- There are no more items in your cart
- Shipping Calculated at checkout
-
Sub-Total (inc. VAT)
£0.00
Need Help?
Surface Tolerant Primers
Surface Tolerant Primers for metal offer exceptional performance in challenging environments where surface preparation is limited. Designed to adhere to minimally cleaned, rusted, or weathered surfaces, these primers provide robust corrosion protection and long-lasting durability. They are ideal for use on steel and other metal substrates in industries like marine, oil & gas, and construction. Surface tolerant primers are commonly used in environments where traditional primers fail to adhere due to poor surface conditions, making them essential for ensuring the longevity and integrity of metal structures and equipment.
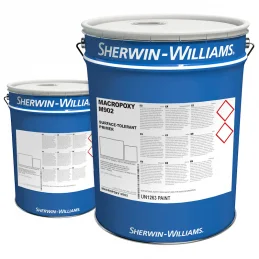
Sherwin-Williams Macropoxy M902
Sherwin-Williams Macropoxy M902 (formerly known as Epigrip M902) is a low temperature curing hi-build 2-pack epoxy brushing aluminium primer coating capable of curing down to 0°C. For brush application onto hand or mechanically prepared surfaces and/or damp gingered surfaces giving excellent wetting and adhesion characteristics - see...

Carboline Carbomastic 15 LT
Carboline Carbomastic 15 LT is a two-component, high build coating with excellent adhesion to rusted steel and most aged coatings. Surface tolerant Recommended for painting over rusted steel where hand cleaning only is possible Carbomastic 15 LT penetrates through rust to steel substrate and stops further corrosion and undercutting...
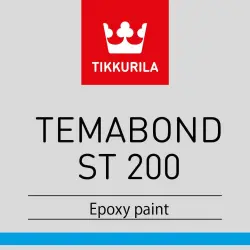
Tikkurila Temabond ST 200
2 component high-solids, aluminium pigmented modified epoxy maintenance paint for demanding surfaces such as steel structures, railway vehicles, and infastructure in energy and telecommunications. Surface-tolerant high-solids epoxy paint. Very good adhesion even to hand-prepared steel. Lower VOC emissions than conventional epoxy paints....
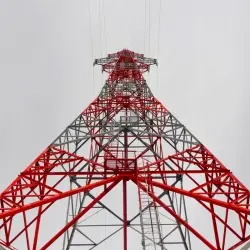
International Interplus 256
International Interplus 256 is a low VOC, two component internally flexibilised high build surface tolerant epoxy primer. It is pigmented with aluminium and lamellar micaceous iron oxide for improved corrosion resistance and represents the second generation in surface tolerant technology.

Sherwin-Williams Macropoxy L425
Sherwin-Williams Macropoxy L425 is a two-pack epoxy zinc phosphate primer to use as anti-corrosive protection of carbon steel surfaces prepared by abrasive blast cleaning. Recommended Systems Macropoxy Dura-plate Zinc Clad Epoxy Primers Zinc Clad Epoxy Buildcoats

International Interplus 770
International Interplus 770 is a low VOC, two component, high solids, internally flexibilised, surface tolerant epoxy primer/intermediate coating intended for use as a versatile, high performance maintenance coating to upgrade tightly adhering existing coatings to longer life durable systems. 4,800+ colours, inc. RAL, RAL Design &...

Rust-Oleum 9169 Epoxy Rust Primer
Available in Red Oxide. Three-component epoxy rust primer. For use on rusted steel surfaces. High adhesion and corrosion protection. Penetrates rust and inhibits further rusting. Professional use only.

PPG SigmaCover 690
PPG SigmaCover 690 is a two-component high solids aluminium pigmented polyamine cured modified epoxy primer/coating designed for maintenance. SigmaCover 690 is a self-priming coating, tolerant to lower grades of steel preparation, and is compatible with most aged, good adhering coatings. It can be recoated with epoxy and polyurethane paints,...

