accordance with BS EN ISO12944- 6:2018 for use in C3, C4 & C5 environments
- Suitable for airless spray, air-assisted airless, plural component airless spray, conventional, electrostatic spray, brush and roller
- Manufacturing capacity increase - elimination of bottle-necks in painting
- Total production cost reduction - Energy cost saving – negates the need for “force curing” at high temperatures
- Please note this product is made to order with a lead time of 7-14 working days
Professional use only - from the 24th August 2023, adequate training is required before industrial or professional use of this product.
Should you require training, visit - https://www.safeusediisocyanates.eu/
Product customisation
Don't forget to save your customization to be able to add to cartProfessional use only - from the 24th August 2023, adequate training is required before industrial or professional use of this product.
Should you require training, visit - https://www.safeusediisocyanates.eu/
Sherwin-Williams Envirolastic 2500 is a single coat, two-pack direct to metal polyaspartic primer/finish or a topcoat over approved primers. It is a fast dry polyaspartic technology formulated to provide anti-corrosion, resistance to mechanical damage, gloss & colour retention and low VOC.
The advanced combination of Envirolastic 2500 product characteristics is designed to take your performance and productivity to the next level:
- Total production cost savings
- Third-party accredited performance to the latest ISO 12944:2018
- Excellent aesthetic finish and UV protection
Quick Links - Click To Jump To Section:
- Features & Benefits
- Recommended Uses
- Key Applications
- Polyaspartic Technology - How It Benefits The Industry
- Product Characteristics
- Typical Systems
- Surface Preparation
- Application Conditions
- Application Equipment
Features & Benefits
- Single coat
- Direct to metal
- Polyaspartic primer/finish or a topcoat over approved primers
- Fast dry polyaspartic technology formulated to provide anti-corrosion, resistance to mechanical damage, gloss & colour retention
- Low VOC
- Suitable for use in a range of markets where durable performance and aesthetics are needed
- Key market segments include infrastructure, stadiums, oil & gas, mining & minerals and power
- Ideal for application to large steel structures and OEMs such as cranes, dockyard equipment, machinery & conveyer systems
- Externally pre-qualified in accordance with BS EN ISO12944-6:2018 for use in C3, C4 & C5 environments
- Suitable for airless spray, air-assisted airless, plural component airless spray, conventional, electrostatic spray, brush and roller
Recommended Uses
Suitable for use in a range of markets where durable performance and aesthetics are needed.
Key market segments include infrastructure, stadiums, oil & gas, mining & minerals and power.
Ideal for application to large steel structures and OEMs such as cranes, dockyard equipment, machinery & conveyer systems.
Externally pre-qualified in accordance with BS EN ISO12944- 6:2018 for use in C3, C4 & C5 environments.
Suitable for airless spray, air-assisted airless, plural component airless spray, conventional, electrostatic spray, brush and roller.
Key Applications
Infrastructure
- Bridges
- Cranes
- Commercial buildings
- Manufacturing plants
- Sporting arenas
- Transportation hubs
- Warehouses
Energy
- Biomass plants
- Waste-to-energy
- Thermal power plants
- Conveyor belts
- Piping and valves
- Pumps
Oil and Gas
- Bullet and storage tanks
- Cylinders and separators
- Piping and valves
- Process vessels
- Production tanks
Mining
- Process vessels
- Conveyor belts
- Screeners and crushers
- Excavators
- Pumps
- Thickeners and clarifiers
Polyaspartic Technology - How It Benefits The Industry
Industrial and civil construction projects are becoming more demanding in terms of quality, durability, sustainability and aesthetics of products. This, for most structural steel fabrication shops and manufacturing plants, means that cost pressure is rising - while product delivery cycles are becoming faster and faster. Therefore productivity and efficiency - as factors of time and cost – play a paramount role in securing contracts and delivering product packages in time.
For more than 15 years Sherwin-Williams have been developing polyaspartic technology and using the unique benefits in a range of applications to help speed up the production process. The adoption rate to this technology platform continues to increase as it benefits contractors in high-performance steel protection systems to fast return to service floor coatings.