Carboline Rustbond NG FC
Carboline Rustbond NG FC is a cross-linked penetrating primer/sealer with good wetting properties. It is highly flexible and accepts a variety of topcoats. Recommended use as primer/sealers for marginally prepared steel and over old coatings. Its excellent wetting properties allows it to penetrate rust and discontinuities in existing coatings...

Tor Epoxy Surface Tolerant Primer
Tor Epoxy Surface Tolerant Primer, a high performance two pack epoxy primer for manually cleaned steel, particularly of interest in “safety” areas where “blast cleaning” is not allowed. Epoxy/Polyamide binder with anti corrosive and inorganic pigments and thinned with Aromatic Hydrocarbon and Alcohol solvents. Two-pack Brush or spray...

Axalta Bondon 115 Aluminium Primer
Axalta Bondon 115 Aluminium Primer is a surface tolerant two pack epoxy aluminium primer, used as a primer on hand prepared rusty steel and to upgrade sound existing coatings. Use as a rust inhibiting primer on hand prepared steel, or as a high build patch repair primer under most generic coating types Approved to UK Network Rail...
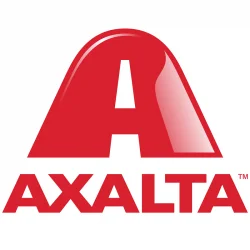
Axalta Bondon 116 Epoxy Primer & Undercoat
Axalta Bondon 116 Epoxy Primer & Undercoat is a high solids two pack epoxy intermediate or finish, designed for application over Axalta Bondon 115. Approved over Bondon 115 by UK Network Rail Can be used as part of a surface tolerant epoxy system which can upgrade sound old conventional coatings to a high performance epoxy/polyurethane...
Need Help?
Need Help?
Surface Tolerant Primers are a specialised category of primers designed to perform exceptionally well on metal surfaces that are not in ideal condition for painting. These primers have been formulated to adhere to surfaces that are rusty, weathered, or only minimally cleaned. In industries where surface preparation is often constrained by environmental conditions or budgetary restrictions, surface tolerant primers stand as a vital solution for ensuring durability and corrosion resistance.
The key advantage of using surface tolerant primers lies in their ability to bond effectively with compromised surfaces. Unlike standard primers that require near-perfect preparation for optimal performance, surface tolerant primers are engineered to deliver excellent adhesion and protection on metal substrates even when abrasive blasting or thorough cleaning cannot be achieved. This makes them indispensable in sectors where time, cost, and access to advanced cleaning techniques are limited but high performance and longevity are essential.
These primers are especially useful in industries such as construction, marine, oil and gas, and industrial maintenance. In environments where steel and other metals are exposed to harsh weather, moisture, and chemical exposure, surface tolerant primers provide a durable shield that prolongs the life of the structure and helps prevent costly repairs or replacements.
Top Features and Benefits of Surface Tolerant Primers
- Adhesion to Poorly Prepared Surfaces: One of the most defining features of surface tolerant primers is their ability to bond with surfaces that have not undergone extensive preparation. Even on rusted, flaky, or weathered metals, these primers exhibit superior adhesion compared to conventional primers. This allows them to serve as the first line of defence in environments where surface preparation methods, such as sandblasting, are impractical or prohibitively expensive.
- Corrosion Resistance: Metal structures and equipment, especially those exposed to outdoor environments or corrosive industrial conditions, are at risk of rapid degradation without proper protection. Surface tolerant primers provide an effective barrier against moisture, salt, chemicals, and other corrosive elements that can accelerate rusting and compromise the integrity of metal surfaces. With a high level of corrosion resistance, these primers help preserve structural longevity, even in extreme climates or corrosive industrial settings.
- Long-Lasting Durability: Durability is a crucial factor in choosing any protective coating, and surface tolerant primers are formulated to offer long-lasting protection. These primers are typically reinforced with inhibitors and fillers that not only bond to the surface but also withstand mechanical stress, weathering, and chemical exposure over extended periods. This long-term durability is particularly valuable in industries like marine and oil & gas, where frequent repainting is impractical and costly.