Proven Protection
This next-generation technology continues to add value across the supply chain in the following ways:
Productivity improvement
- Dry film thickness up to 225 microns in one layer with no outgassing
- C3 – One-layer “direct-to-metal” application
- C4/C5 - Two-layer application over approved primers
Manufacturing capacity increase
- Elimination of bottle-necks in painting
- Time to handle 2 hours at 20°C, 50% RH
- Application of C3, C4 and C5 coating systems in 8-hour single shift
Application cost reduction
- C3 – up to 50% cost/m 2 decrease against two-layer systems
- C4/C5 – up to 40% cost/m 2 decrease against three-layer systems
Total production cost reduction
- C3 – up to 25% cost/m 2 decrease against two-layer systems
- C4/C5 – up to 15% cost/m 2 decrease against three-layer systems
- Energy cost saving – negates the need for “force curing” at high temperatures
Environmental improvement
- Low carbon emissions – negates the need to run infrared, electric or gas ovens
- Low VOC emissions – VOC at 190 g/l (EPA Method 24) or 193 g/kg (EC SED)
Long-term corrosion protection
- Independently certified to ISO12944:2018 Part 6 C3, C4 and C5 (Regime 2)
- Coating system design life up to 25 years or over
- Excellent gloss and colour retention
Product Characteristics
Data | |
---|---|
Flash Point: | 27°C (80°F), mixed (Seta Flash) |
Volume Solids: | 78% ± 2%, mixed, may vary by colour |
VOC (EPA Method 24): | 190 g/lt; 2.21 lb/gal, mixed, may vary by colour |
193gms/kilo by weight to satisfy EC Solvent Emissions Directive | |
Cleanser/Thinner: | No 15 (for thinning) |
No 9 (for cleaning) | |
Pack Size: | 15 litre unit when mixed |
Mix Ratio: | 2:1 by volume |
Weight: | 1.7kg/ltr (may vary with shade) |
Shelf Life: | 6 months, unopened - Store indoors at 4.5°C (40°F) to 38°C (100°F). |
Recommended Spreading Rate per coat :
Minimum | Maximum | |
---|---|---|
Wet microns (mils) | 130 (5.0) | 300 (12.0) |
Dry microns (mils) | 100 (4.0) | 225 (9.0) |
~Coverage m 2 /L (sq ft/gal) | 7.8 (312) | 3.5 (139) |
NOTE: Brush or roll application may require multiple coats to achieve maximum film thickness and uniformity of appearance. |
Drying Schedule:
10°C 50%RH |
20°C 50%RH |
30°C 50%RH |
|
---|---|---|---|
To Touch: | 60 minutes | 30 minutes | 15 minutes |
To Handle: | 3 hours | 2 hours | 60 minutes |
To Recoat: | 2 hours | 60 minutes | 30 minutes |
Pot Life: | 60 - 75 minutes | ||
The maximum recoat time with itself is 24 hours, if exceeded, abrade surface before recoating. Drying time is temperature, humidity and film thickness dependent. |
Typical Systems
Product | Dry Film Thickness / ct. | |
---|---|---|
Microns | (Mils) | |
1 ct. ENVIROLASTIC 2500 | 120 | (5) |
C2H and C3M / BS EN ISO12944-6:2018 | ||
1 ct. ENVIROLASTIC 2500 | 180 | (7) |
C2VH, C3H, C4M and C5L / BS EN ISO12944-6:2018 | ||
1 ct. Macropoxy 400 | 140 | (6) |
1 ct. Envirolastic 2500 | 100 | (4) |
C4H. BS EN ISO12944-6:2018 | ||
1 ct. Macropoxy 400 | 175 | (7) |
1 ct. Envirolastic 2500 | 125 | (5) |
C4VH, C5H / BS EN ISO12944-6:2018 | ||
1 ct. | 125 | (5) |
1 ct. ENVIROLASTIC 2500 | 175 | (7) |
C4VH, C5H / BS EN ISO12944-6:2018 | ||
1 ct. Zinc Clad IV EU | 60 | (3) |
1 ct. ENVIROLASTIC 2500 | 200 | (8) |
C4VH, C5H / BS EN ISO12944-6:2018 |
For compatability and use with other primers please contact 0113 2455450 (option 2) or send a message to [email protected].
Surface Preparation
Surface must be clean, dry, and in sound condition. Remove all oil, dust, grease, dirt, loose rust, and other foreign material to ensure adequate adhesion.
Refer to the Application Guide for detailed surface preparation information.