- Flexibility in Application: Surface tolerant primers can be applied in a wide range of environmental conditions, including on wet or damp surfaces. This makes them suitable for outdoor use where environmental control is difficult, allowing application in areas prone to moisture or humid conditions. Whether applied via brush, roller, or spray, these primers adapt to a variety of surface textures and weather conditions, ensuring a seamless application process.
- Fast Drying and Overcoating Times: Many surface tolerant primers are designed with fast drying properties, reducing downtime during the application process. Quick drying times mean that a secondary coat, whether it be a topcoat or another protective layer, can be applied more swiftly, which is critical for projects with tight schedules. Faster overcoating times allow industries to minimise the disruption to operations and move more quickly through maintenance or refurbishment phases.
- High Build Properties: The high build nature of surface tolerant primers means they can be applied in thicker coats without sagging or dripping, providing enhanced protection with fewer coats. A thicker primer layer increases resistance to impacts, abrasion, and environmental wear, making these primers an excellent choice for high-traffic areas or surfaces that will be subjected to heavy use or exposure.
- Versatility Across Substrates: While surface tolerant primers are most commonly used on steel, their application is not limited to ferrous metals. They can also be effectively used on other metal substrates, such as aluminium and galvanised steel. This versatility ensures that these primers can cater to a wide range of applications across various industrial sectors, providing uniform protection across different materials.
- Resistance to Extreme Conditions: Designed to endure some of the harshest environments, surface tolerant primers maintain their protective properties under extreme conditions, such as exposure to high levels of humidity, saltwater, and industrial chemicals. In industries like marine and offshore oil rigs, where metal structures are constantly exposed to harsh environmental factors, these primers are invaluable for ensuring long-term protection against corrosion and mechanical wear.
Common Uses of Surface Tolerant Primers
Marine and Offshore Industries
Surface tolerant primers are indispensable in the marine and offshore industries, where steel structures are constantly exposed to the harsh conditions of saltwater, moisture, and extreme weather. Vessels such as ships, barges, and tankers rely on these primers to protect their hulls, decks, and superstructures from the corrosive effects of saltwater. Offshore platforms, including oil rigs and wind farms, also benefit from surface tolerant primers, which provide a protective layer even when the metal has been exposed to harsh weather for extended periods. Surface preparation is often limited to mechanical cleaning in these environments due to logistical challenges, making surface tolerant primers an ideal solution for preventing rust and prolonging the service life of equipment.
In addition to protecting against saltwater corrosion, these primers can withstand the mechanical stresses that occur in marine environments, such as constant movement, impact from waves, and contact with other vessels or equipment. Without the need for extensive surface preparation, workers can apply surface tolerant primers to equipment that remains in operation, reducing downtime and ensuring continuous protection.
Oil and Gas Industry
The oil and gas industry, both onshore and offshore, faces some of the harshest working conditions, with equipment constantly exposed to corrosive chemicals, salt, extreme temperatures, and abrasive materials. Surface tolerant primers are frequently used to coat pipelines, storage tanks, drilling rigs, and refinery equipment, providing long-lasting protection against corrosion. These primers excel in environments where minimal surface preparation is the norm, such as remote drilling sites or offshore platforms where abrasive blasting or high-pressure washing is not feasible.
For example, pipelines running through deserts or arctic regions are subjected to extreme temperature fluctuations, which can cause traditional coatings to crack or fail. Surface tolerant primers offer flexibility and durability, remaining intact even when the substrate expands or contracts. Storage tanks containing corrosive chemicals or petroleum products also benefit from these primers, which resist chemical degradation and form a protective barrier against leaks and rust. Given the financial implications of pipeline or equipment failure, surface tolerant primers play a crucial role in asset protection and longevity in the oil and gas industry.
Industrial Maintenance and Repair
Factories, warehouses, and industrial plants often face a range of challenges when it comes to protecting metal surfaces. Many of these facilities house machinery, conveyor systems, and structural steel that are exposed to varying levels of moisture, chemicals, and wear over time. Surface tolerant primers are a key tool in industrial maintenance, providing the necessary protection for equipment and structures that are difficult to prepare properly for painting.
Industrial plants typically experience wear and tear on machinery and structures from daily operations, leading to corrosion, rust, and surface damage. In many cases, shutting down the plant for extensive cleaning and surface preparation is not an option. Surface tolerant primers allow for protective coatings to be applied to lightly cleaned or weathered surfaces, ensuring that the equipment remains operational while still being protected from further degradation. This application extends to machinery parts, steel beams, staircases, railings, and even flooring systems, where the need for a fast, reliable, and durable coating solution is paramount.
In addition, surface tolerant primers are useful for emergency repairs, where there is no time to perform extensive surface cleaning. A quick application of these primers ensures immediate protection, allowing the facility to remain operational until more comprehensive maintenance can be performed.
Construction and Infrastructure
The construction industry makes extensive use of metal components such as girders, beams, and other structural elements that are often exposed to outdoor environments during and after construction. Steel used in bridges, tunnels, commercial buildings, and skyscrapers is particularly susceptible to rust and corrosion, especially during the construction phase when surface preparation might be incomplete or rushed.
Surface tolerant primers offer a solution for protecting these materials in less-than-ideal conditions. Construction sites are often exposed to dust, moisture, and other environmental contaminants that make it difficult to achieve the high levels of cleanliness required for standard primers. Surface tolerant primers provide excellent adhesion to surfaces that have not been fully cleaned, ensuring that structural elements are protected from corrosion even before the final building stages.
In infrastructure projects, such as bridge construction or highway expansion, surface tolerant primers are applied to steel beams and supports to protect them from moisture, road salt, and pollution. Given the high stakes involved in these projects, where structural integrity and longevity are paramount, the use of surface tolerant primers ensures that steel elements remain strong and rust-free for decades.
Transportation and Infrastructure Maintenance
The transportation sector, particularly railways, bridges, and roadways, relies heavily on surface tolerant primers for protecting metal structures from environmental exposure and heavy use. Metal components used in railway tracks, bridges, street lights, and traffic barriers are continuously subjected to wear from vehicles, vibration, and weather elements such as rain, snow, and ice.
Railway companies use surface tolerant primers to coat tracks, bridges, and overhead metal frameworks to protect them from the adverse effects of moisture and corrosion. Metal railway bridges, for example, are constantly exposed to water, road salt, and mechanical vibrations from passing trains. Applying a surface tolerant primer extends the life of these structures by preventing rust and deterioration, which could lead to expensive repairs or replacements.
Similarly, in road infrastructure, bridges and guardrails are coated with surface tolerant primers to shield them from the corrosive effects of road salt, rainwater, and pollution. Bridges that are frequently exposed to water, such as those spanning rivers or coastal areas, benefit greatly from the corrosion resistance offered by these primers. In cities, where road infrastructure is constantly in use and needs to remain open, surface tolerant primers provide an efficient solution, allowing maintenance to proceed with minimal disruption to traffic flow.
Agricultural and Heavy Equipment
Agricultural machinery and heavy equipment used in construction, mining, and forestry industries are constantly exposed to dirt, mud, water, and chemicals. Surface tolerant primers are commonly used to protect these metal machines from rust and corrosion. Tractors, ploughs, combine harvesters, excavators, and bulldozers are often stored outdoors, exposed to the elements for long periods, making them susceptible to surface damage. Surface tolerant primers ensure that these machines remain operational for years, even with minimal cleaning and preparation before coating.
These primers are also valuable in preventing rust and wear on equipment that is in constant use in rugged conditions. For example, forestry machinery operates in wet, muddy, and sometimes corrosive environments, where surface preparation might be limited to removing dirt and debris. By applying surface tolerant primers, operators can protect their valuable equipment from rust and degradation, reducing the frequency of repairs and extending the overall lifespan of their machinery.