The systems listed above are representative of the product's use and other systems may be appropriate.
Minimum recommended surface preparation:
Iron & Steel:
- Sa2.5, (BS EN ISO8501-2007)
- 50-75 microns
- (2-3 mil) profile
Galvanizing:
- SSPC-SP16
- 50 micron
- (2 mil) profile
Surface Preparation Standards | |||||
---|---|---|---|---|---|
Condition of Surface | BS EN ISO8501-1:2007 | Swedish Std.SIS055900 | SSPC | NACE | |
White Metal | Sa 3 | Sa 3 | SP 5 | 1 | |
Near White Metal | Sa 2.5 | Sa 2.5 | SP 10 | 2 | |
Commercial Blast | Sa 2 | Sa 2 | SP 6 | 3 | |
Brush-Off Blast | Sa 1 | Sa 1 | SP7 | 4 | |
Hand Tool Cleaning | Rusted | C St 2 | C St 2 | SP2 | - |
Pitted & Rusted | D St 2 | D St 2 | SP2 | - | |
Power Tool Cleaning | Rusted | C St 3 | C St 3 | SP3 | - |
Pitted & Rusted | D St 3 | D St 3 | SP3 | - |
Approved Primers
Envirolastic 2500 is a fast cure technology that is designed to provide rapid return to service, as a result it is not compatible with all primers. The following primers are currently approved for use:
The maximum overcoating interval on the approved list of primers is 28 days at all temperatures. If this is exceeded, it is recommended that the primer surface is abraded and cleaned down primer to overcoating with Envirolastic 2500.
Application Conditions
Temperature:
- 5°C (41°F) minimum
- 49°C (120°F) maximum (air, surface, and material)
- At least 3°C above dew point
Minimum Paint temperature 5°C for application.
Maximum paint temperature 35°C for application.
Maximum Relative Humidity 85%.
Minimum Relative Humidity 35%.
Maximum air and surface temperature 50°C.
Clean application equipment thoroughly before and after use. Mixed coating is sensitive to water, use water traps in all air lines.
Moisture contact can reduce pot life and affect gloss and colour.
Thoroughly mix both components before using or dry time, gloss and colour will be affected.
- Relative humidity: 85% maximum
Refer to the Application Guide for detailed application information.
Application Equipment
Airless Spray:
- Air Pressure Bars: 80 - 100
- Tip: 008" - .014"
Air Assised Airless Spray:
- Air Pressure Bars: 2 - 4
- Fluid Pressure Bars: 40 - 160
- Tip: 011" - .015"
Conventional Spray:
- Air Pressure Bars: 2 - 4
- Fluid Pressure Bars: 0 - 1,5
- Tip: 1.0 - 1.5mm
Data sheet
- Manufacturer
- Sherwin-Williams
- For Use By
- Industrial Use
- Interior / Exterior Use
- Exterior Use
- Water / Solvent Based
- Solvent
- For Use On
- Steel, Iron, Galvanising
- Application Method
- airless spray, air-assisted airless, plural component airless spray, conventional, electrostatic spray, brush, roller
- Sheen
- Gloss
- Colour
- Fully Tintable
- Single, Two or Three Pack
- Two-Pack
- Pack Size
- 15L
- Mixing Ratio
- 2:1 by volume
- Touch Dry (at 20°C)
- 30 Mins
- Dry to Handle (at 20°C)
- 2 hours
- Dry to Recoat (at 20°C)
- 60 minutes
- Coverage
- Min 7.8 m2L - Max 3.5 m2L
- Max. Application Temperature
- 49°C
- Min. Application Temperature
- 5°C
- Solids by Volume
- 78% ± 2%, mixed, may vary by colour
- VOC
- 190 g/lt; 2.21 lb/gal, mixed, may vary by colour
- Shelf Life (from date of manufacture)
- 6 months, unopened - Store indoors at 4.5°C to 38°C
- Recommended Dry Film Thickness
- Min 100 - Max 225
- Recommended Wet Film Thickness
- Min 130 - Max 300
- UN Number
- UN1263
- Pot Life (at 10°C)
- 60 - 75 minutes
- Base Type
- Solvent-Based
- Suitable For Use On
- Steel
- Suitable For Use On
- Galvanised Steel
- Suitable For Use On
- Iron
- Suitable For Use On
- Galvanising
- Suitable For Use On
- Primed Surfaces
- Finish
- Gloss
- Application Method
- Spray
- Usages