Power Plants and Utility Infrastructure
In power plants and utility infrastructure, metal structures are continuously exposed to chemicals, moisture, and harsh weather. Surface tolerant primers are used to protect metal components, such as cooling towers, pipelines, and transmission towers, which are often difficult to clean thoroughly due to their location and exposure.
For example, cooling towers in power plants are exposed to constant moisture and chemicals used in the cooling process, making them highly susceptible to corrosion. Surface tolerant primers provide a durable protective layer that withstands the chemical exposure and prevents rust from forming on these vital structures. Transmission towers, often located in remote areas or near bodies of water, face constant exposure to wind, rain, and salt. Surface tolerant primers allow these structures to maintain their strength and reliability, reducing the need for frequent maintenance or replacement.
In addition, these primers are used in hydroelectric power plants, where metal components such as turbines and dams are in constant contact with water. By applying surface tolerant primers, plant operators ensure that these components remain free from corrosion and continue to function efficiently for many years.
Water Treatment and Waste Management Facilities
Water treatment plants and waste management facilities handle large volumes of corrosive substances, including chemicals and wastewater, which can quickly degrade metal structures and equipment. Surface tolerant primers are commonly applied to metal tanks, pipelines, and equipment in these facilities to protect them from rust and corrosion. The primers' resistance to moisture, chemicals, and abrasion ensures that the equipment remains functional and safe for an extended period.
For example, metal tanks used to store chemicals in water treatment facilities must be protected from corrosion to prevent leaks or contamination. Surface tolerant primers offer an effective solution for coating these tanks, even when the surface preparation is limited to pressure washing or wire brushing. Waste management facilities, which often handle corrosive materials and are exposed to harsh environmental conditions, also benefit from the protective properties of these primers. Equipment such as conveyor systems, shredders, and compactors can be coated with surface tolerant primers to prevent rust and extend their operational lifespan.
FAQs
- Can surface tolerant primers be applied over existing rust? Yes, surface tolerant primers are specifically formulated to adhere to rusted surfaces, though it is still recommended to remove loose or flaking rust before application for the best results.
- Are surface tolerant primers suitable for all metals? While surface tolerant primers are primarily designed for steel, they can be used on other metals such as galvanised steel, aluminium, and iron, depending on the formulation.
- What are the environmental conditions for applying surface tolerant primers? Surface tolerant primers can be applied in a wide range of conditions, including high humidity, damp surfaces, and low temperatures, making them versatile for outdoor use.
- Can surface tolerant primers be overcoated with other products? Yes, many surface tolerant primers can be overcoated with topcoats designed for added protection or aesthetic appeal. It is important to check compatibility with the selected topcoat.
- How long do surface tolerant primers last? The longevity of surface tolerant primers depends on the environment and level of exposure, but they generally provide long-term protection, often extending the lifespan of metal structures by several years.
- Is surface preparation still necessary when using a surface tolerant primer? While these primers are designed to tolerate poor surface conditions, removing loose rust, flaking paint, and other contaminants is recommended to maximise adhesion and performance.
- Can surface tolerant primers be applied to damp or wet surfaces? Yes, many formulations are specifically designed to adhere to damp or wet surfaces, making them ideal for use in outdoor or humid environments.
- How thick should surface tolerant primers be applied? Surface tolerant primers are typically applied in thicker coats to ensure full coverage and protection. The exact thickness will depend on the manufacturer's guidelines.
- Do surface tolerant primers require a specific type of topcoat? The choice of topcoat depends on the exposure conditions and performance requirements. Some surface tolerant primers are compatible with a wide range of topcoats, including epoxy, polyurethane, and alkyd systems.
- What industries benefit the most from surface tolerant primers? Industries that face challenges with surface preparation, such as marine, oil and gas, construction, and infrastructure, benefit significantly from using surface tolerant primers due to their high performance and durability in harsh conditions.