- Low VOC
- Usages
- Atmospheric
- Usages
- Anti-Corrosive
- Usages
- Gloss Retention
- Usages
- Colour Retention
- Usages
- Primer/Finish
- Usages
- 1 Coat
- Usages
- Exterior Durability
- Usages
- Direct to Metal
- Product Usage Type
- Primer & Topcoat
- Product Range
- Envirolastic
- Colour Family
- Magnolia
- Colour Family
- White
- Colour Family
- Neutral
- Colour Family
- Anthracite Grey
- Colour Family
- Violet
- Colour Family
- Cream
- Colour Family
- Beige
- Colour Family
- Grey
- Colour Family
- Green
- Colour Family
- Blue
- Colour Family
- Red
- Colour Family
- Brown
- Colour Family
- Pink
- Colour Family
- Orange
- Colour Family
- Purple
- Colour Family
- Yellow
- Colour Family
- Off-White
- Colour Family
- Black
- Product Type
- Polyaspartic
- Environment
- Atmospheric
- Environment
- Exterior Durability
- Touch Dry/Dust Free (@ 20-25°C)
- 30 mins
- Product Attributes
- 1 coat
- Product Attributes
- Anti-Corrosive
- Product Attributes
- Primer/Finish
- Product Attributes
- Gloss Retention
- Product Attributes
- Colour Retention
- Product Attributes
- Low VOC
Questions
Question about the product
Be the first to ask a question about this product!
IMPORTANT SHIPPING & DELIVERY INFORMATION
Sherwin-Williams Envirolastic 2500 is only available with the shipping and delivery timescales listed below - please do not contact our Customer Support Team with enquiries about alternative or earlier shipping and delivery times.
Saturdays and Sundays, as well as Bank Holidays, are not classed as working days.
Orders placed after the cut-off for this product will not be processed for earliest dispatch until 9am the next working day.
All delivery costs below are excluding VAT
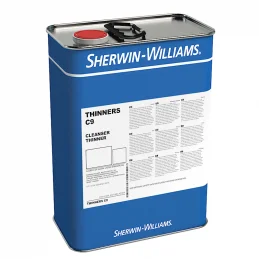
Sherwin-Williams Cleanser/Thinner No.9
Sherwin-Williams Cleanser/Thinner No.9 is a specially formulated blend of solvents designed to mix with its compatible Sherwin-Williams products to create an optimal consistency for application whether it be for Brush, Roller or Spray. It can also be used for cleaning of surfaces and application equipment.

Sherwin-Williams Cleanser/Thinner No.15
Sherwin-Williams Cleanser/Thinner No.15 is a specially formulated blend of solvents designed to mix with its compatible Sherwin-Williams products to create an optimal consistency for application whether it be for Brush, Roller or Spray. It can also be used for cleaning of surfaces and application equipment.
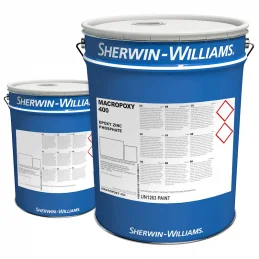
Sherwin-Williams Macropoxy 400
Formerly known as Sherwin-Williams Macropoxy C400V3, a multi-functional epoxy zinc phosphate coating suitable for the protection of steelwork in a range of exposure environments from C1 to C5. It was recently used on The Shard (London) for corrosion protection. Recommended uses include: Buildings, car parks Petrochemical plants, breweries,...

Sherwin Williams Zinc Clad IV EU
Sherwin Williams Zinc Clad IV EU (formerly known as Zinc Clad M501), is 2-pack epoxy zinc rich anti-corrosive primer for anti-corrosive protection of steel surfaces prepared by abrasive blast cleaning, and may be used as a repair primer for galvanized surfaces. Meets the performance requirements of ISO20340 (2009) as part of a three coat...

Surface Preparation Kits for Steel
These surface preparation kits for steel have been created to help provide customers with an easily accessible bundle of tools to aid in the preparation of steel surfaces in accordance with ISO 8501-1 (St2/3) and SSPC (SP 2/3). Please click here for important information about these kits. Kit Contents: SET 1 (Hand Tools) 1 x Rust-Oleum...